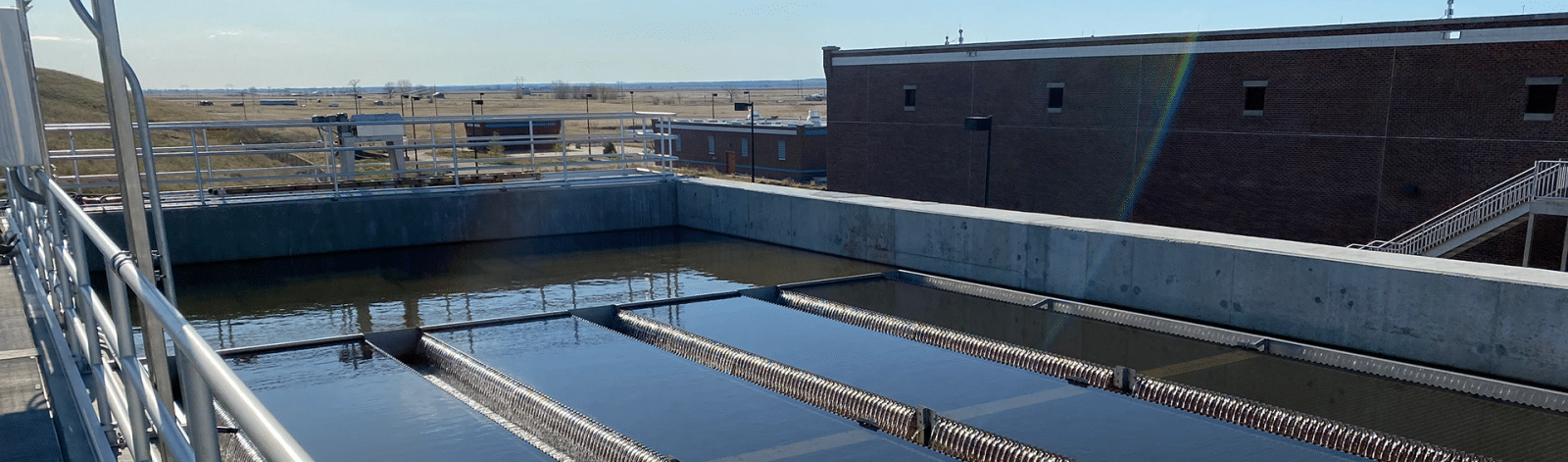
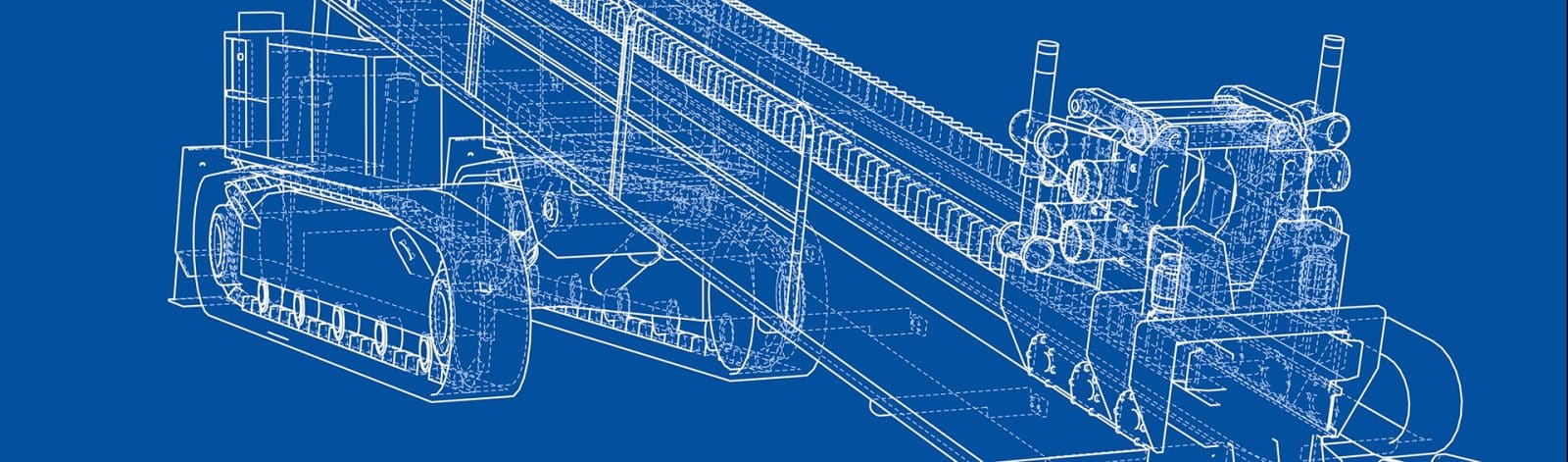
Why Trenchless Utility Installations Might Be Your Project’s Best Solution
By Mike Kynett, PE
Crossing existing roads, utilities, waterways, or other infrastructure with new utility installations can be challenging to permit. And in many cases, open-cut trenching may not be an option when crossing busy roadways.
However, once that process is complete, municipalities face another challenge: selecting the most cost-effective way to install the crossings—and one that also complies with your project’s permit.
A project’s schedule also may not fall into the timeframe required by the permit to perform an open-cut excavation across a waterway. Right-of-way or utility owners may not allow open-cut crossings at all and may require only a trenchless crossing option.
While it seems like there are many obstacles to installing new utilities, there are several installation methods available using trenchless techniques to cross existing infrastructure in a cost-effective manner. Here are three options to consider when evaluating the feasibility of a trenchless crossing. Each variation has its pros and cons along with its own unique requirements and considerations.
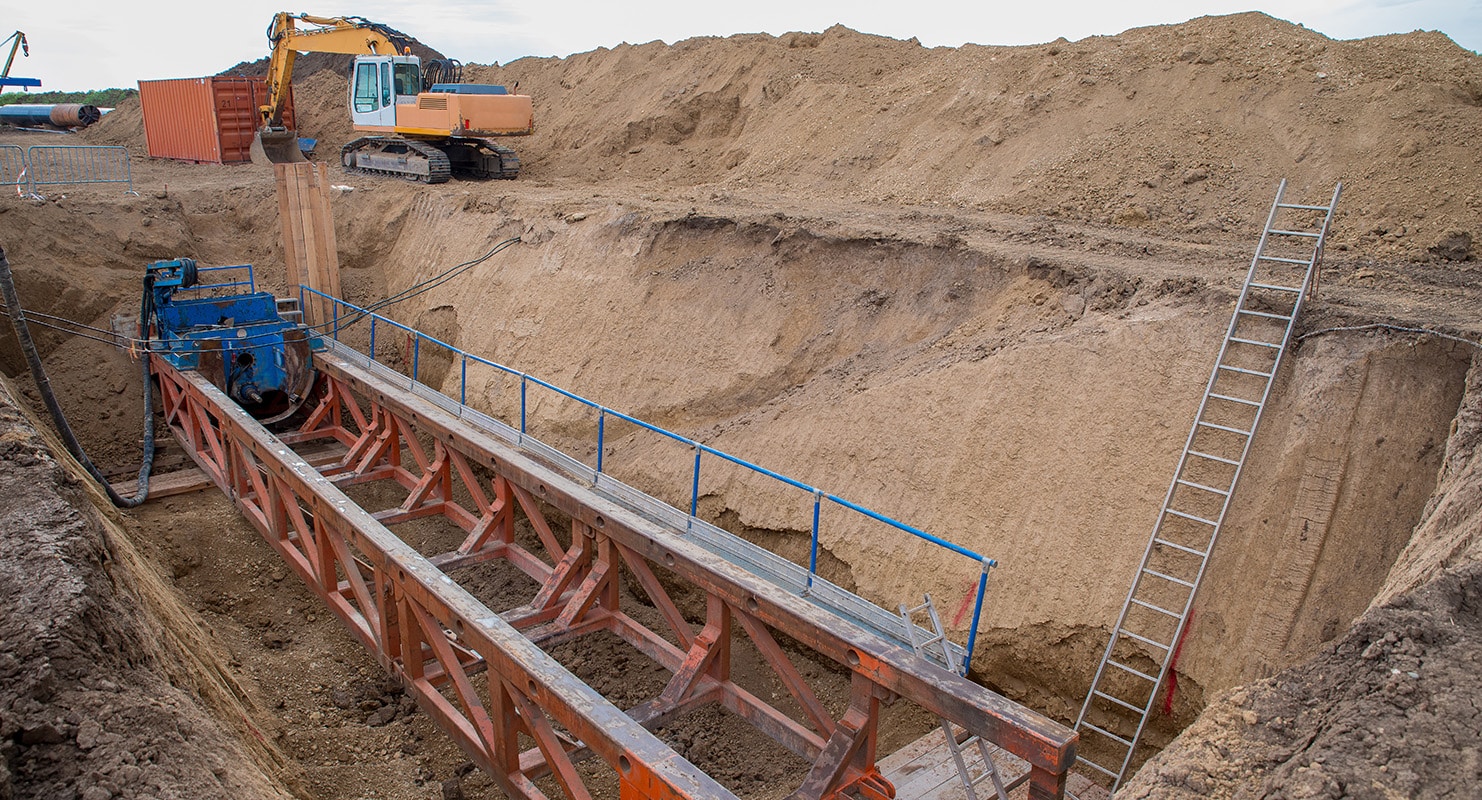
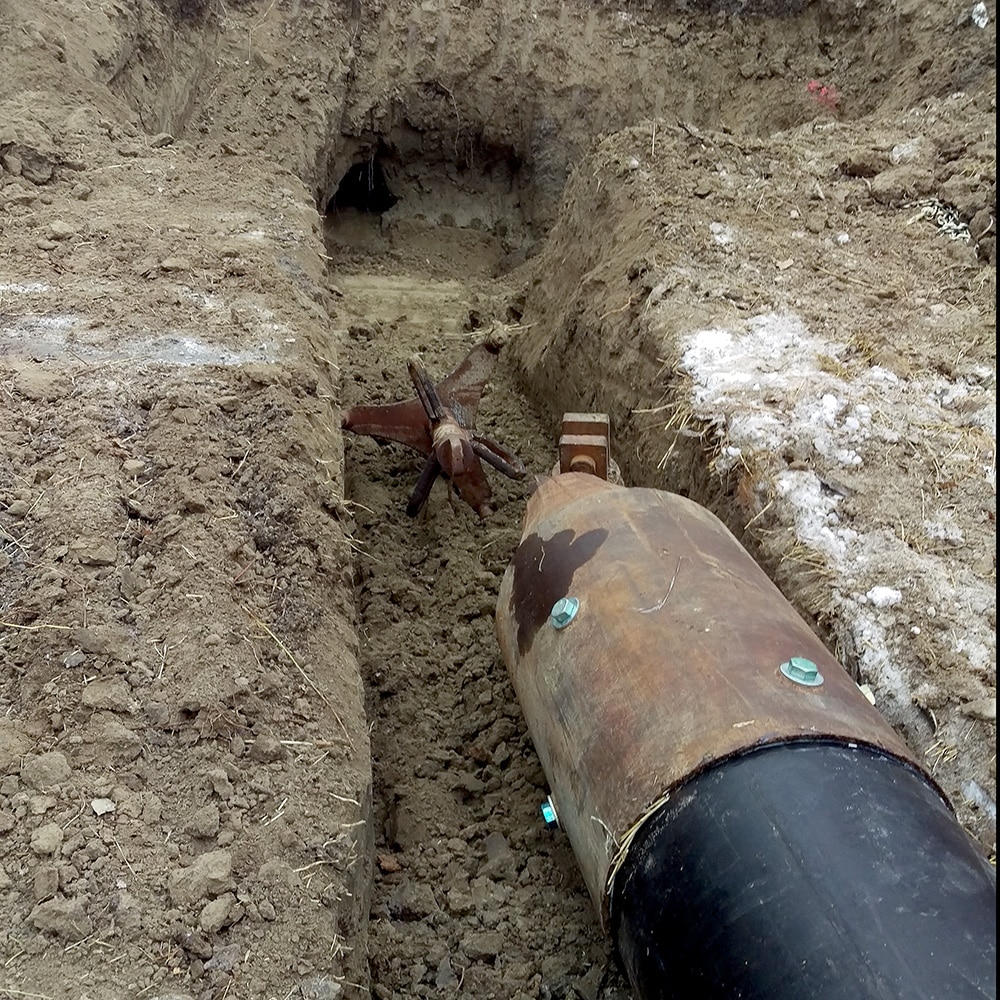
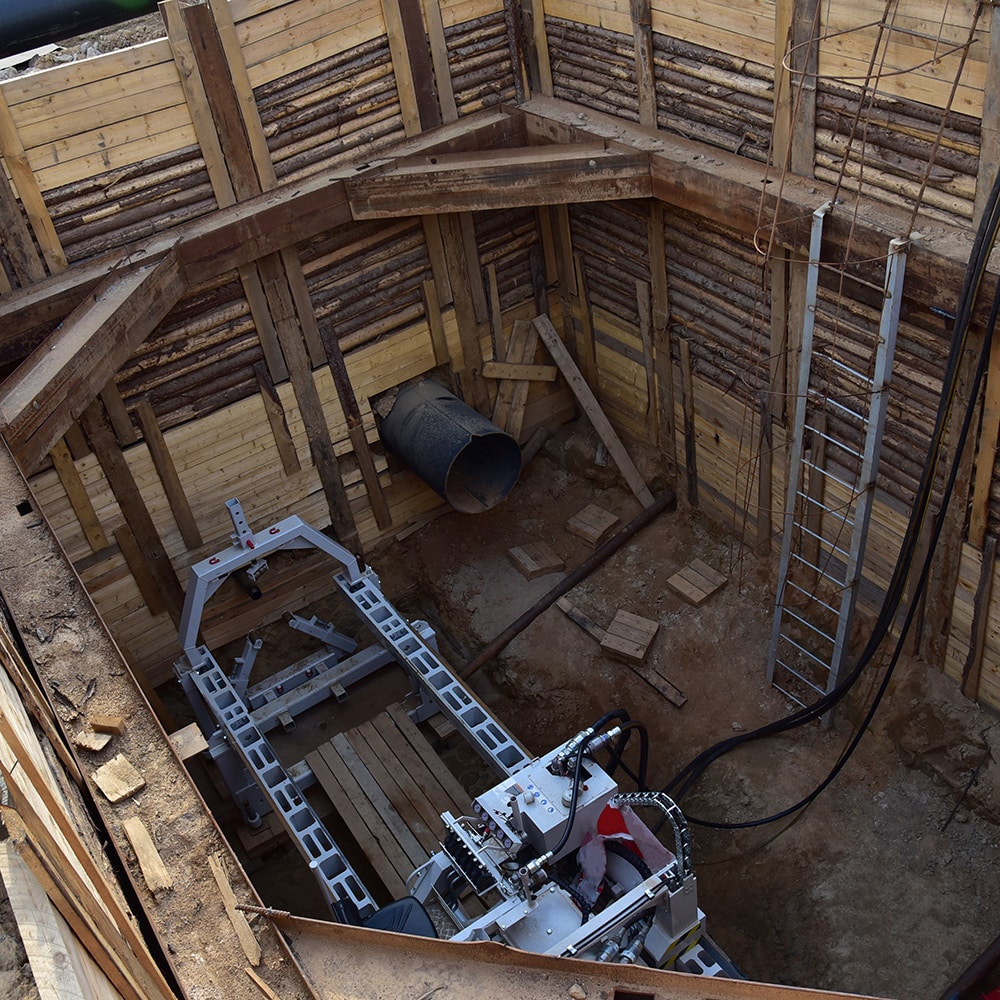
Directional Drilling
The directional drilling approach uses a flexible drill head to install a pipe at an angle and varying elevations. Drill heads of increasing size are used to bore out the crossing alignment. Then the carrier pipe can either be pulled directly into the prepared drilled path or insert a casing and the carrier installed into the casing. This method is common for going under bodies of waters such as rivers or creeks or under roadways.
One of the benefits of this method is that deep insertion and receiving pits do not have to be excavated as the pipe alignment can be drilled down from the ground surface to the desired elevation and then brought back up on the other side of the crossing.
The main drawback to this method is that soil conditions, such as gravely material or large rocks, can have an adverse effect on the drilling head and cause alignment errors. Geotechnical evaluations including bore log investigations should be completed beforehand to confirm that the soil conditions will allow directional drilling. These evaluations may require specialized equipment such as a barge if the crossing will be located under a waterway that can’t be accessed by the geotechnical drill rig.
Jack and Boring
Jack and Boring uses a straight-line boring technique and most often involves inserting a casing pipe first, then installing the actual carrier pipe inside the casing. The casing pipe is hydraulically jacked into place while a drill head with an auger is inserted through the casing pipe and is used to simultaneously create a crossing path in front of it. Drill tailings are removed at the insertion pit using the auger.
This method is effective for crossing under roadways or other elevated embankments where the depth of the pipe can be installed relatively close to the normal open-cut depth of the new utility installation.
Be aware that a permitting agency such as a highway department or railroad may require a casing pipe for the crossing. If so, this requirement can make jack and boring extremely cost-effective since the casing pipe is already placed as part of the installation method.
The drawback to this method is that the insertion and receiving pits need to be at the depth of the crossing elevation. Very deep crossings can be expensive due to the cost of excavation and shoring.
Is Pipe Bursting the Right Trenchless Method for Your Project?
Microtunneling
Microtunneling uses a small boring machine to drill a shaft, and the utility pipe is installed into the shaft. The boring machine is controlled remotely from the surface and is hydraulically pushed, similar to the jack and boring method. Insertion and receiving pits are excavated at both ends of the project, and the boring machinery is lowered to the desired crossing elevation. Drilling materials are also augured back to the receiving pit as in the jack and boring method.
A benefit of this method is that remote operation reduces safety concerns by eliminating the need for workers to operate machinery directly in deep excavations.
Microtunneling is often used for larger pipes and may not be cost-effective for smaller-diameter pipe installations. This method is also very specialized and is predominantly one of the most expensive techniques on a per-foot basis.
Learn How Trenchless Sewer Lines Can Save Time and Money