
Fort Knox Mill Modifications Cyanide Mixing System
Updating an Old Facility for a New Purpose
Fort Knox is an open-pit gold mine near Fairbanks, Alaska. The mine uses conventional open-pit methods, with ore processed at a mill and heap leach facility. The Fort Knox process plant needed to undergo modifications to make it possible to process ore from both Fort Knox and another site: Manh Choh, a gold deposit 160 miles away in Eastern Alaska.
Kinross Gold hired Morrison-Maierle’s industrial team to help with its mill modifications project, which improved the existing mill complex so that it could batch process both Fort Knox and Manh Choh ore through the mill. The mill modifications project was divided into 10 subprojects, including the cyanide mixing system.
Services and Highlights
-
Civil engineering
-
Structural engineering
-
Mechanical engineering (process and HVAC)
-
Electrical engineering
-
Instrumentation and controls
-
Fire suppression
-
New cyanide mixing process and building
-
Piping infrastructure
-
Cyanide solution (CNS) supply line
-
Flushing and purging mechanisms
-
Process air receiver
-
Cyanide solution return
-
Air and water stations
-
Sump pump system
-
Safety shower/emergency eyewash stations
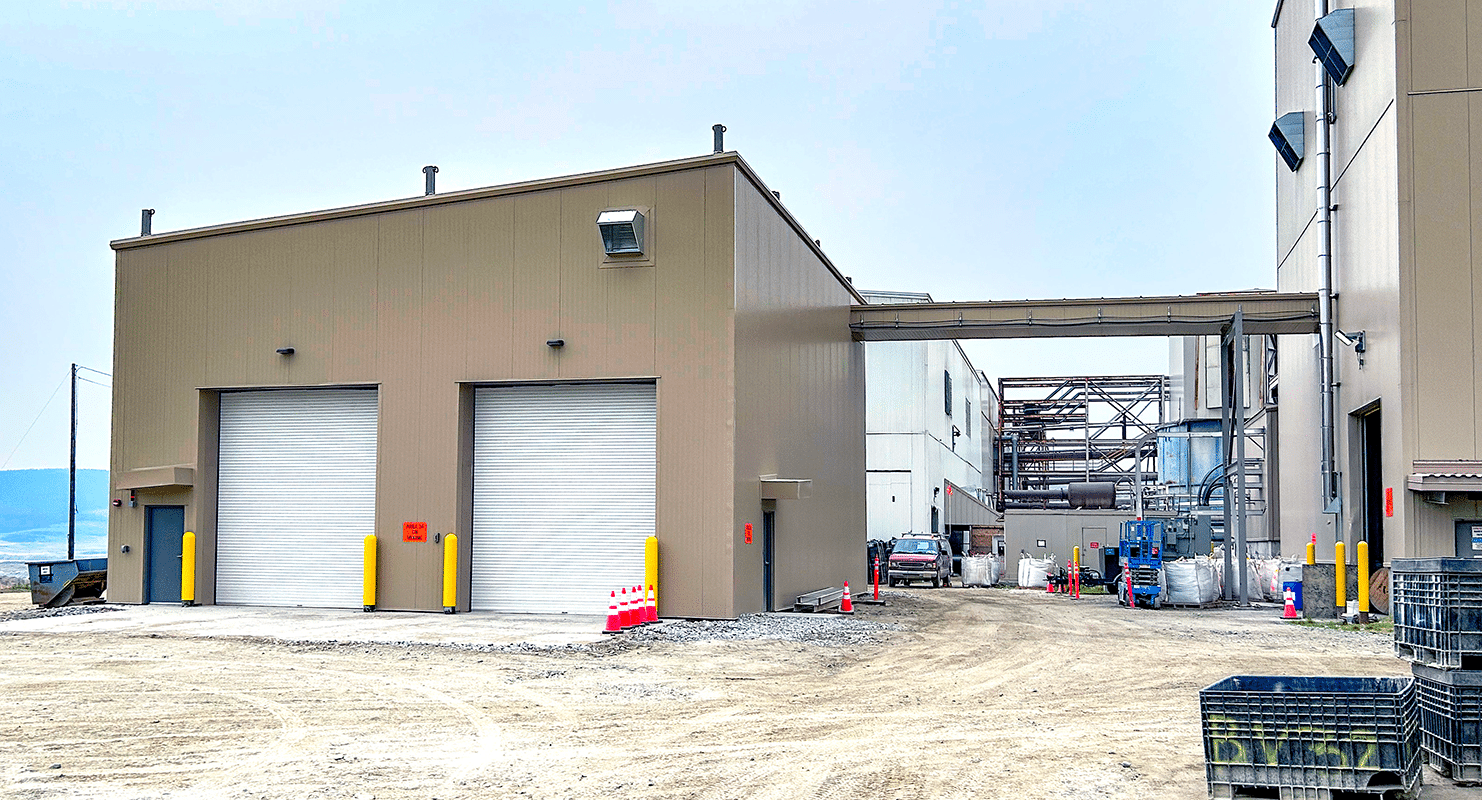
A New Method
Before this project, the Fort Knox Mine processed ore in two primary streams: high-grade pit ore and ore from the Mahn Choh Mine and run-of-mine ore placed on the Walter Creek and Barnes Creek valley-fill heap leach pads. Cyanide (CN) solution is used to recover both ore streams.
The former cyanide mixing method at the mine involved adding sodium cyanide briquettes, process water, and caustic solution to the CN mix tank. Once added, the cyanide mix tank agitator mixed the briquettes into solution. Following mixing, the resulting solution in the cyanide mix tank was then pumped to the cyanide storage tank.
The mill modifications project introduced a new method for cyanide delivery. With this method, sodium cyanide briquettes are brought to the site in ISO containers on tractor-trailers and are then mixed/dissolved using process water recirculating between the ISO container and the cyanide mix tank.
The new mixing process includes adding 14,000 gallons of process water to the existing cyanide mix tank, which is then pumped through the ISO container and back into the cyanide mix tank, creating a mixing loop between the cyanide mix tank and the ISO container. This process takes between 3.5 to 6 hours, depending on the temperature of the process water. The goal is to dissolve the briquettes into a 24% cyanide solution. Once the mixing is complete, the sodium cyanide solution is purged from the ISO container and into the cyanide mix tank with process air.
During the mixing/offloading operation, the ISO containers are parked in a steel building structure with two pull-through bays, known as the Cyanide Mix Building. The building has concrete containment slabs and turn-up curbs to meet the International Cyanide Management Code requirements for secondary containment of 110% of the volume of the largest tank or vessel. The roof and walls are constructed with all-weather insulated panels, and the design allows for heating and air exchange to meet health and safety codes.
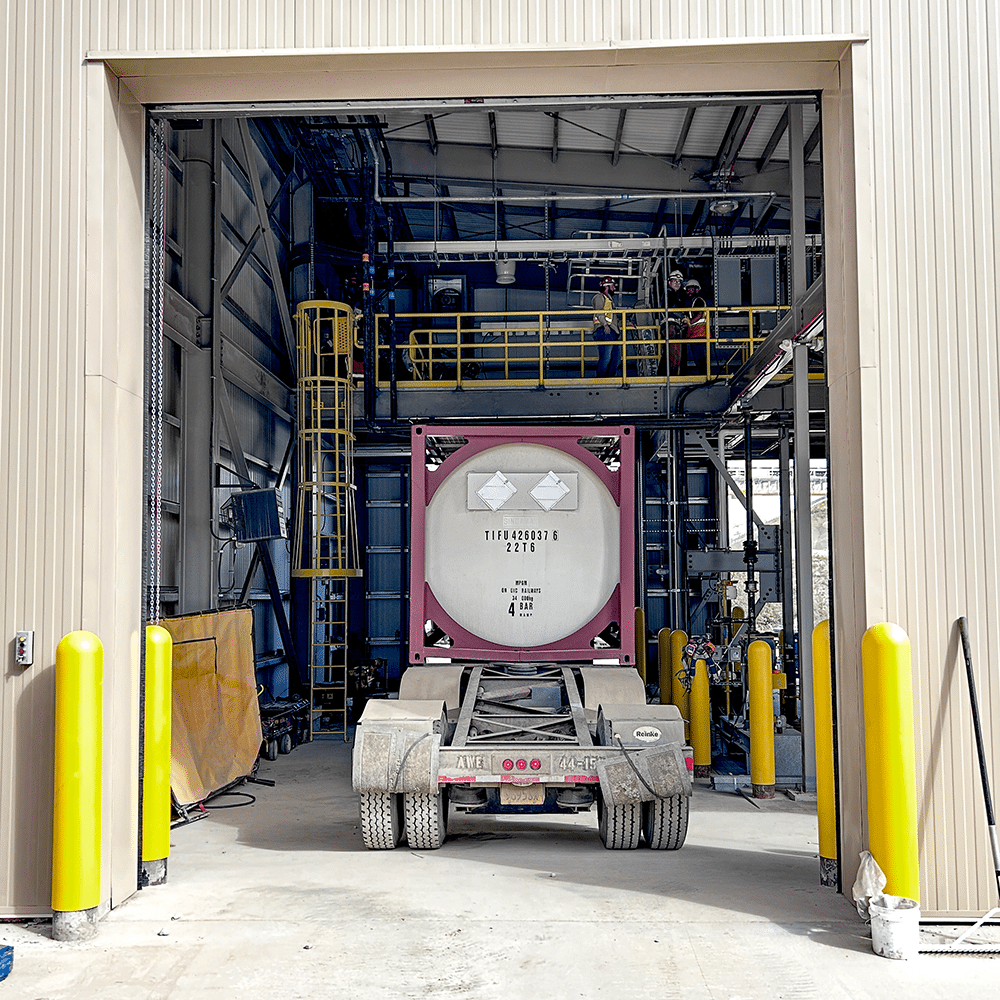
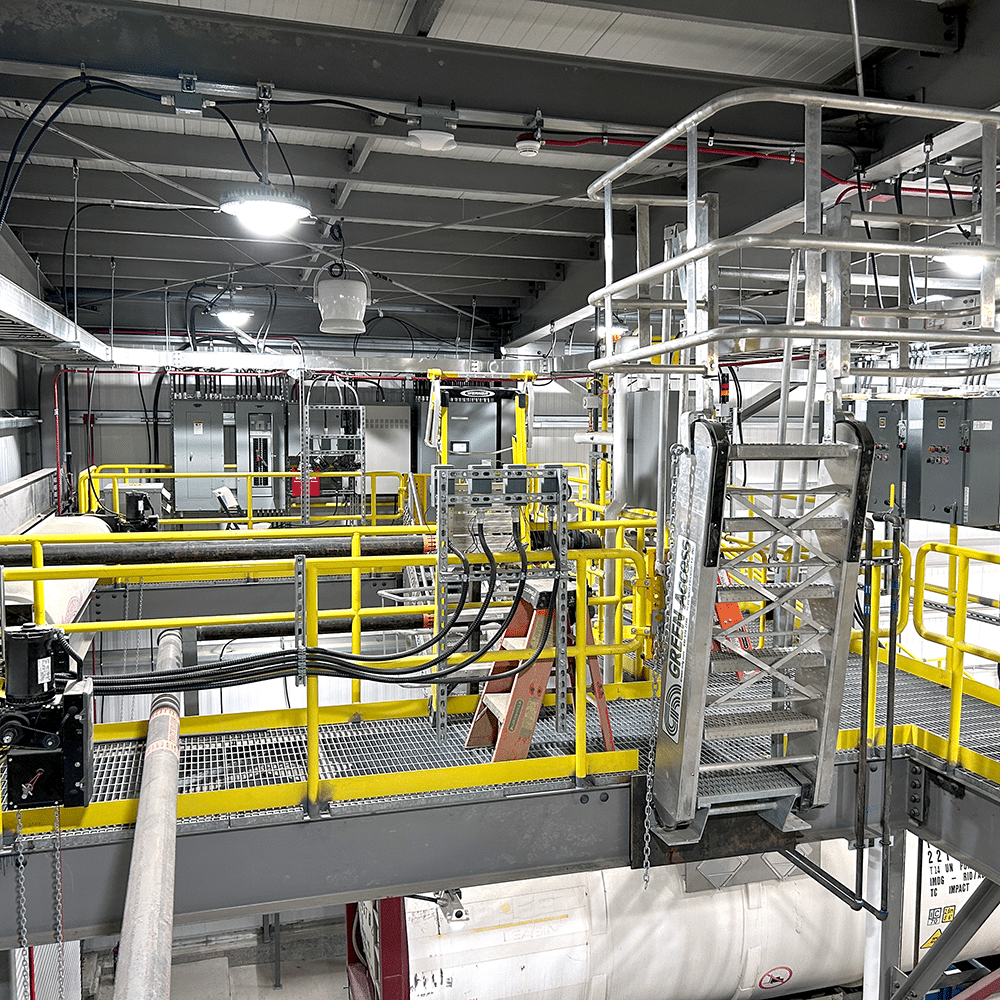
A Safer and More Efficient Cyanide Mixing System
To prevent the accidental release of the cyanide solution into the environment, we used a variety of containment strategies and safeguards. These included:
- Turn up curbs and slab grading to store 110% of the ISO container’s volume.
- Hydrophilic water stops, PVC plastic or sealant material is put in concrete joints to make them watertight.
- Sump pit, a concrete holding area cast into the concrete slab that will store solution if a tank or pipes were to rupture. The sump pit can also be used for cleaning and maintenance, as you can spray down the facility, drain the water into the pit, and then pump it out later.
ISO containers make the overall process safer for truck drivers, the traveling public, plant operators, and employees. The new mixing method uses mixing in double-walled tanks instead of ones that are open to the building and uses automated remote control of many tasks instead of manual operation.
The industry is doing more to safeguard the use of cyanide, and the mill’s use of ISO containers is a good example. With this new mixing system, liquid cyanide does not need to be transported on roadways, reducing the risk of trucks wrecking or getting punctured in transit. Because cyanide arrives in solid form, the dangerous portion (mixing with liquids) occurs in a building designed to handle that process.
Using ISO containers allows the mine to safely mix more sodium cyanide at once, ultimately saving time and money. And because the system is automated, it switches the process from performing to monitoring, reducing the number of staffing hours required to operate the plant. This is especially beneficial as workers at the mine must wear a full hazmat suit while manually mixing the cyanide solution in the facility.
Anytime gold process uses cyanide solution, safeguarding against accidental release to the environment during operations is paramount. To achieve this, we followed several codes. The first is the International Cyanide Management Code, a voluntary code dictating high safety standards for cyanide-using facility design, construction, operation, and maintenance. In addition, we followed the ACI 350 Specifications for Environmental Concrete Structures. This environmental code dictates how to design a structure safely to reduce cracking in slabs and walls and eliminate leakage. With twice as much reinforcement required to meet the code, this increased project costs but improved overall safety and containment standards.
We reduced overall environmental impacts by reusing an existing facility instead of building a new one to process Manh Choh ore. As a result, Kinross could also easily repurpose the cyanide mixing system and storage tanks with the added benefit of increasing storage capacity.
Learn more about our industrial capabilities.