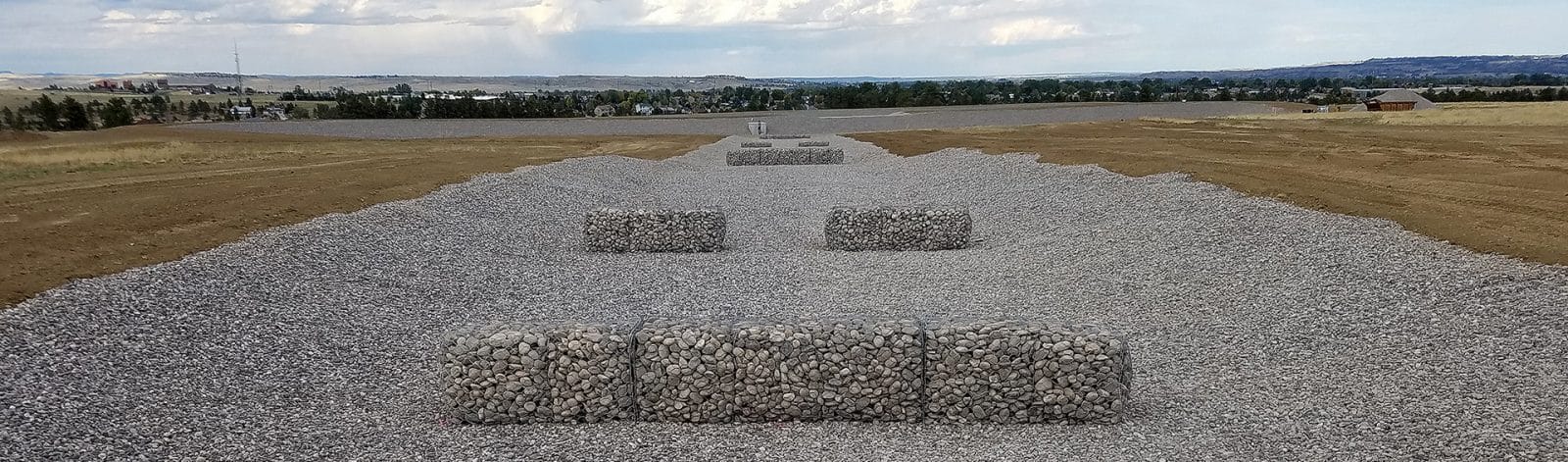
Billings Airport Storm Drainage System
Stormwater Solution for a Busy Airport
Billings-Logan International Airport hired Morrison-Maierle to come up with a solution that included a multi-phased project better to control the large stormwater events on the airfield, detain the large volume of water in a new pond structure, and drain the ponds through an underground pipe — at a predetermined rate — to nearby creek drainage.
Phase 1 included two 48-inch tunnel bores installed under the main air carrier runway to alleviate mid-field ponding and water flowing over the runway during large storms. This also required the team to find a way to directionally drill a 30-inch pipe down a 130-foot sandstone cliff at a 30% slope.
Phase 2 included installing underground piping from the airport’s north side to the Alkali Creek drainage and building large stormwater detention ponds near the existing Pond D structure.
As a result, the Billings airport is now ready for storms of any kind with a system that can effectively move water from the airfield to a nearby creek.
Services & Highlights
-
Design engineering
-
Construction administration
-
Combination of tunnel boring and motor drilling
-
Bentonite pond liner
-
Permitting
-
Use of hobas pipe as a stong, rust-free option
A Two-Phased Approach
Phase 1 consisted of a new approach to installing a pipe under a runway. Microtunneling was used at the airport in 1990, but after completing a cost analysis, the Morrison-Maierle team found that it was three times more expensive than tunnel boring. The design team found information on tunnel boring of the size and type of pipe needed, the procedure, the cost, and contractors who can do this work. This was the longest tunnel boring operation — at the 48-inch size — done by the contractor and their equipment.
The permitting and easement processes took significant time, as getting the pipe installation connections to Alkali Creek was difficult. The team also spent time making careful decisions that would help control erosion, considering the amount of stormwater that would enter the detention ponds. After considering several methods, the team used a bentonite pond liner with a honeycomb, a three-dimensional structure made of plastic fabric, and filled with rocks and concrete, as an erosion control method.
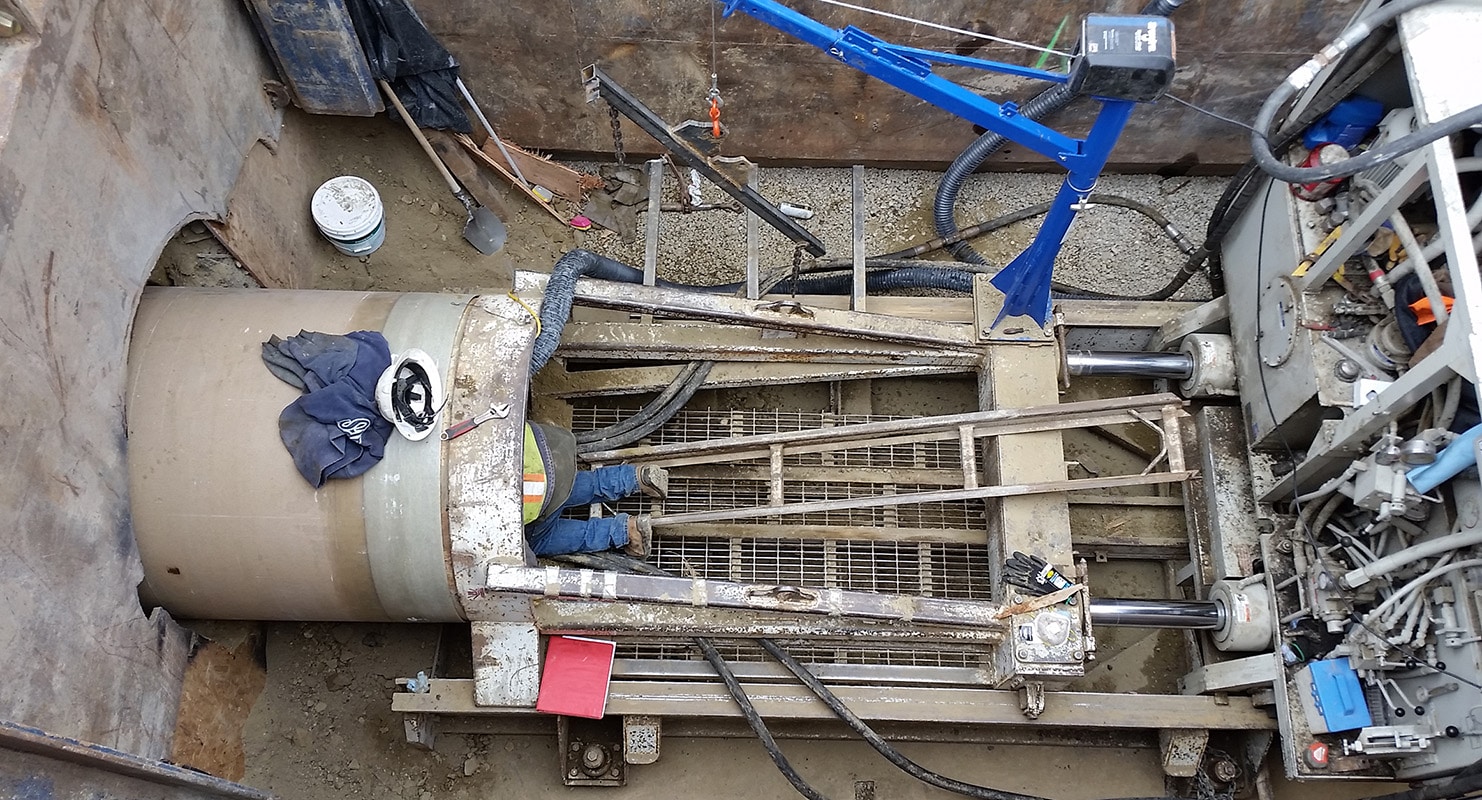
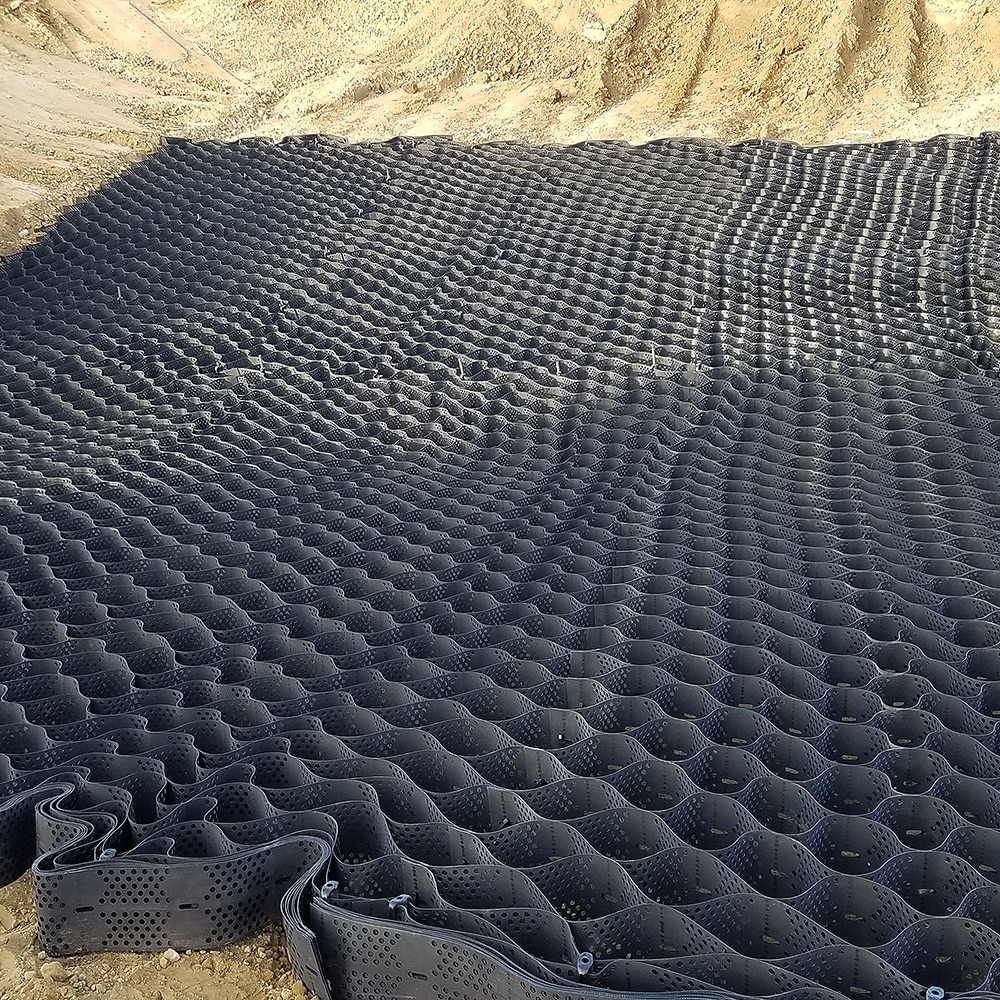
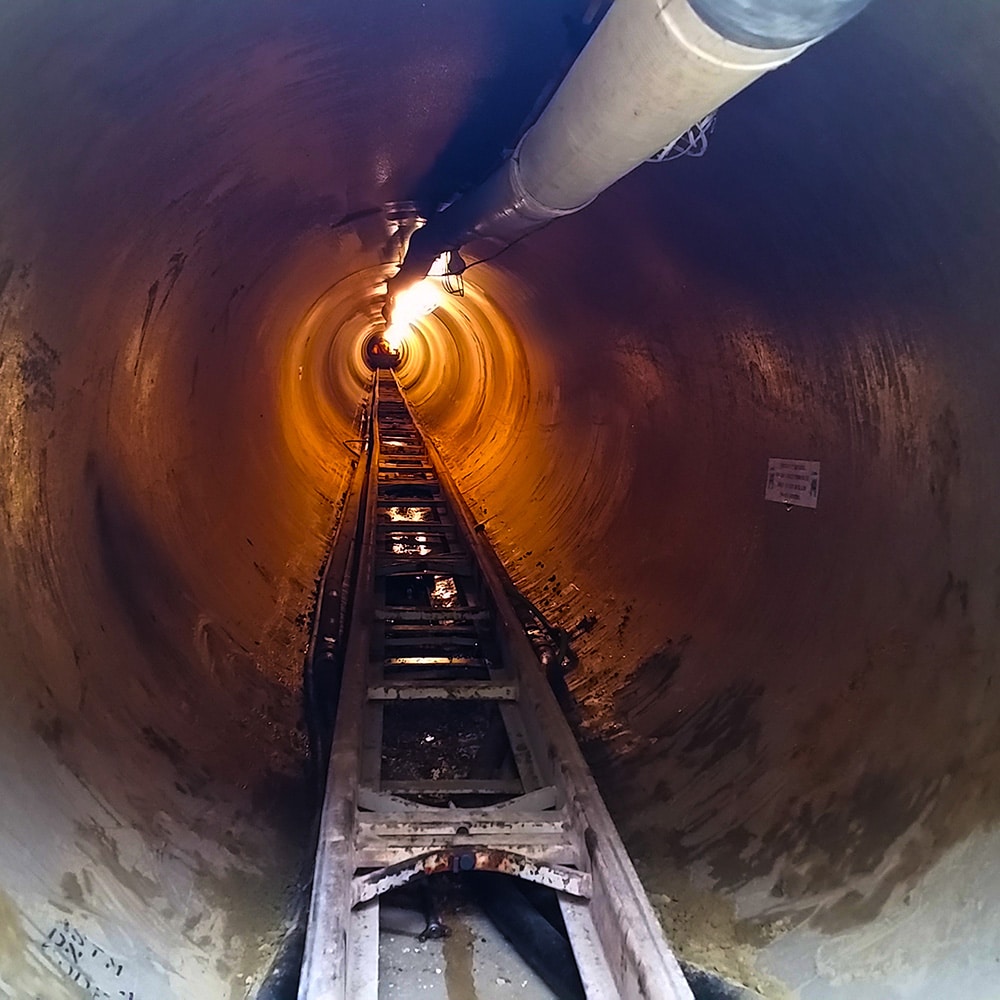
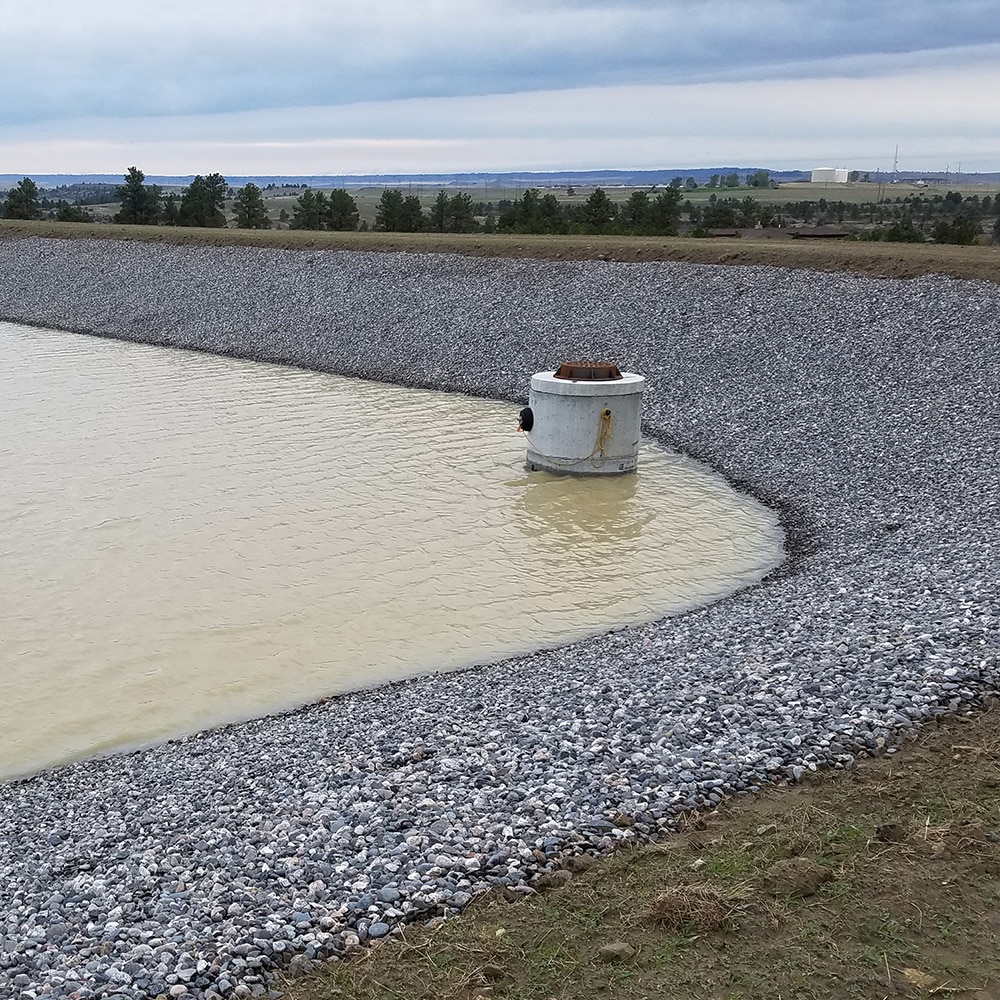
In preparation for future developments at and around the airport, Morrison-Maierle also designed open channel structures to capture stormwater on the northeast side of the airport that directed the water to the detention ponds. As the project progressed, the tunneling boring option took longer to complete but was still a third of the cost of micro tunneling, which kept the project within budget. As a result, Morrison-Maierle was able to use a larger pipe under the runway. A 48-inch pipe is the smallest size that can be used for tunnel boring. The larger-sized pipe will also help with future development and stormwater issues.
Finally, the design team placed the outfall pipe down the airport’s north side to Alkali Creek. This final location was determined after Morrison-Maierle considered cost, the adjacent private land, slope, and access. The pipe required an easement from the adjacent property owner and right-of-way easements from the county and city for the discharge pipe. Morrison-Maierle worked with many entities on the owner’s behalf.
Related Projects
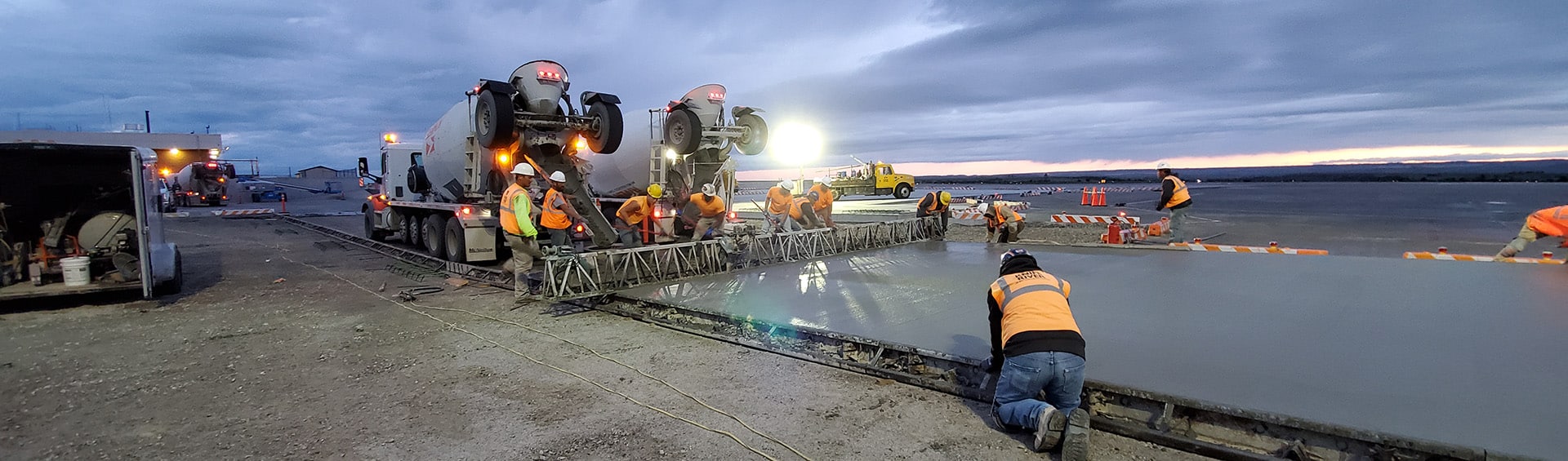
Billings Airport Commercial Apron Construction
Billings Airport Commercial Apron Construction
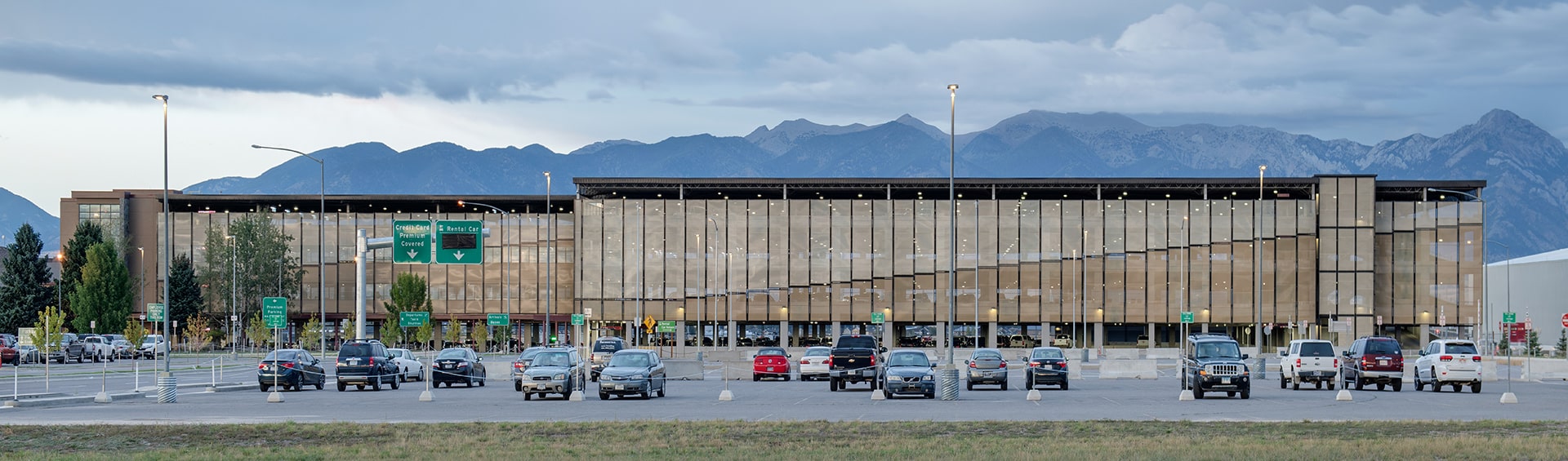
Bozeman Yellowstone Airport Parking Garage
Bozeman Yellowstone Airport Parking Garage
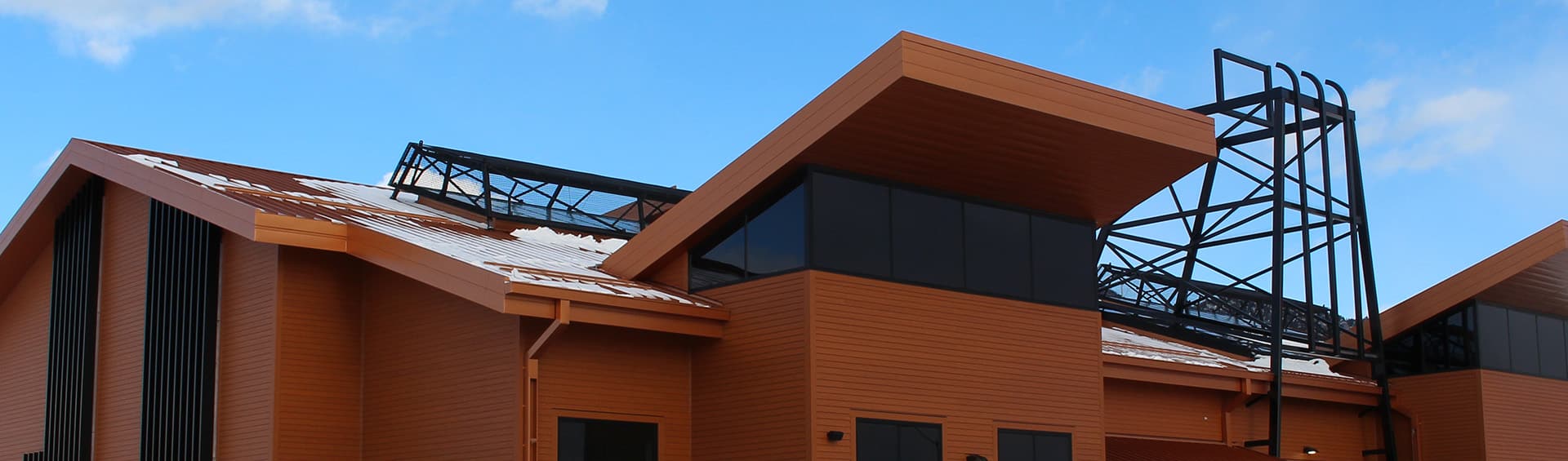
Bert Mooney Airport Terminal
Morrison-Maierle was the prime consultant on this project and was hired to design the site civil, mechanical, electrical, plumbing, and structural engineering for the Bert Mooney Airport.