
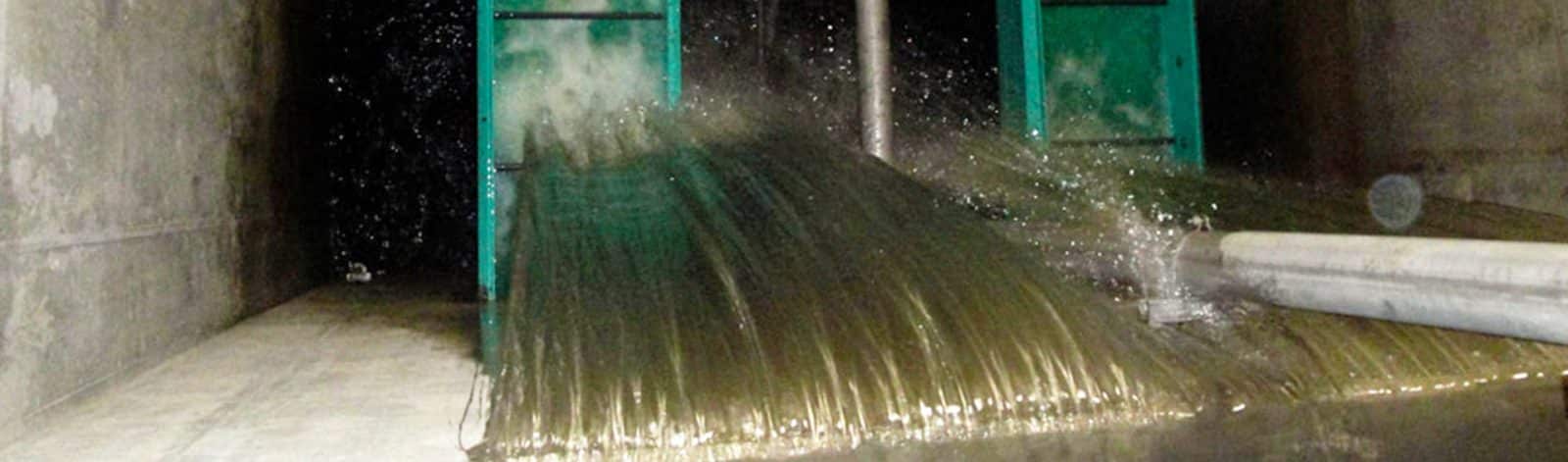
Avoiding Pitfalls: Commissioning Water Treatment Plant Rehab and Retrofit Projects
By Jeff Ashley, PE
The design and construction of a water treatment plant is a collaborative effort between engineers, owners/operators, contractors, manufacturers, regulators, and funding agencies. While the design responsibilities lie with the engineering team, typically, the contractor and manufacturers work with plant operations staff during the commissioning phase.
Commissioning demonstrates that the water treatment plant processes, as designed and constructed, will operate reliably to meet drinking water standards. The commissioning process is even more complex when the project involves rehabilitating certain plant components and retrofitting the plant with new processes and equipment.
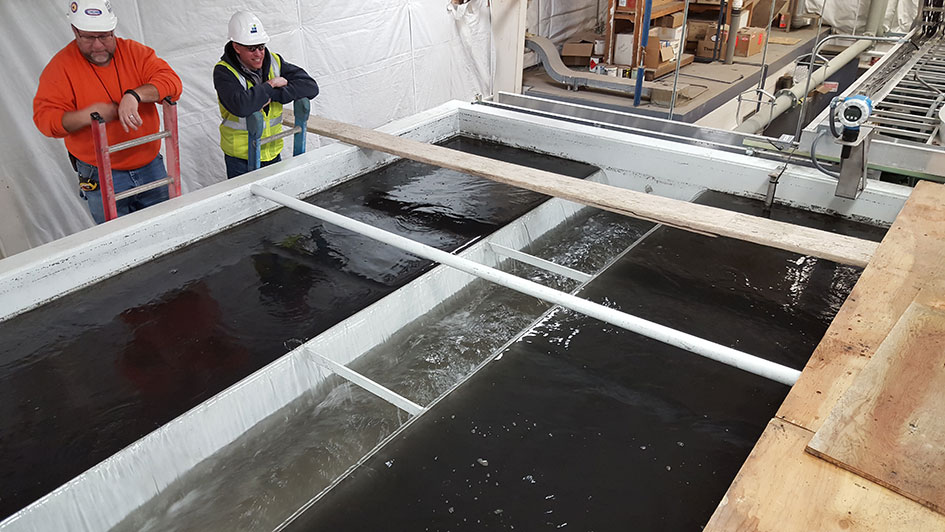
Regardless of the project delivery method, in order to successfully commission a water treatment plant rehabilitation and retrofit project, proper planning in the design phase is critical, and plant operations staff must be included in the planning. Additionally, key members of the design engineering team must be involved in commissioning and process implementation. In design-bid-build project delivery, the contractor and manufacturers are contractually responsible for a complete and functional system following construction, but without a “road map” in the contract documents, and without design team and operator engagement throughout the project, several issues can arise.
Some of the more common problems may include:
- The project is bid without a clear plan on what processes must be built and commissioned first. A clear plan creates clarity, promotes coordination, helps build relationships, and avoids eventual change order costs for the owner.
- There is no clear understanding of who is responsible for coordinating the commissioning process. With poor or no planning, the engineer may assume the contractor is in charge. If there is insufficient information in the contract documents, the contractor may assume the manufacturer, engineer, or owner will be responsible and not provide staff and budget to accomplish the tasks.
Planning is Everything
In addition to problems with bidding documents and questions on responsibilities, project teams without commissioning plans can encounter other stumbling blocks related to sequencing. For example, equipment may be commissioned randomly during construction without considering sequencing with other existing and new processes and equipment. When equipment is commissioned too early or out of sequence, specific training tips, important performance testing, and process adjustments often are not properly completed. When performed too late, these tasks and actions are often rushed, resulting in incomplete work.
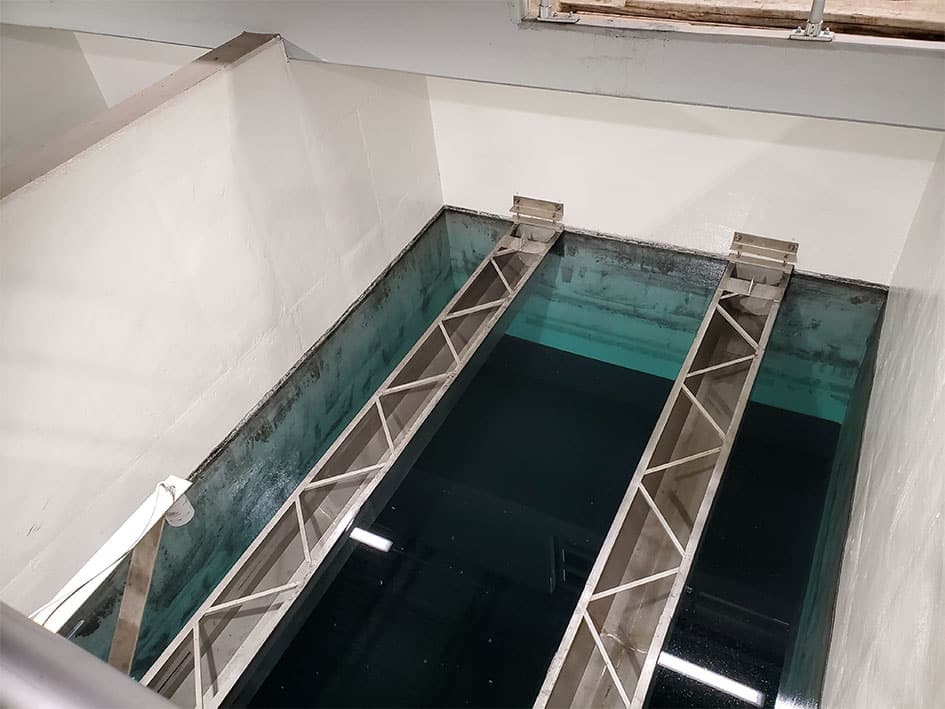
Which Comes First? Which Comes Last?
How do we integrate all the various processes in the proper sequence and consideration of existing processes? For example, process residual basins need to be online before filter commissioning to discharge the filter to wastewater. During testing and initial operation, the filter-to-waste process may result in additional water volume and pumping from the residual basins that exceed pre-construction conditions for existing basins. Ask yourself: Is this accommodated in the planning? How will existing basins and pumping systems function under the testing conditions?
Other issues with electrical, controls, and instrumentation often arise without a proper commissioning plan. These systems must be online before treatment processes are commissioned, and electrical sub-contractors should be properly scheduled into the overall construction schedule.
Out with the Old, In with the New
Teams should also consider how new systems that replace old systems are brought online in a retrofit project. For example, replacing existing equipment with a new gas chlorine system can be challenging. The existing system must remain in use before a “switch” can be made and cannot be taken offline or demolished until the new system is commissioned and ready for use. If there are setbacks in this conversion process, the owner may be at risk of non-compliant water being sent to the community.
Oftentimes, rehabilitation and retrofit projects include a complete electrical and control system upgrade. This may require new equipment installed with new systems and older equipment to be phased from the old to the new system at the appropriate time. This type of process warrants careful planning in the design process to develop a proper sequencing plan.
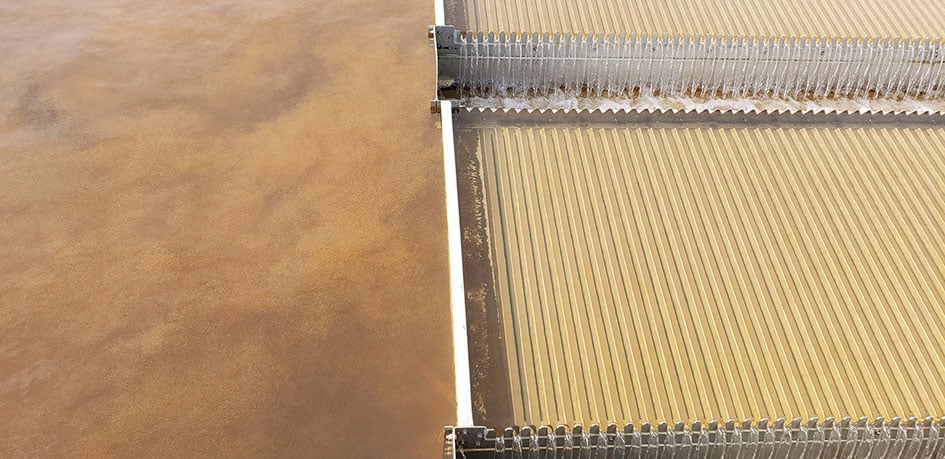
The Case for Communication
Without design engineering team support during construction, the construction inspector can interpret the commissioning plan and make decisions, typically without all the background information that went into the design. Furthermore, without operator input during design, operations staff may have no idea what is taking place and their responsibilities during commissioning.
These issues can all be avoided in rehabilitation and retrofit projects with proper planning and execution guidelines. See my next article for some helpful hints with water treatment plant commissioning.