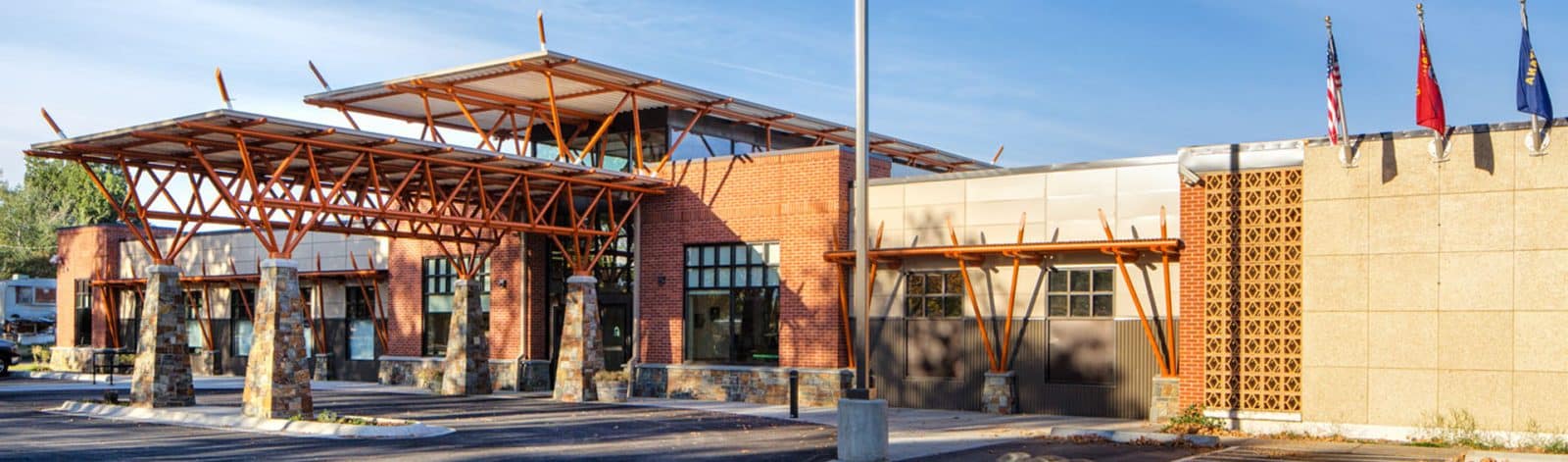
St. Ignatius Community Health Clinic
Expanding Tribal Health Services
The Confederated Salish and Kootenai Tribes (CSKT) of the Flathead Reservation needed medical facilities for its people in the Mission Valley. Their original 1960s-era facility had a clinic, mental health services, and areas for X-ray, audiology, diabetes education, and physical therapy. The tribe decided to build the St. Ignatius Community Health Clinic, which has expanded its services so locals can receive care in their community and don’t have to drive to nearby Missoula for basic medical care. As a result of this project, the clinic has also been able to hire 150 more people in medical professions on the reservation and start programs and services they couldn’t house before this facility was built.
Initially, the project was divided into several phases: Hazardous materials cleanup before construction, preparation and demolishing a section of the existing structure, constructing a new building, and remodeling of the existing structure.
During the last phase, the owner secured more funding that nearly doubled the money they had to work with. They put it into the project, which posed many new design challenges for the team but provided the owner with a better building than expected.
Services & Highlights
-
Mechanical engineering
-
Electrical engineering
-
Plumbing design
-
Fire protection engineering
-
Civil engineering
-
Survey
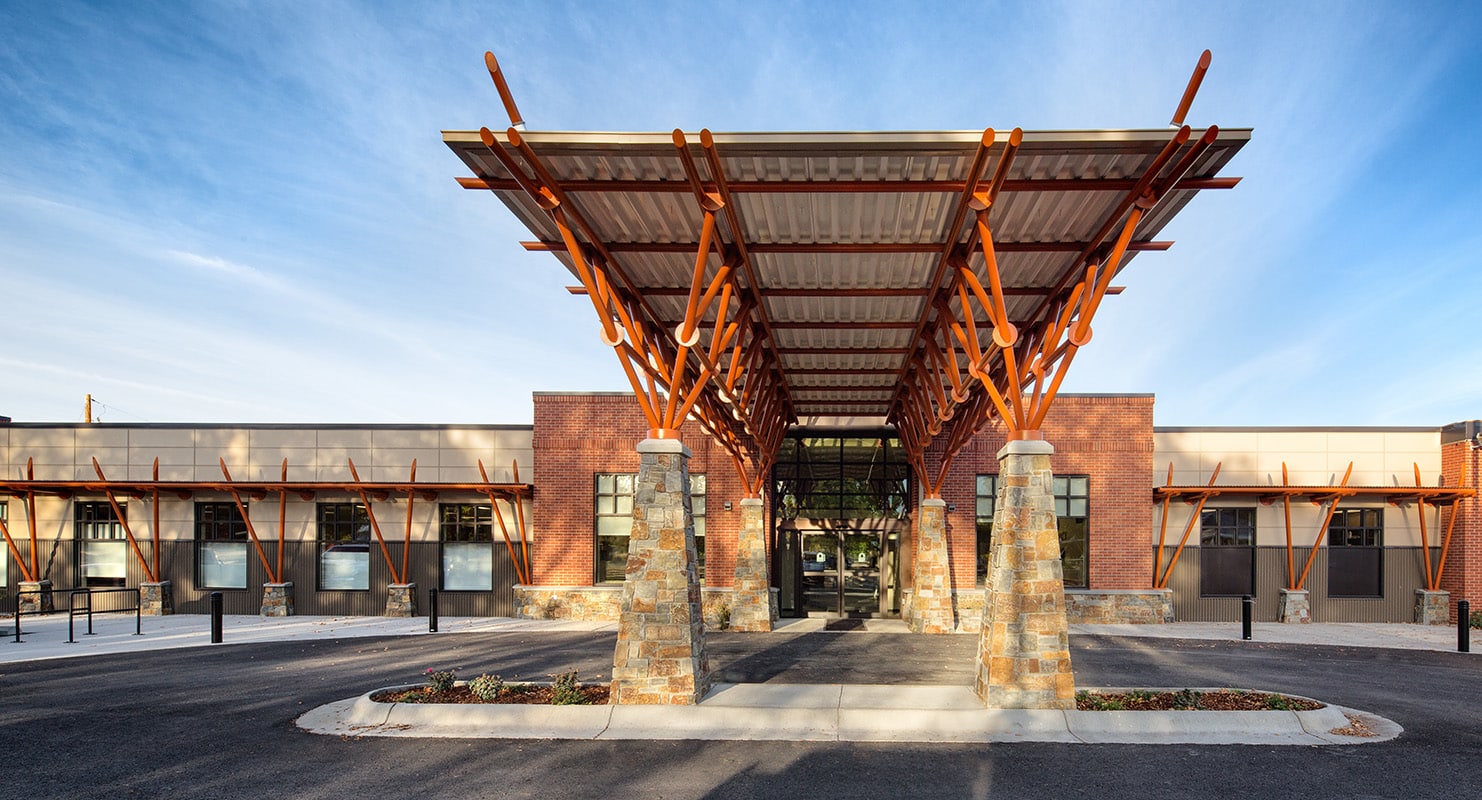
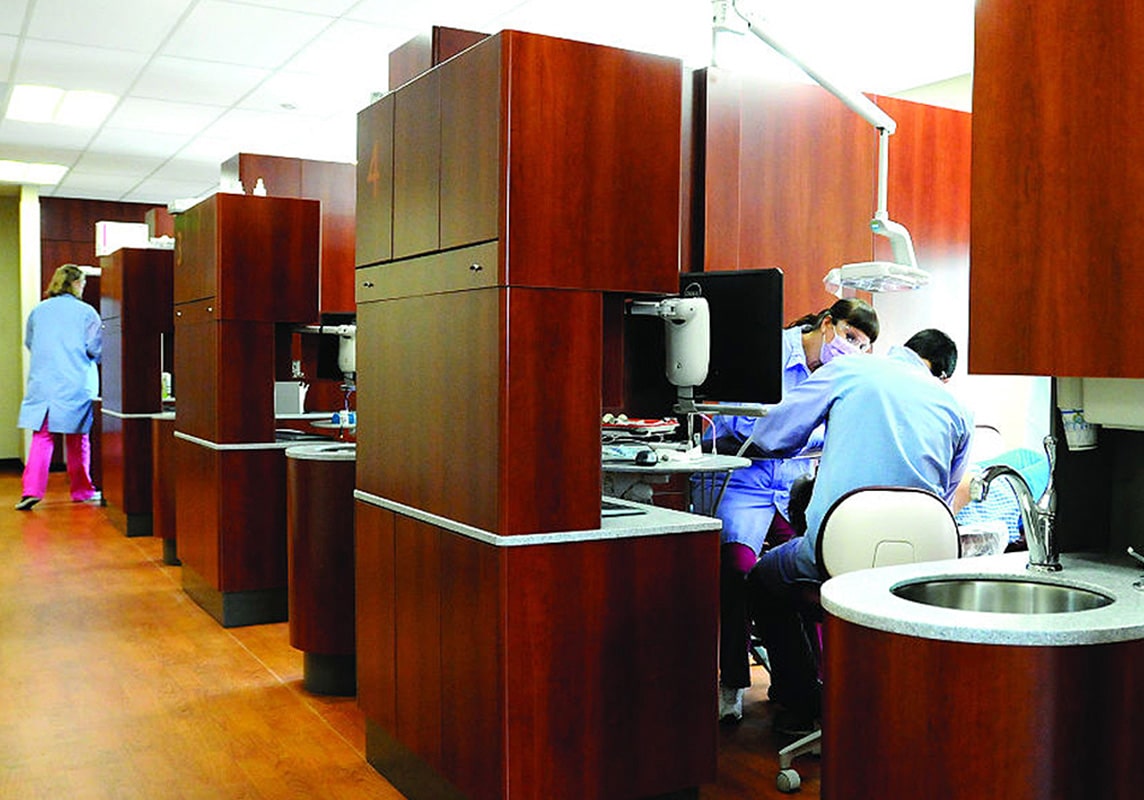
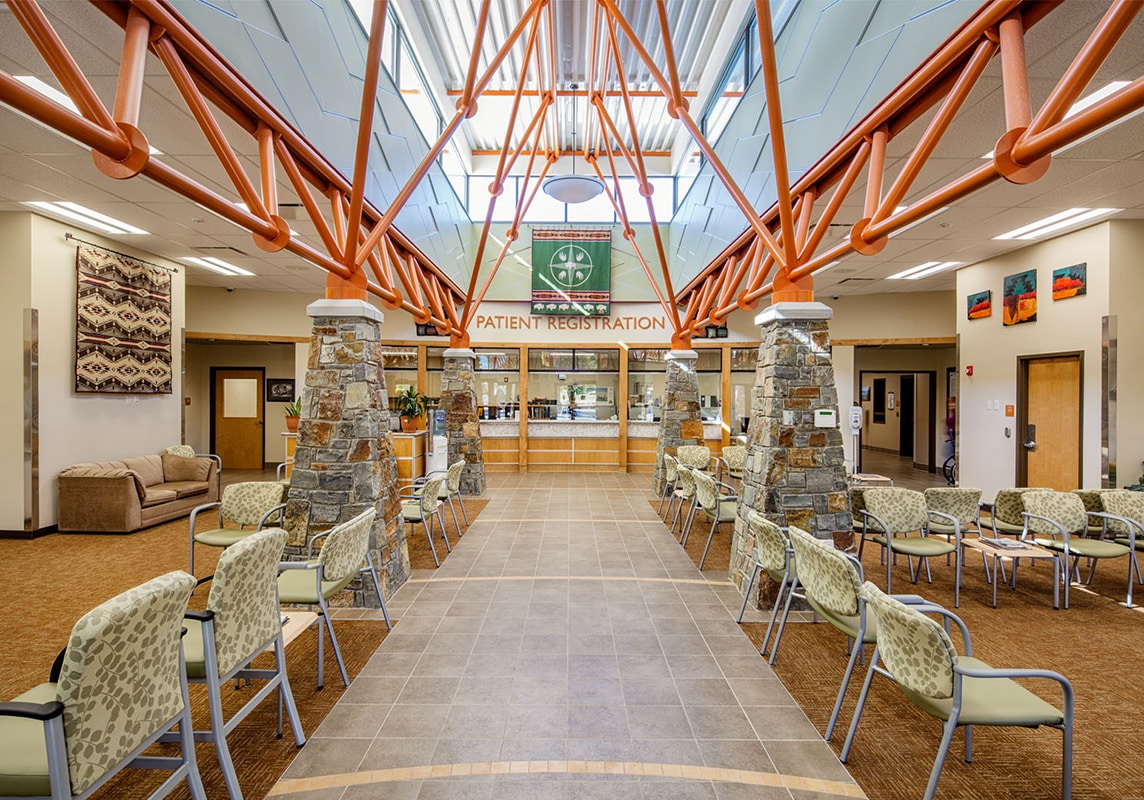
Tight Spaces and Tight Budgets
Due to budget constraints, many design decisions were made based on the very few affordable options available. Originally, the existing building was served by a 30,000-gallon propane tank 100 yards away, and the owner’s preference was to eliminate the propane. Morrison-Maierle did an energy study to determine what type of system and what energy source would be most effective. Since there is no natural gas service in the area the only options were propane and electricity.
Because of the extremely low electric rate (due to Kerr damn and their utility benefit to the community), Mission Valley users have extremely low and stable rates compared to the rest of the state. Propane, on the other hand, was very expensive and unstable prices. The new design removed all propane in the building with the exception of a generator to back up critical electrical loads for the clinic that would protect its equipment.
The new portion of the building was easier because the team created a building that was of standard height and up to code. However, the existing building’s low ceilings provided a unique challenge. Morrison-Maierle’s team came up with a solution to put Remote Terminal Units (RTU) on the roof, ductwork through new chases to the crawlspace, and utilized the large crawlspace that existed under most of the existing building that would serve the clinic space below.
The team also used air source heat pumps and electric backup in the rooftop unit. These units incorporate variable air volume and reheat with electricity. As a result, there is no need for boilers and chillers as they have packaged DX Cooling with digital scroll compressors and SCR electric heat to maintain a constant discharge air temperature. Both the remodeled and the new portions of the building are highly efficient in terms of heating and cooling.
Designed to Stay Open During Construction
Finally, because this project was done in phases, Morrison-Maierle had to make sure certain areas of the clinic were operational because it did not have another temporary location to move into during construction. The design team decided that in order to keep the facility operational, the new RTU was one of the first things installed on the new portion of the facility and it was used on the existing portion of the building during the reconstruction of the existing facility.
Related Projects
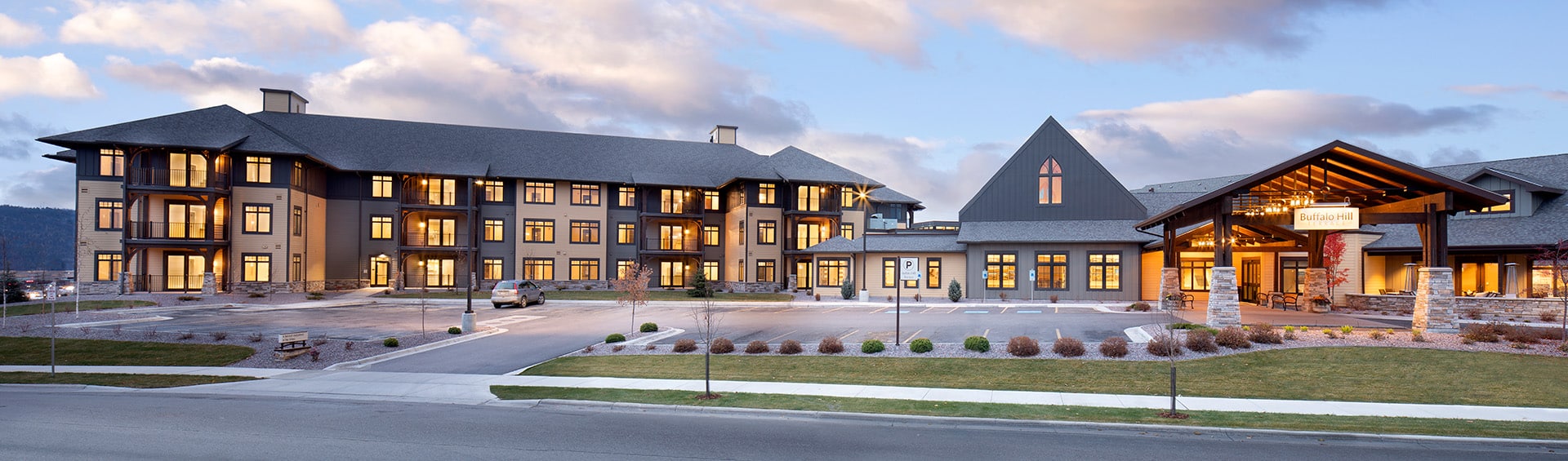
Immanuel Lutheran Communities
With core values of compassion, excellence, respect, integrity, and stewardship, Immanuel Lutheran Communities (ILC) provides care for the aging through their Immanuel Lutheran Home facility.
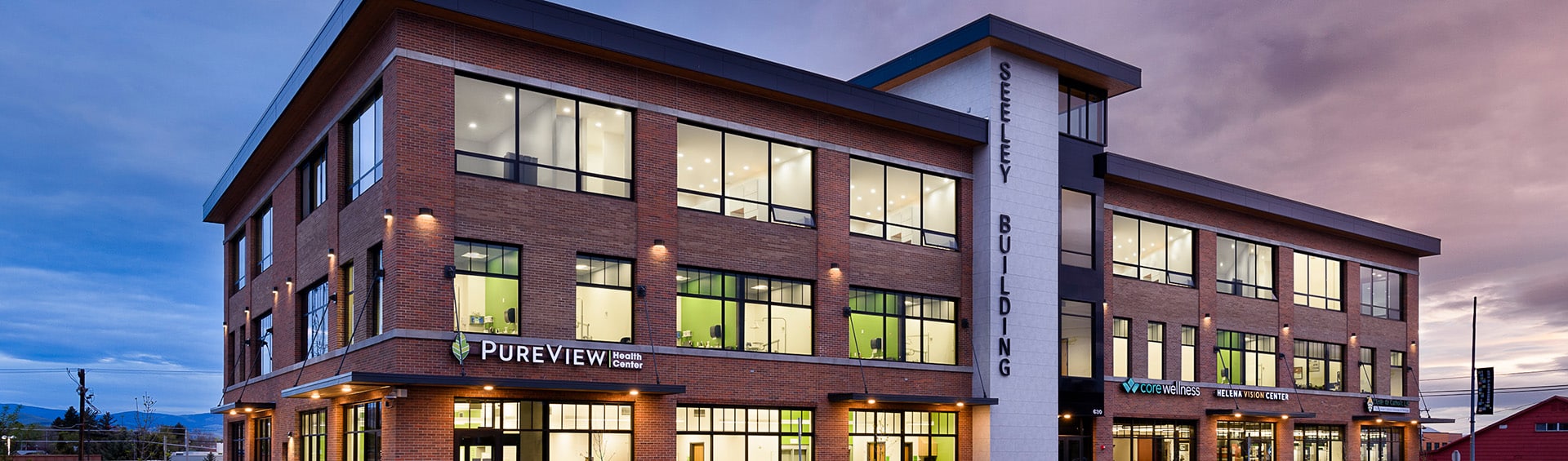