
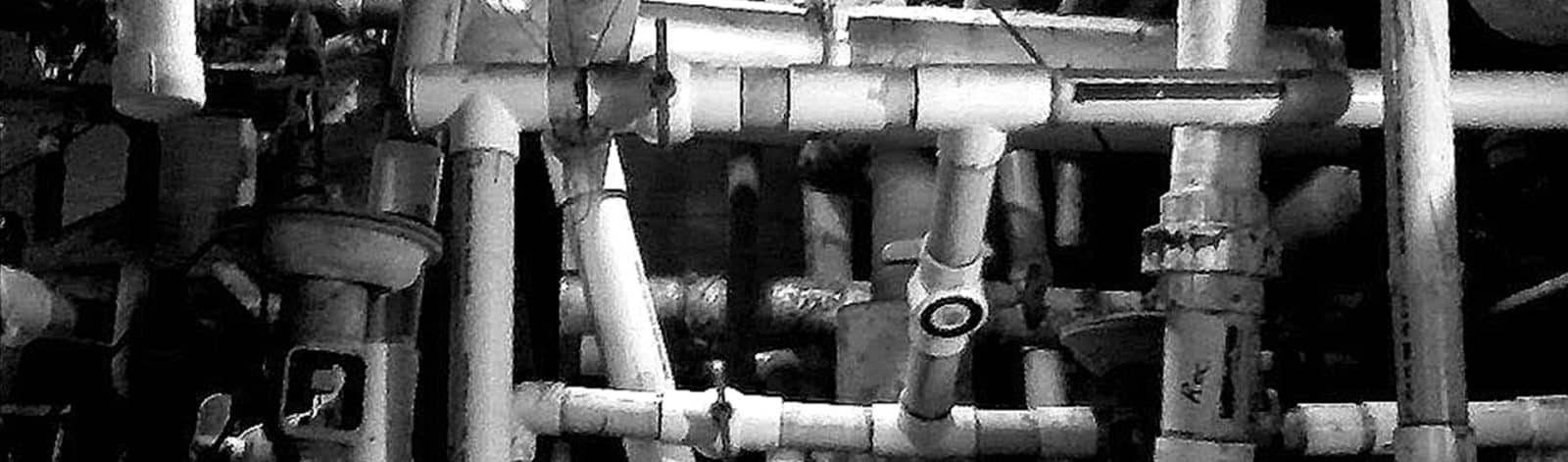
Risks and Consequences of Deferred Maintenance
By Rika Lashley, PE
Countless communities in the U.S. are faced with deferred maintenance issues for their water and sewer infrastructure—usually due to budget constraints. Piping that was placed in the ground half a century or longer ago is beginning to fail. Or worse, deposits within this old pipe have the potential for contaminating the water along its route and can run into people’s taps. Equipment installed to treat the community’s wastewater and keep the receiving streams or aquifers safe is being held together by resourceful operators, even though it should have been replaced a decade ago.
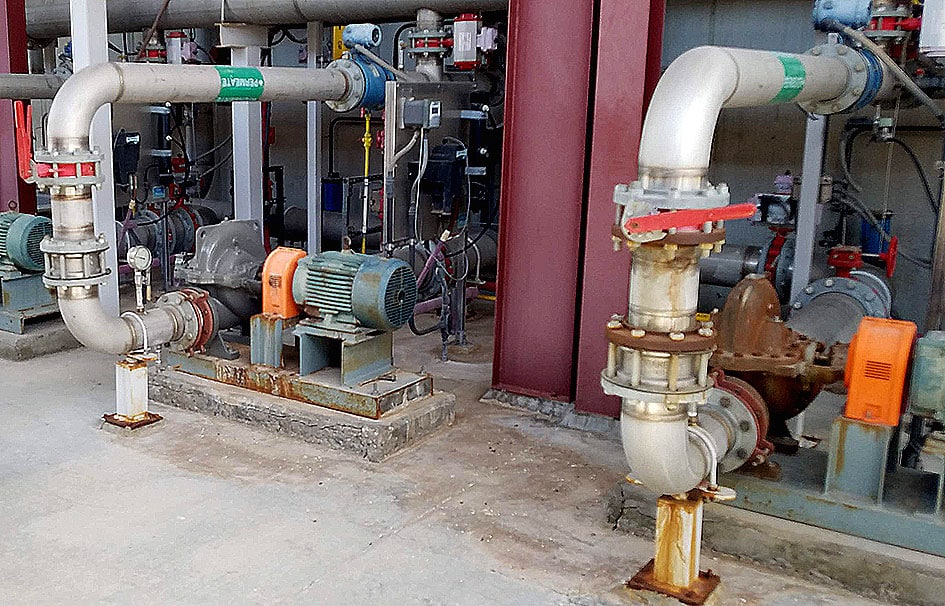
Does the worry over when the next piece of critical equipment may fail keep you up at night? Does the argument of lack of budget begin to sound hollow when the “what-if” scenarios in your mind keep getting increasingly dire? Or are you one of the decision makers saddled with the responsibility of deciding to spend money that doesn’t appear to exist?
Here are some things to consider when working through costs (direct and indirect) and budgets that may help you put the real costs and savings into perspective with a proactive deferred maintenance plan.
Costs and Risks of Deferred Maintenance
There are three main risks and associated costs to consider when analyzing the potential of equipment failure, and how you might use these to develop a deferred maintenance plan.
- Cost of replacement now versus replacement in five years – The cheapest time to replace is now because over time, equipment and services will be more expensive. If you have determined that a piece of equipment needs to be replaced, it is in your community’s financial interest to make the replacement sooner rather than later.
- Cost of emergency repairs/responses versus planning for replacement – Planning for replacement allows you to select the best time; one that minimizes impacts on the rest of the operations rather than having to respond when your equipment fails. If there is no plan for replacement, other processes can be impacted that can drive up efforts and costs needed to fix the situation. Planning also allows you to choose a better piece of equipment that may save you energy, consumables, or labor in the long run. Emergency replacements tend to replace like-for-like solutions and don’t allow enough time to consider long-term planning and explore other more efficient solutions.
- Environmental risks and considerations – If an equipment failure causes a spill of some kind, there may be environmental damage, which can add time, effort, and unexpected costs to mitigate.
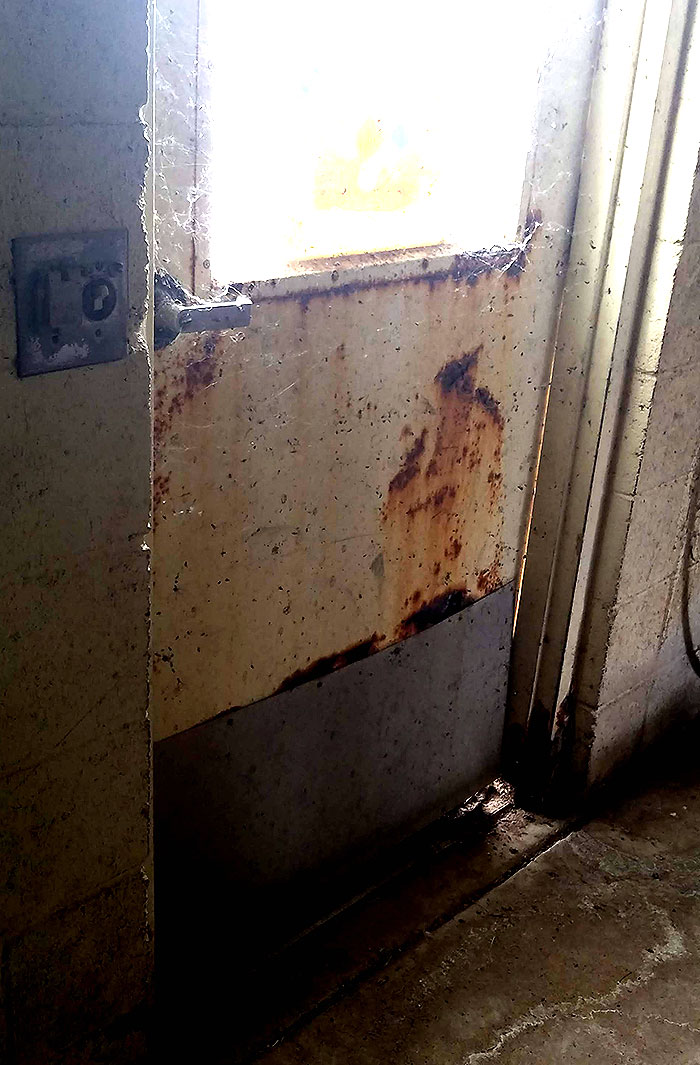
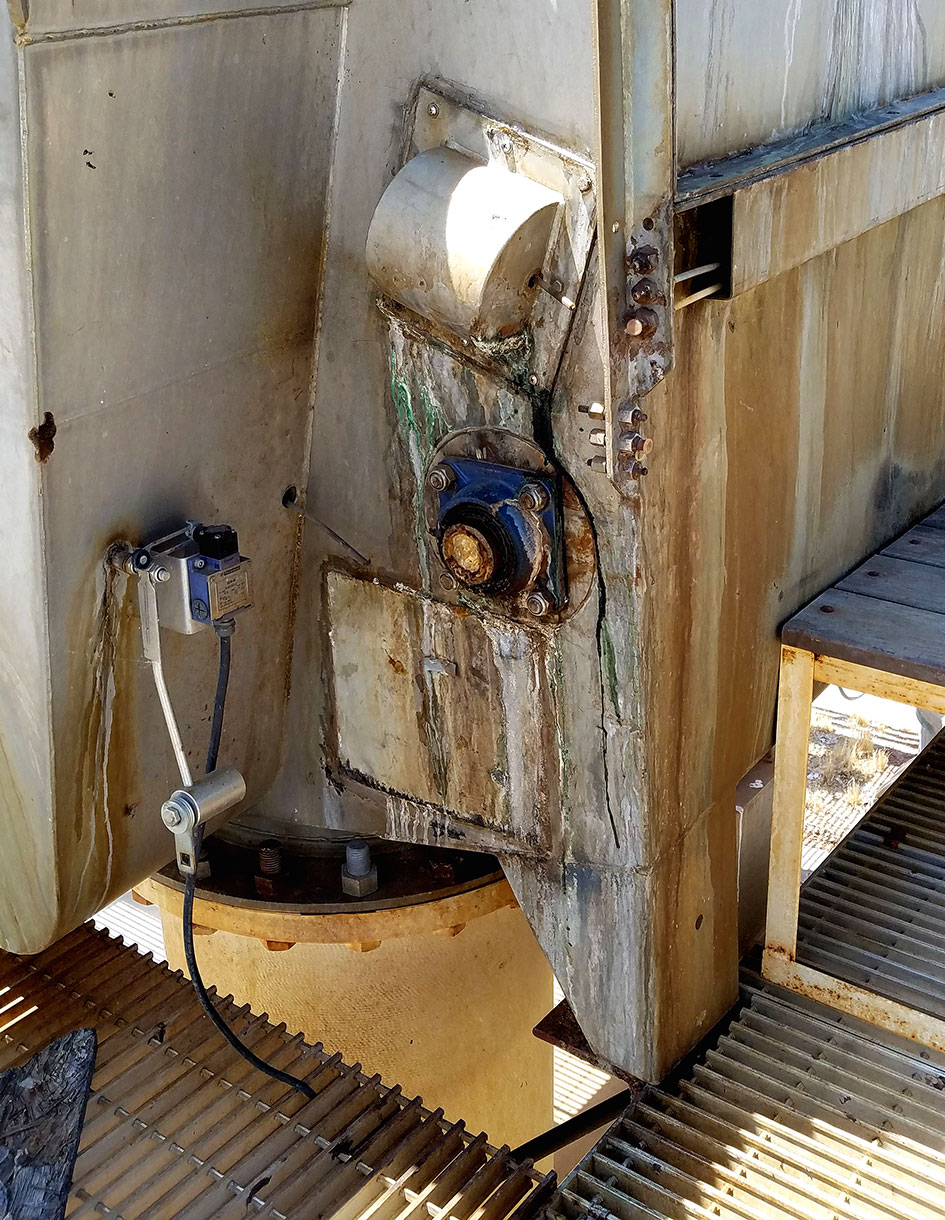
Environmental Health and Safety Impacts
In addition to quantifiable costs associated with deferred maintenance, there can be other indirect costs regarding the health and safety of the public and the environment. While the following may not directly translate into dollar amounts at your facility, they do carry risks and can incur costs in round-about ways:
- Staff safety risks – Your staff works around the clock to keep your community supplied with safe drinking water and treat its wastewater. When they respond to an equipment failure, they can be exposed to raw sewage, chemicals, and unsafe conditions like slippery surfaces. They may also have to enter confined spaces or endure extreme outdoor temperatures. These conditions may lead to workplace injuries, exorbitant medical costs, and missed work. Your operators deserve safe working conditions and will perform better in an environment that considers their health and safety.
- Public health risks and considerations – Failure of critical systems can also put the public’s health at risk, whether improperly treated drinking water or a release of untreated wastewater into a stream.
- Loss of public trust – If the equipment failure leads to service interruptions to the public or environmental damages, the public may lose trust in your utility and the services you provide. It will take time, an overabundance of good communication, and years of service without trouble to regain this trust. This loss of public trust may also lead to a high volume of angry calls to your staff, excessive and unnecessary scrutiny of future operations and decisions, staff turnover, and even lawsuits. While it is difficult to estimate a dollar amount for a loss of public trust, a real risk can be avoided with a solid plan in place.
So how do you begin to tackle this issue? The starting point must be an assessment of your facilities that evaluates all facility components’ condition, performance, and capacity. The results of the assessment will be used to identify needs and plan for repair, replacement, or upgrades in a manner that makes the most efficient use of every dollar spent. This assessment will start the process of waking from the deferred maintenance nightmare—and begin curing those sleepless nights.
Maintenance Planning Resources
The water-wastewater industry is not the only one faced with budget shortfalls and the need for careful planning to avoid emergencies. If you are interested in what other industries have to say about the costs of deferred maintenance, check out these links:
- “The Real Cost of Deferred Maintenance,” is an article from the perspective of the healthcare industry.
- “Gambling with Deferred Maintenance: Today’s Solution, Tomorrow’s Problem” is an article by AAF Flanders written from the point of view of a facility manager of building housing offices, schools, hospitals, etc.
You may want to check out Stephanie Seymanski’s blog on Preliminary Engineering Reports, which provides a tool for assessment and planning, as well as procuring funding for projects. I will also follow up on this blog with a second installment to look at some aspects of facility assessment and planning. Stay tuned.
Learn how to end your deferred maintenance nightmares