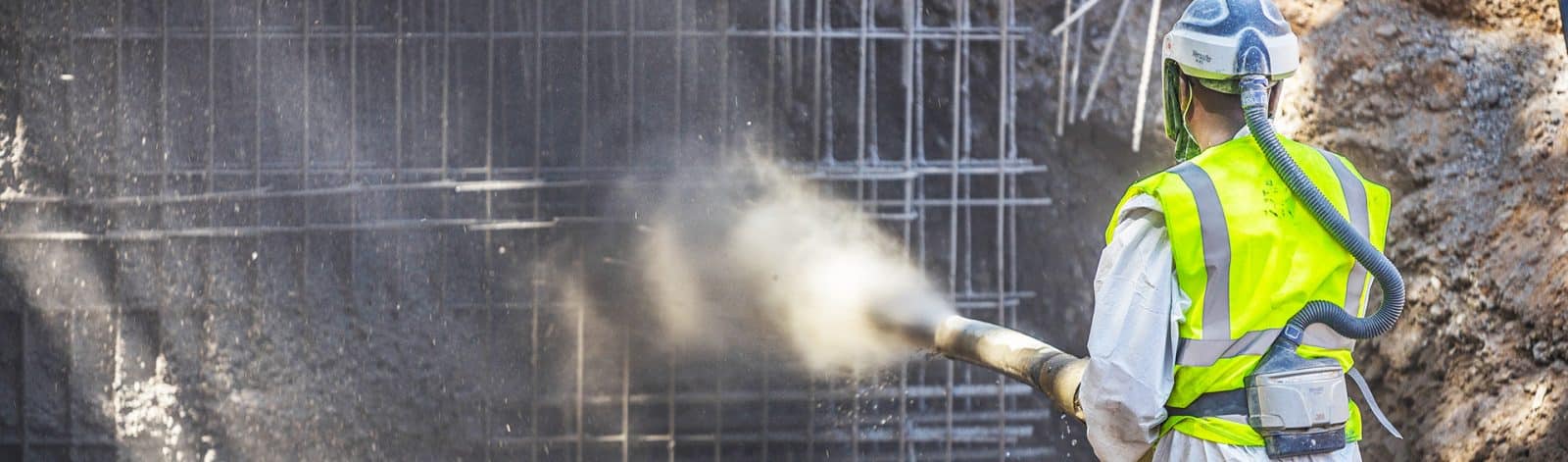
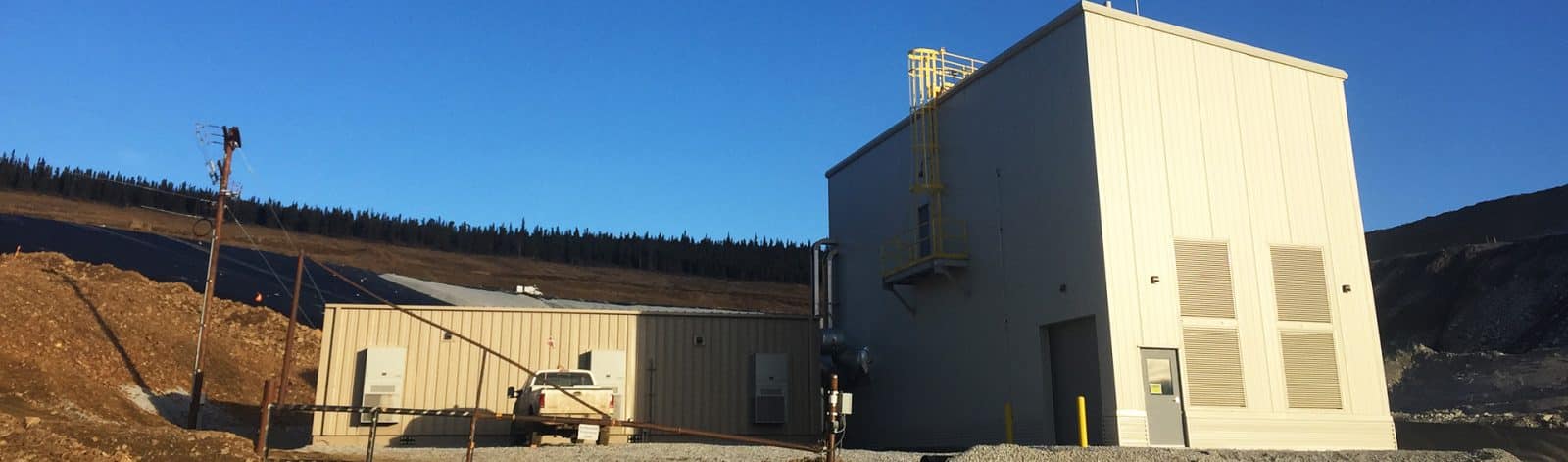
How Using a Pre-Manufactured Ehouse Can Save Your Project Time and Money
By Brian Literski, PE
Industrial mining projects use pre-manufactured Electrical Power Houses (Ehouses) for completing projects on schedule and within budget. I am often asked what makes these Ehouse units a better choice than a permanent electrical room, and when an Ehouse should be considered for projects. Before I answer these questions, let me first define an Ehouse.
Ready to ‘Plug and Play’
An Ehouse is a self-supported pre-engineered building that contains and houses most of the electrical equipment for an industrial project. Ehouses come in a variety of shapes and sizes to meet the project requirements and can contain anything from a single medium voltage Variable Frequency Drive (VFD), to a low-voltage motor control center (MCC) and control panel, or even the entire electrical and control distribution systems for an industrial process like a barren solution pump station. They come pre-connected and are essentially ready to “plug and play” into the field devices/equipment. Ehouses are also capable of being relocated or, once the life of the process is done, they can be decommissioned or repurposed much easier than a permanent building.
The interior electrical components are pre-wired and tested by the Ehouse manufacturer prior to shipment. The remainder of the work, once the Ehouse is delivered to the site, is to place it in its intended location and connect the external electrical connections for power, controls, and grounding.
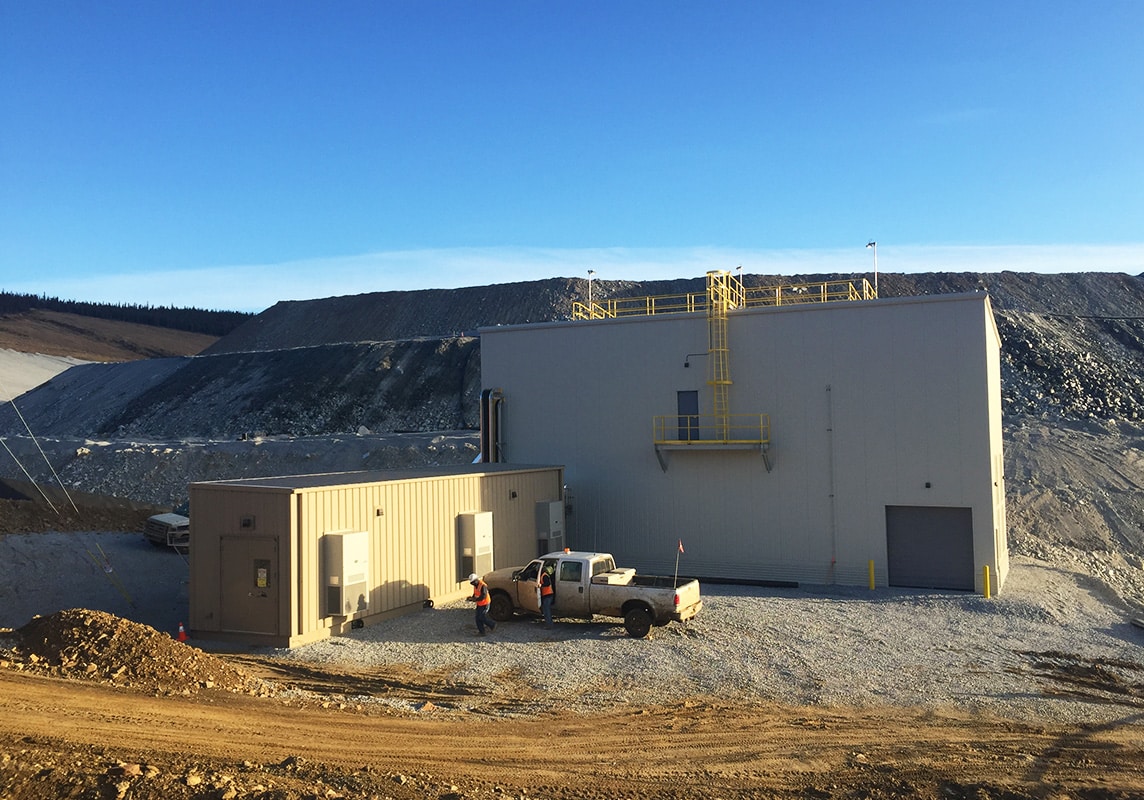
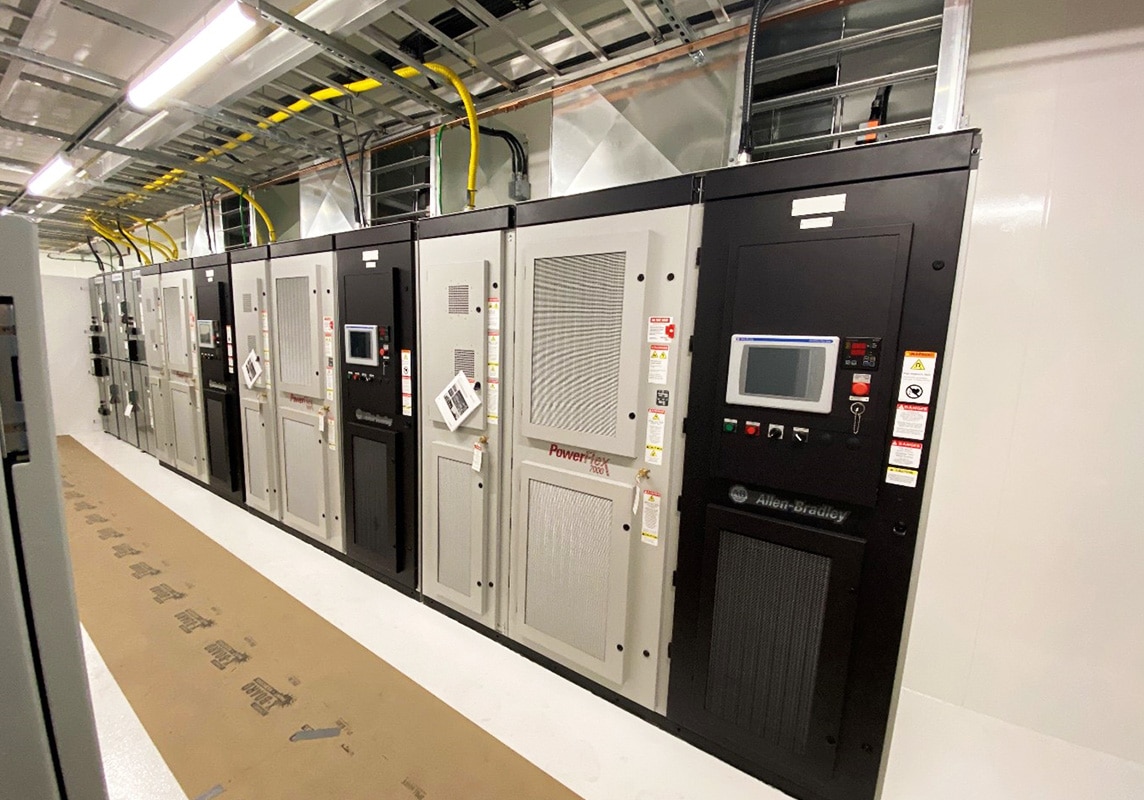
Tips for Success
In my experience, the electrical equipment used in industrial processes requires a longer lead time than standard electrical equipment for other building projects. For example, a new MCC or piece of medium voltage electrical equipment can have lead times as long as 12-20 weeks depending on the manufacturer and complexity of the equipment needed for the project. As a result, industrial project owners often purchase the large electrical equipment themselves to avoid contractor mark-ups and to get a jump on the long lead items associated with these types of orders.
However, if you decide to use an Ehouse, planning for long lead times, which include both manufacturing and shipping, can be avoided. Most reputable Ehouse manufacturers need 6-8 weeks to package the equipment and ship it to the site. This is an ideal situation because the owner can control the schedule by ordering the electrical equipment at the start of the project and establish the final timeline with the Ehouse manufacturer.
Another benefit is that the engineering time required for an Ehouse is reduced because the manufacturer takes on the design of the self-supported Ehouse structure. However, the layout of the interior remains the responsibility of the engineer, who adheres to working space and clearance requirements. The electrical layout—along with technical specifications detailing required construction methods—makes it easier to provide an Ehouse for a fast-paced project, again helping with constrained schedules.
Saving Time and Money
Ehouses can successfully help industrial clients meet their budgets by providing a pre-manufactured building with all the equipment pre-installed, wired, and tested prior to arriving on site. Both building layouts and proper building codes are addressed and finalized ahead of time which saves time and money. The cost savings come from having the equipment show up ready to be wired to the field devices such as power and/or controls.
Additionally, the client pays shop rates for the manufacturing and installation of this equipment instead of field rates and per diem which can be up to two times higher for more remote locations.
There are also fewer coordination issues between the construction disciplines (i.e. electrical, structural, and mechanical expertise) as the Ehouse manufacturer has the sole responsibility for sourcing, building, and providing quality control for the Ehouse. While material costs are roughly the same at the site or in the shop, we have found that labor is the biggest cost-saving factor in procuring an Ehouse. One thing to note is that depending on the size of the Ehouse, shipping can be quite expensive and should be a consideration in the final decision to design around an Ehouse.
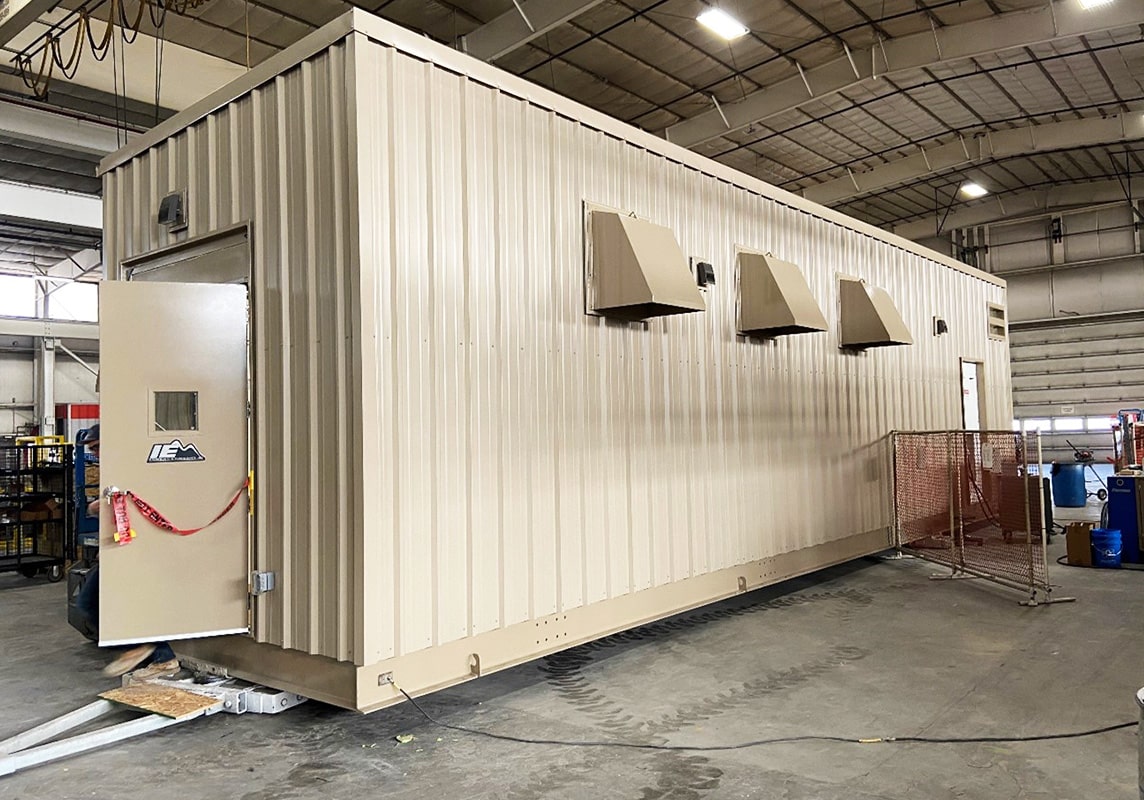
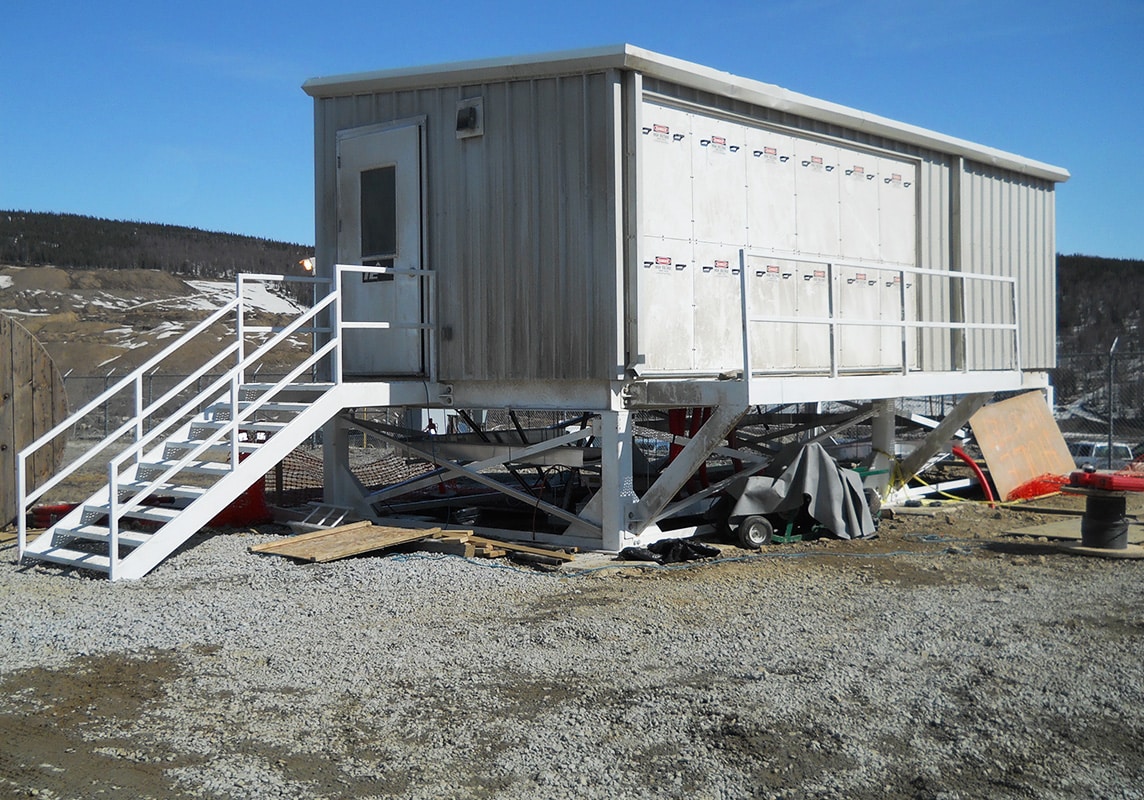
Remote Location Benefits
Ehouses really make sense when the process is at a remote location where there is no other structural building infrastructure or where there are multiple outdoor processes and installing a permanent building doesn’t make sense to the client. For example, we have deployed several Ehouses on mine sites where there are large pumping stations and no other building infrastructure being constructed.
It can still be an effective solution for remote processes located in a building as well by limiting the building contractor’s scope. Less work for the general contractor usually means the project can be delivered quicker to the owner.
Mining clients also like deploying Ehouses because it reduces the amount of structural concrete on site; reducing concrete on-site reduces the maintenance required by MSHA at these sites.
Ask Us
Morrison-Maierle has effectively deployed five major Ehouses in the last seven years on fast-paced mining projects and has found that they are particularly useful for large pump stations where there is no other vertical building infrastructure.
If you have questions, need more information, or want to know if an Ehouse is right for your next project, please reach out. We’re always happy to help and answer your questions.