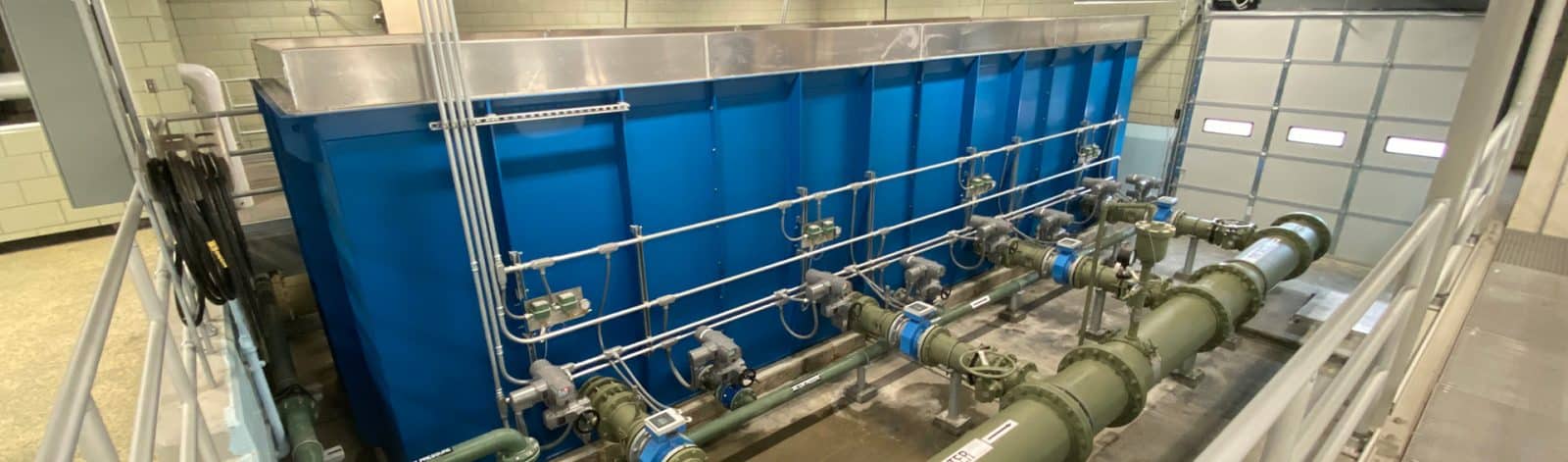
Glasgow Water Treatment Plant
Expansion in an Existing Footprint
The City of Glasgow’s former water treatment plant was a groundwater softening facility built in 1966 when the population was approximately 6,500 and many residents were employed at the nearby Air Force base. In the early 1970s, the base was decommissioned, and the population began to decline over the next 50 years to its current figure – approximately 3,400. This left the city with an oversized water treatment facility that had the capacity to treat nearly 3.5 million gallons per day to a community that was now half its former size.
While the Glasgow plant was well operated and maintained, the operators had an increasing number of limitations with outdated treatment processes and aging equipment. To address these issues, the city elected to upgrade its water treatment plant. The project was completed in the spring of 2020, and Morrison-Maierle leveraged some unique approaches to retrofit and rehabilitate this 1960s-era facility.
Services and Highlights
-
Preliminary engineering report
-
Civil engineering
-
Construction phasing services
-
Planning
-
Bidding
-
Reclassification of plant
-
Unique approach to fitting new equipment into the existing footprint
-
3D modeling
-
Plans made to keep system running during construction and upgrades
Modern Technology and Cost-Effectiveness
The design included installing a new packaged steel tank clarifier system providing treatment specifically designed for the low turbidity source water from the Missouri River. The existing clarifier did not provide adequate pre-treatment for filtration due to its size and configuration, so the upgrade project included replacing the single clarifier with four contact adsorption clarifiers (CACs) housed in steel tanks—a proprietary process specifically used for low turbidity water. These units were pilot tested in 2015 to ensure performance.
The project also constructed new concrete filter basins appropriately sized for the current water demand (approximately 2.0 million gallons per day), modern filter underdrains, dual filter media (anthracite and silica sand), a pumped high-rate backwash system with supplemental air scour and filter to waste capability.
Since the CAC process is proprietary, Morrison-Maierle worked with the funding agencies and the city to find a workable solution for a cost-effective project. The design included negotiating a price with the supplier to procure the equipment and define the full scope of supply. A fair price was negotiated, and this price was written into the bidding documents.
The general contractor was responsible for contracting with the supplier and meeting all the terms and conditions. This approach reduced the risk for the city compared to pre-purchasing the CAC equipment. To balance the non-competitive CAC equipment, the filter equipment along with all other major equipment in the project were specified on performance, thus allowing competitive bidding between suppliers.
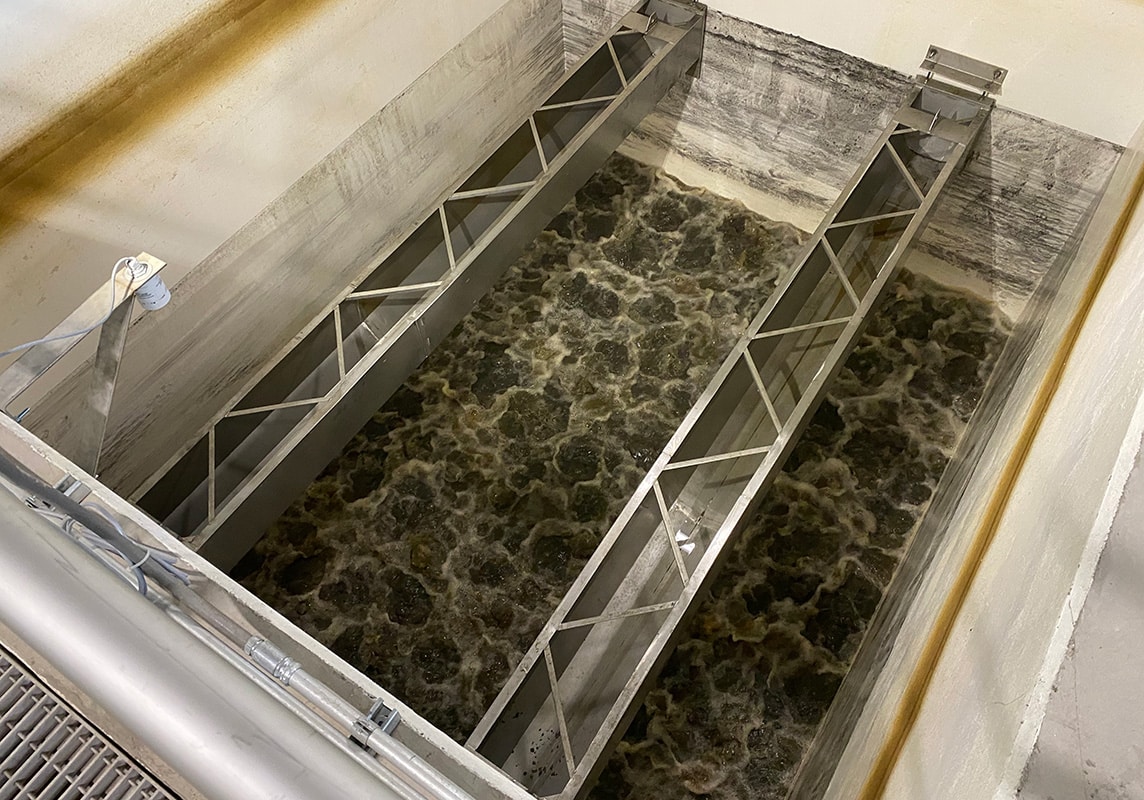
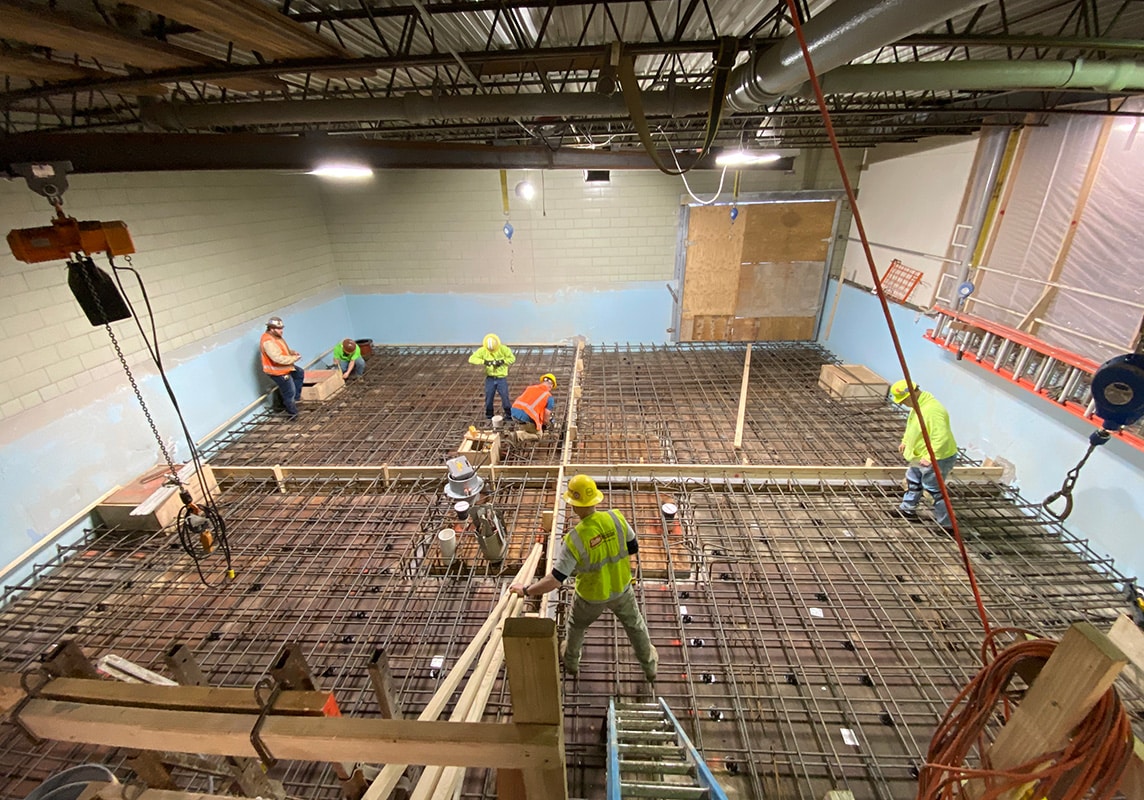
Detailed Phasing Plan
The city was interested in maintaining the existing building footprint due to site constraints and a potentially costly building expansion. In order to achieve this, the overall concept was to divide construction into Phase A and B, allowing the contractor access to only certain areas of the plant, while maintaining other areas so the city could effectively operate the plant and continue to produce water. Phase A involved the contractor demolishing the single clarifier and re-purposing the concrete basin to construct the new filters. The city then utilized only the existing filters to produce water during Phase A.
Once the new filters were commissioned and producing safe drinking water, the contractor moved to Phase B, demolishing the old filters and preparing this area for the new CAC system. The city had full access to utilize the new filters for water production. This approach created a seamless operation for the plant, and provided a detailed road map in the contract documents during the bidding process, while also allowing the contractor flexibility with certain unphased items to build a cost-effective project.
Due to the construction sequencing plan, the plant had to be operated without a clarifier in both Phase A and B. This required working with the Montana Department of Environmental Quality (DEQ) to reclassify the plant during construction. The water treatment plant was originally classified as a “conventional filtration” plant (chemical addition, clarification, and filtration) prior to construction. Phase A required demolition of the old clarifier basin, repurposed to construct the new filters. By eliminating the clarifier, the operational mode of the plant had to be converted to “direct filtration” (chemical addition and filtration only) during this time. Phase B involved demolition of the existing filters, while using the new filters for treatment, still operating in direct filtration mode. When the project was finished, the plant was reclassified back to a conventional filtration system with chemical addition, the new CACs, and new filters. Close coordination was required with city staff and Montana DEQ during the planning process, design and permitting, and construction to ensure operation was successful.
Related Projects
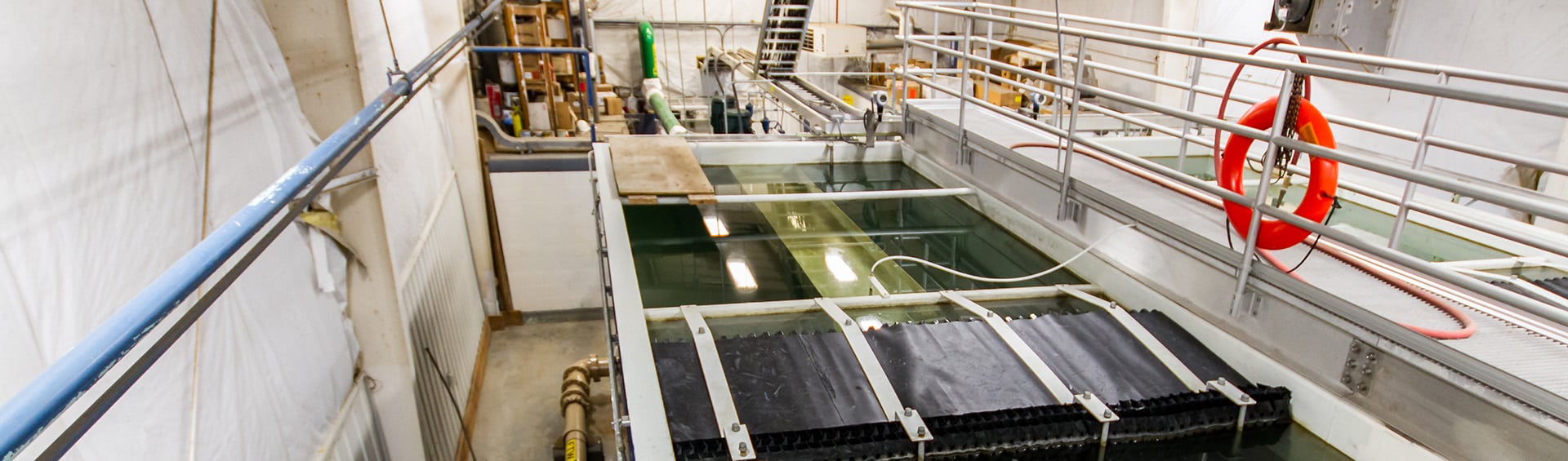
Chinook Water Treatment Plant Improvements
With front-end planning and engineering, the City of Chinook has an updated water treatment plant capable of processing the turbid, and sometimes volatile, Milk River conditions.
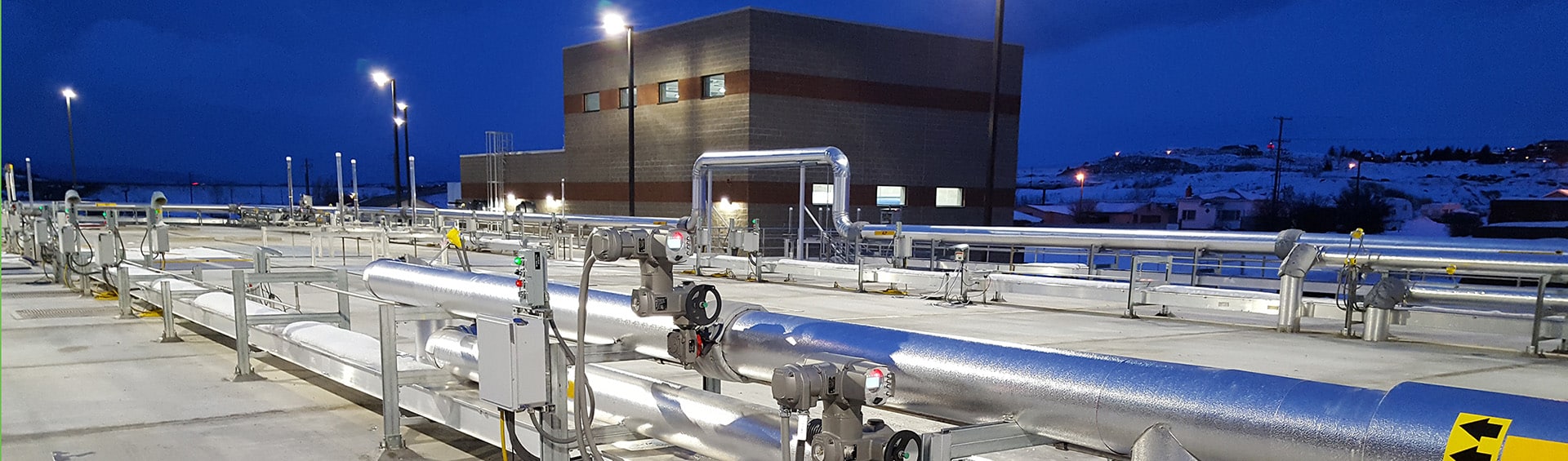
Butte-Silver Bow Wastewater Treatment Plant MBR Upgrades
Morrison-Maierle developed a cost-effective, efficient wastewater treatment plant in Butte using advanced technologies that minimized environmental impact on a nearby Superfund site.
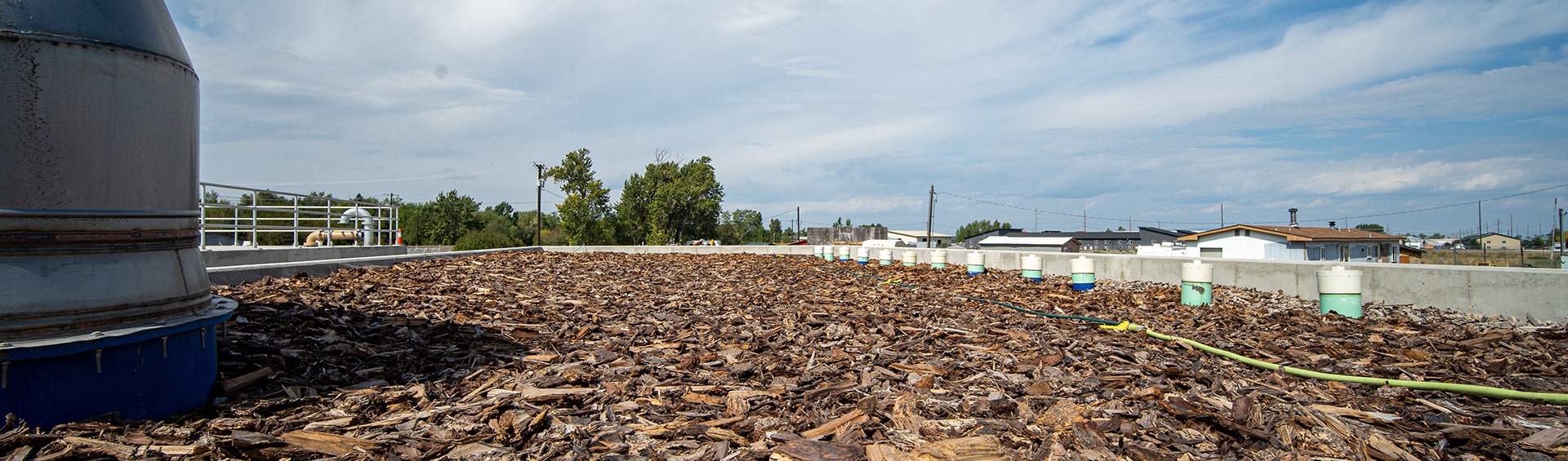
Four Corners Wastewater Treatment Plant
Four Corners Wastewater Treatment Plant