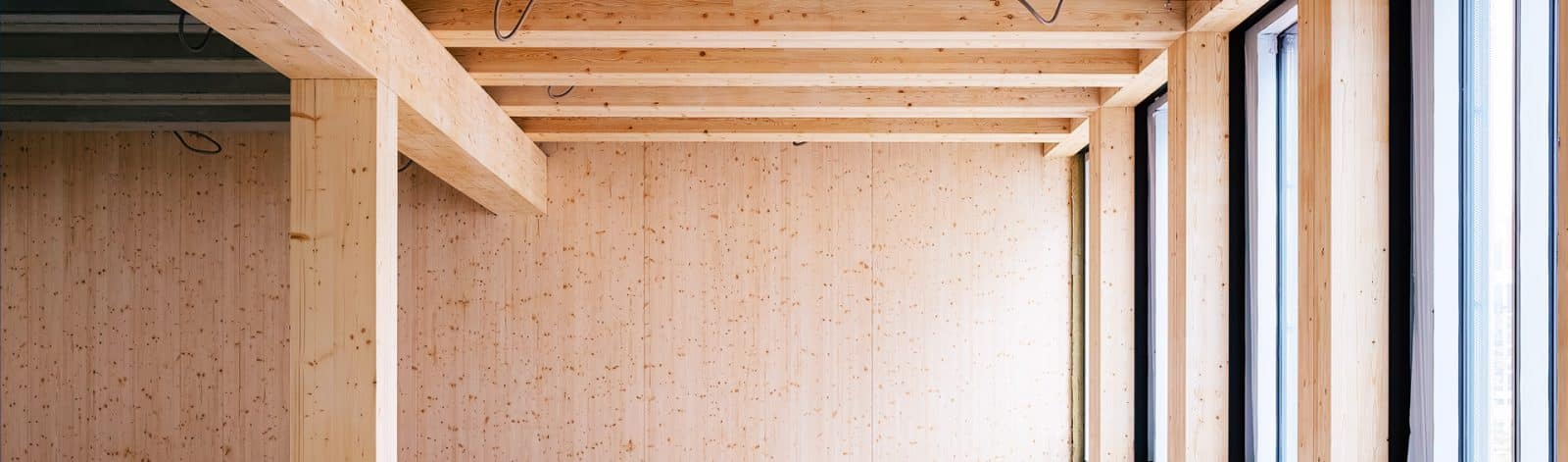
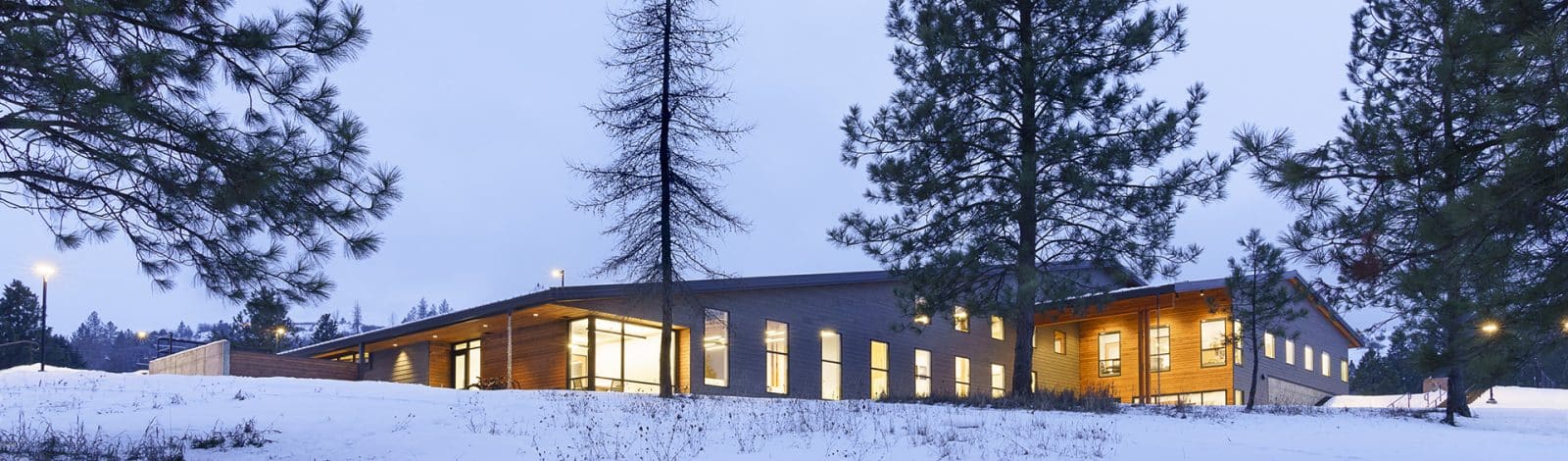
3 Strategies for Effective Mass Timber Design
Design with Mass Timber in Mind
In recent years, the use of mass timber design in projects of all types has exploded across the United States. You may have heard in the media or from other sources that mass timber is sustainable, renewable, and as strong as steel. While this is true to a certain extent, it is important to understand mass timber’s strengths while taking the time to understand its limitations.
Because mass timber is frequently talked about as being as strong as steel, there is a common misconception that mass timber products are equivalent to steel. This can sometimes lead to expectations for equivalent performance between steel and mass timber construction.
However, because steel’s weight/density is 15-16 times more than the wood used in mass timber projects, they aren’t a 1:1 replacement. Wood has similar strength to steel per pound, but because of the density difference, we need a lot more volume of wood to achieve equivalent strength performance. Therefore, designing mass timber buildings in the same way as a typical steel building requires deeper members, which increases the height and cost of the building overall and results in less efficient buildings.
If you want to reap the benefits of using mass timber materials, we have found that designing your project from the outset with mass timber in mind sets you up for success.
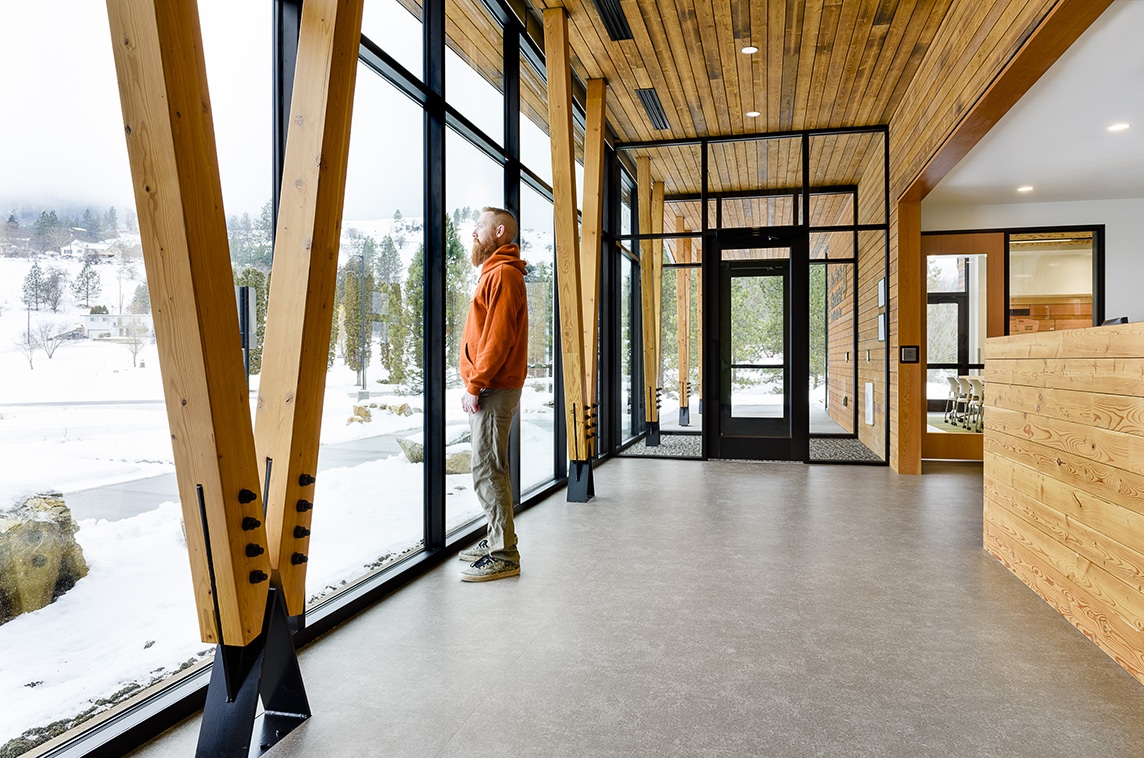
Efficient Mass Timber Design
Starting a project with the intention of using mass timber products will allow designs that maximize its benefits. Constructing well-designed mass timber design projects can be a fast process. Large mass timber roof and floor panels can be lifted into place and set quickly in the field, which can help reduce construction schedule and labor costs when compared with steel, concrete, and stick framed wood construction.
Conversely, irregularly shaped buildings that do not feature repetitive panel layouts may not go up as smoothly and efficiently with mass timber. Because mass timber materials often come at a cost premium, not maximizing the schedule and labor benefits of mass timber may result in budgetary pressure on projects.
Additionally, an efficient and cost-competitive multi-story mass timber building will have more columns than an equivalent steel building. Swapping wood beams for steel beams with the same span length will result in wood beams that are often as much as twice the depth of a comparable steel beam. This ultimately increases the floor-to-floor height of the building, which can increase costs. Therefore, the only way to get a mass timber building that is as open as a steel building is by potentially paying a premium for it, which is why a lot of mass timber projects may not pencil out financially.
Our Buildings Structural Engineers Have Joined SE 2050. Learn More About this effort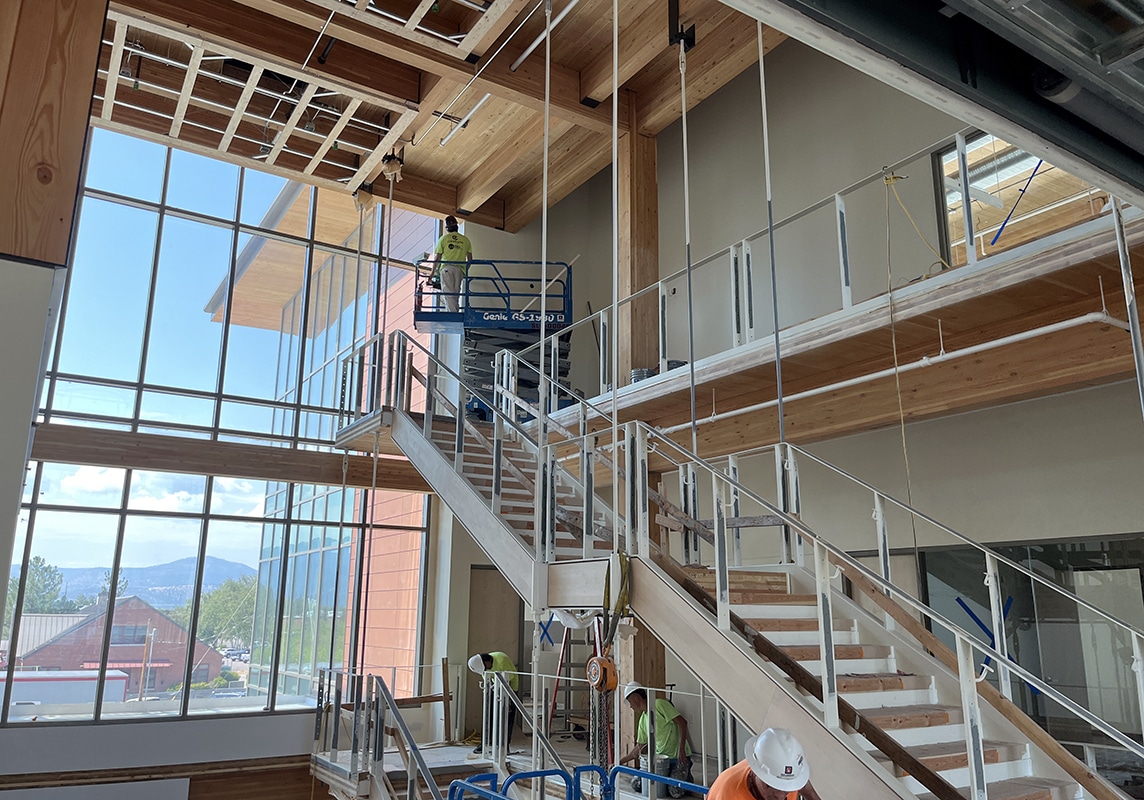
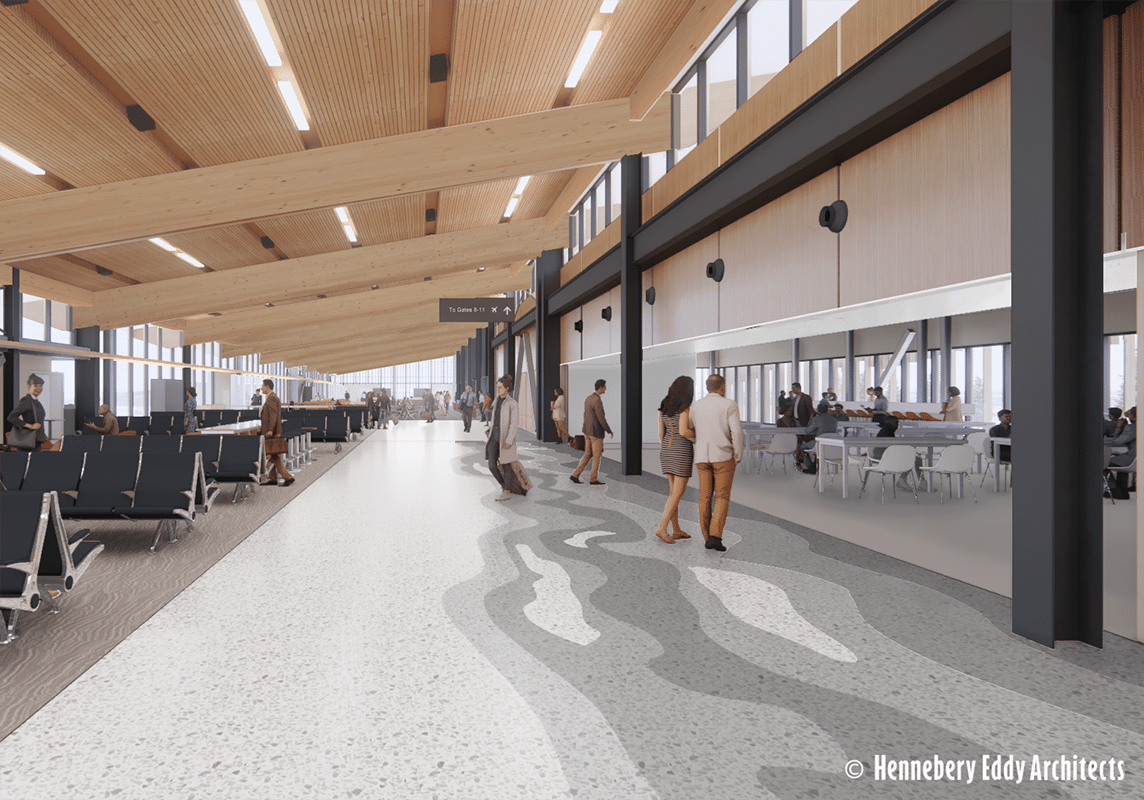
Mass timber design tips
Here are a few tips to increase efficiency and open concepts with mass timber design.
Increase efficiency with a hybrid design
One of the best ways to achieve the free-flowing open concepts of steel structures with mass timber is a hybrid design. A hybrid steel-mass timber structure typically consists of steel beams and columns with a mass timber floor and/or roof and can be a good compromise of cost and aesthetics. With this hybrid method, it’s possible to save a lot of the construction schedule and labor savings by using mass timber panels.
Because steel beams can be spaced further apart and with shallower depths, buildings can have more open flow throughout the spaces. This also provides added flexibility, as too many columns can make it challenging to rework the space. One of the often overlooked aspects of sustainability is that the more a building can be reprogrammed and reused, the more sustainable it becomes because the carbon embodied in the structure remains in the structure and not in the landfill or recycling facility.
An additional benefit of hybrid design is simple, strong beam-to-column connections. One of the things we often see in mass timber design is that, at some point, the connection capacities of beams to beams or beams to columns can control the maximum spacing of the beams and columns. This consideration is not a concern in hybrid structures.
Finally, hybrid structures minimize the amount that the structure wants to “creep” or continue to deflect downward over time. Wood tends to creep while steel does not, so accounting for the effects of creep to ensure long-term floor flatness and levelness is a good consideration when designing a traditional mass timber building. In comparison, hybrid structures have far fewer risk factors for creep, such as long-term slab cracking.
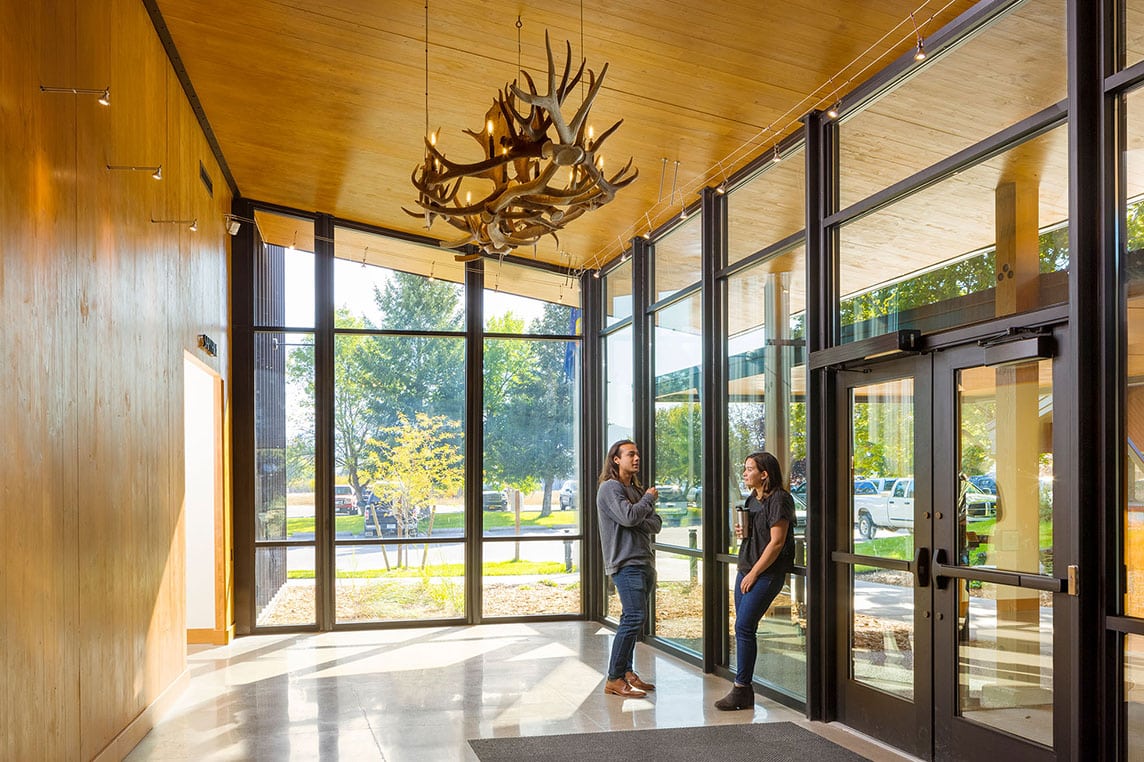
Maximize mass timber’s benefits using chases
Designing with chases maximizes what we all love about mass timber—the aesthetics—by keeping exposed wood ceilings and roofs uncluttered.
This method works by putting a one-to-two-foot gap between panels and then sealing off the top with plywood. By doing this, it’s possible to pour a concrete or gypcrete floor or install roofing above the plywood. This creates a chase in the floor/roof that allows you to tuck electrical, communications technology, and even fire sprinklers into the chase. This provides future flexibility over the traditional method of burying conduit in the concrete slab on top of the mass timber and is less expensive (although less flexible) than providing a raised access plenum for utilities above the floor. Burying conduit in the concrete topping slab increases the likelihood of cracking of the slab—so in a building with exposed concrete floors, it’s a good idea to consider the aesthetics of the top and bottom of the floor assembly.
Using chases between panels not only provides added flexibility, but the utilities are far more accessible. It’s worth noting, however, chases within the mass timber panel depth are not necessarily deep enough for all utilities, especially ductwork.
One of the ways we have found to maximize the available space to run ducts and other utilities without obstructing the mass timber floor/roof above is to create a central corridor in the building with columns spaced on either side of the corridor to minimize the span of the beams that support the mass timber panels over this corridor. In some cases, we have even been able to recess the beam into the depth of the mass timber panels so that the corridor is free of obstructions over the entire length, making MEP equipment easier to route and resulting in a better-looking product.
We have used both chases between panels and corridor chases successfully on the Headquarters Building of the City of Bend Public Works Campus. On this project, we worked with our client and owner to use a steel beam upturned into the depth of the CLT panels to provide an unobstructed corridor. We are taking a similar approach between panel chases on the design of the new Redmond, Oregon Airport Terminal and have been holding numerous brainstorming sessions with the design team to learn ways to distribute air into the space with minimal visual impact on the mass timber aesthetic.
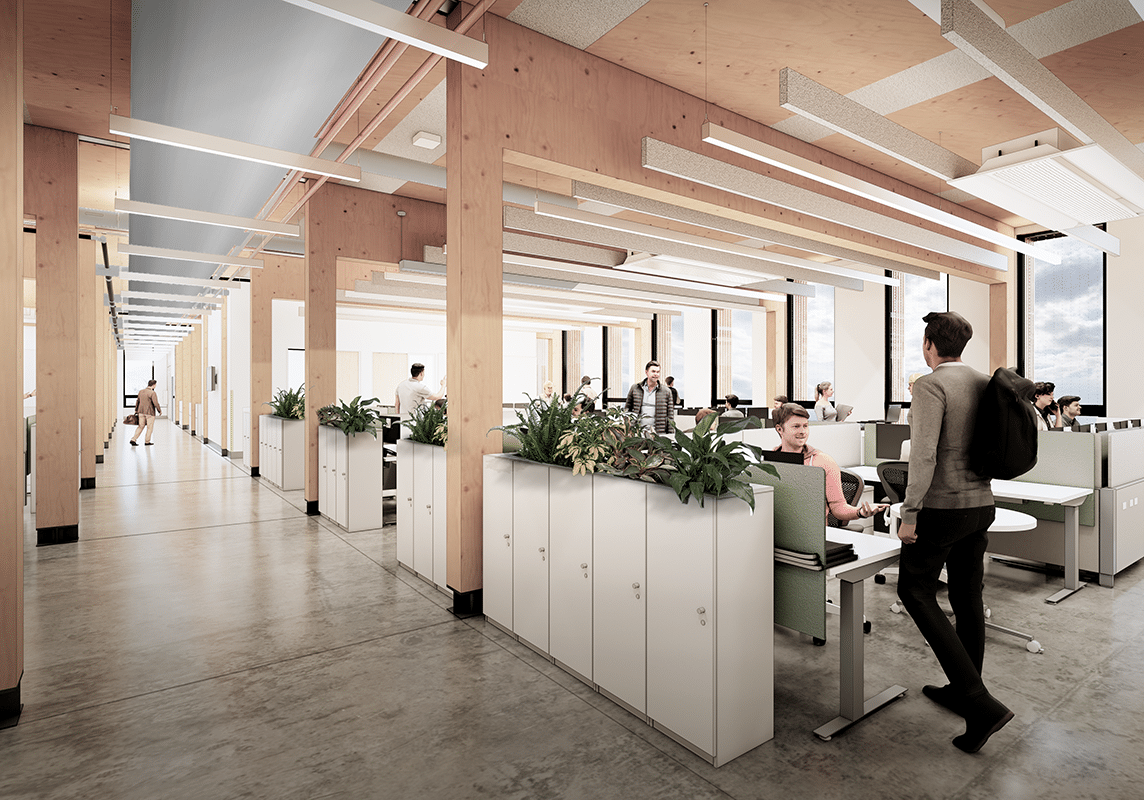
Save time and money with construction manager general contract (CMGC) design
For several reasons, we highly recommend using CM/GC (construction manager/general contractor) or design-build delivery methods when using mass timber in projects. These project delivery methods allow the design phase to begin with column spacing assumptions based on common panel sizes, allowing designers to quickly refine them once the supplier is selected by the GC and typically before the midway point of the design phase.
Typically, floor and roof panels should span continuously between two, three, or even four beams to maximize the strength of the mass timber panels. So, column spacing will depend on the panel dimensions of the selected manufacturer, depending on panel type (CLT, DLT, GLT, Mass Plywood) and supplier. One of the early goals in design is to minimize panel waste (i.e., cutting panels down from the dimensions they are most efficiently fabricated or shipped). Since panel waste is part of the construction cost, less panel waste means less mass timber cost. Therefore, the earlier a mass timber provider is selected, the earlier an efficient column grid can be established, which can save the project money.
With hard bid projects, we have found that it’s best to plan for multiple scenarios with a performance specification that sets minimum strength and serviceability parameters and allows multiple suppliers to bid on the project. There is a risk of redesigning here because when the supplier isn’t involved until late in the construction documents phase, design decisions, like column grid spacing, might not work with the selected supplier. Conversely, with a CMGC design approach, once a mass timber provider is selected, designs can be adjusted to work with their standard sizes, ultimately saving time and money.
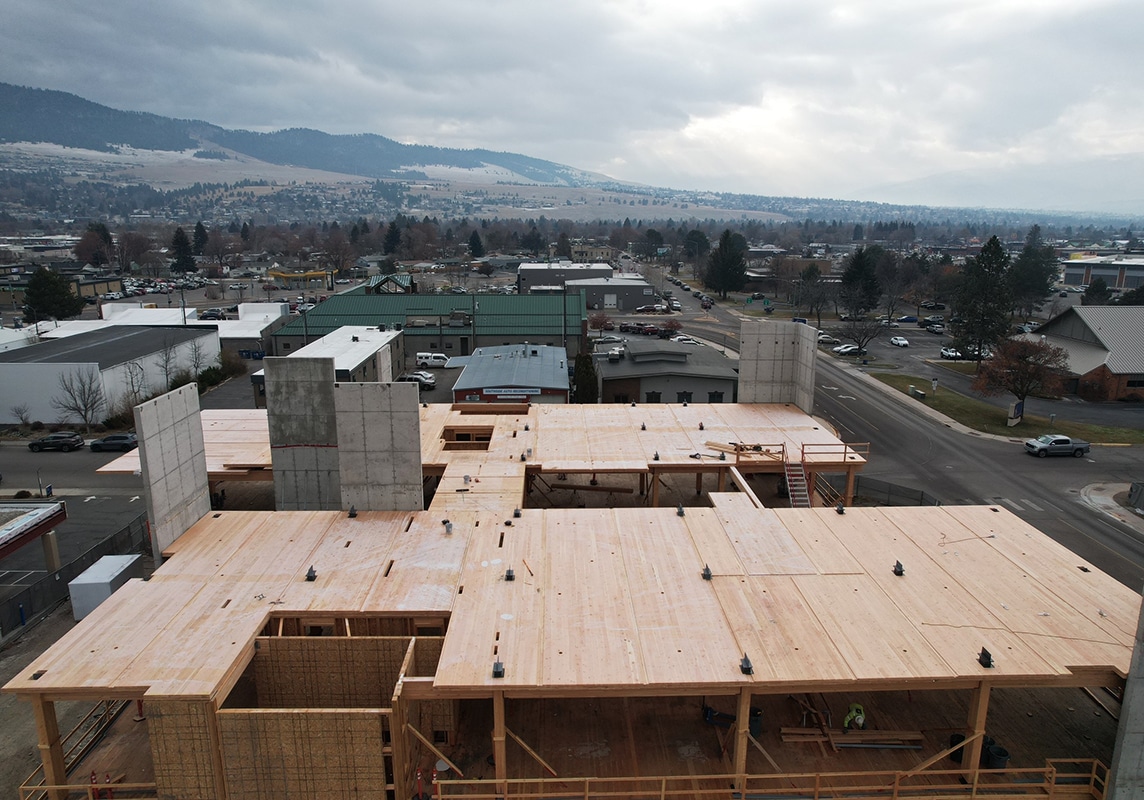
Our Passion for Mass Timber
We enjoy learning new things about mass timber and are excited to continue creating innovative and sustainable solutions. Over time, we have no doubt that mass timber will become an increasingly cost-competitive option.
We hope these three tips help you get started, and there’s more to come! Check back to learn more as we continue our mass timber series. Our doors are always open for questions and to address concerns involving mass timber solutions.
Contact Eric to learn more about our mass timber capabilities.