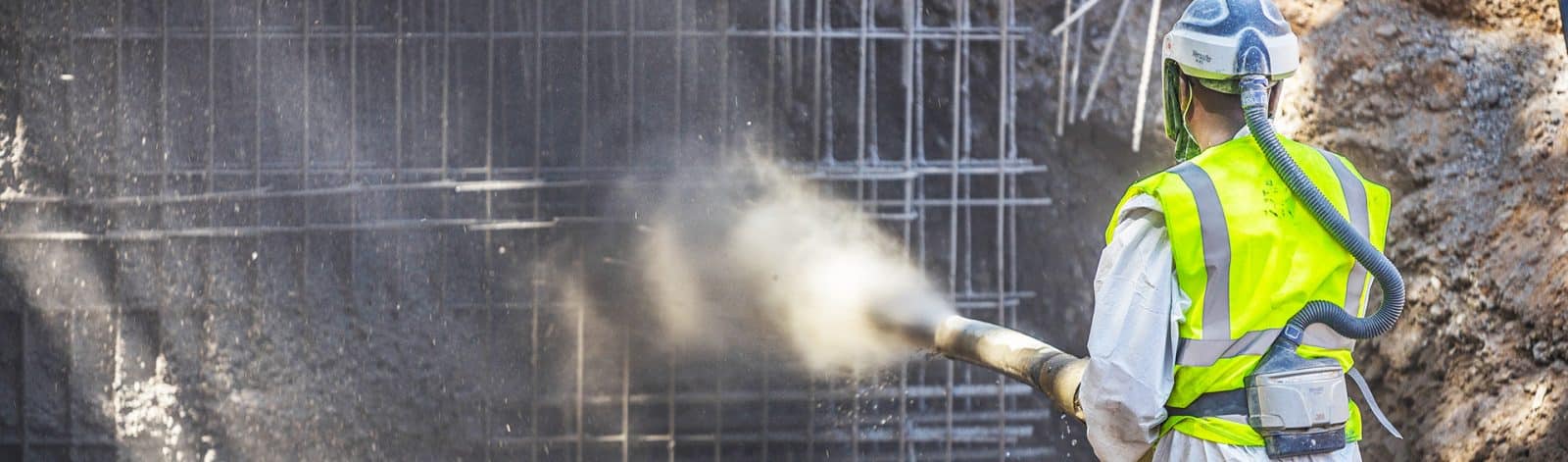
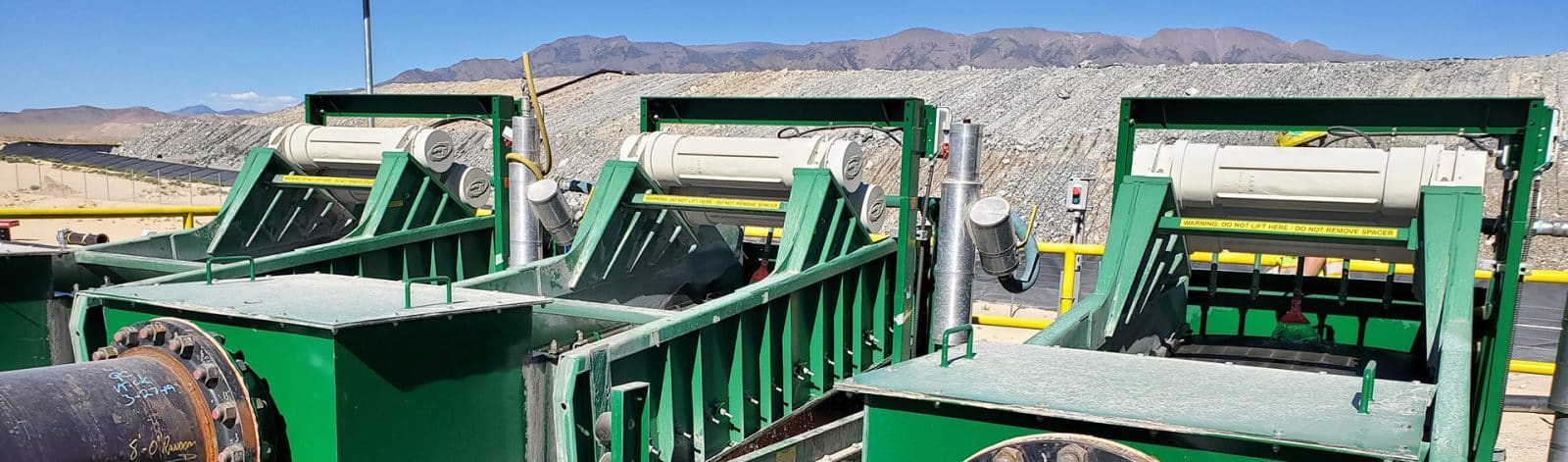
What You Need to Know About Vertical Carbon-in-Column Plants
By Deborah Johnston, PE
Are you considering adding solution handling capacity to your heap leach operations? If your reasons for wanting to add a carbon-in-column plant are for primary gold recovery or as a scavenger circuit to pull ounces from re-circulation, your next question might be, “Would a vertical design make more sense?”
Cascading columns (also known as gravity) Carbon-in-Column (CIC) Plants are one of the most common and proven engineering solutions for processing solution from heap leach pads. They consist of large-diameter columns that are filled with activated carbon. The pregnant solution flows through the carbon columns, generally in a step-down arrangement so that the overflow from the highest elevation column will flow to the next column. The gold absorbs onto the surface of the carbon. The loaded carbon is periodically removed from the columns and sent for stripping.
With at least four Vertical Carbon-in-Carbon (VCIC) Plants commissioned in the past two years in Nevada alone, a vertical plant design is something you might want to consider. The advantages of the vertical column approach include the following:
- Smaller footprint.
- Reduced amount of valving between stages.
- Reduced fabrication costs.
- Between 20 and 30 percent lower installation costs.
If your operation is constrained by any of the issues above, “going vertical” might be the way to go.
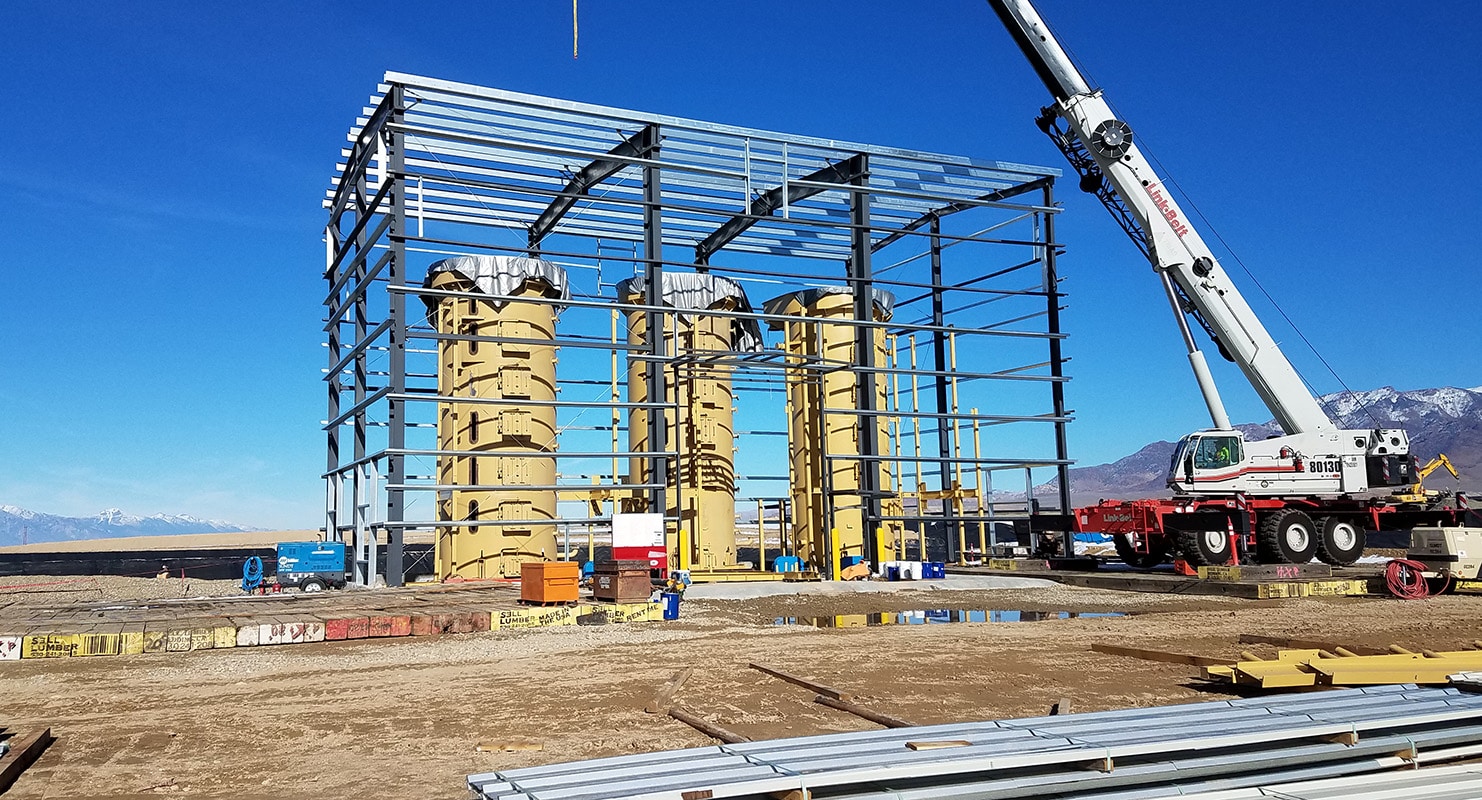
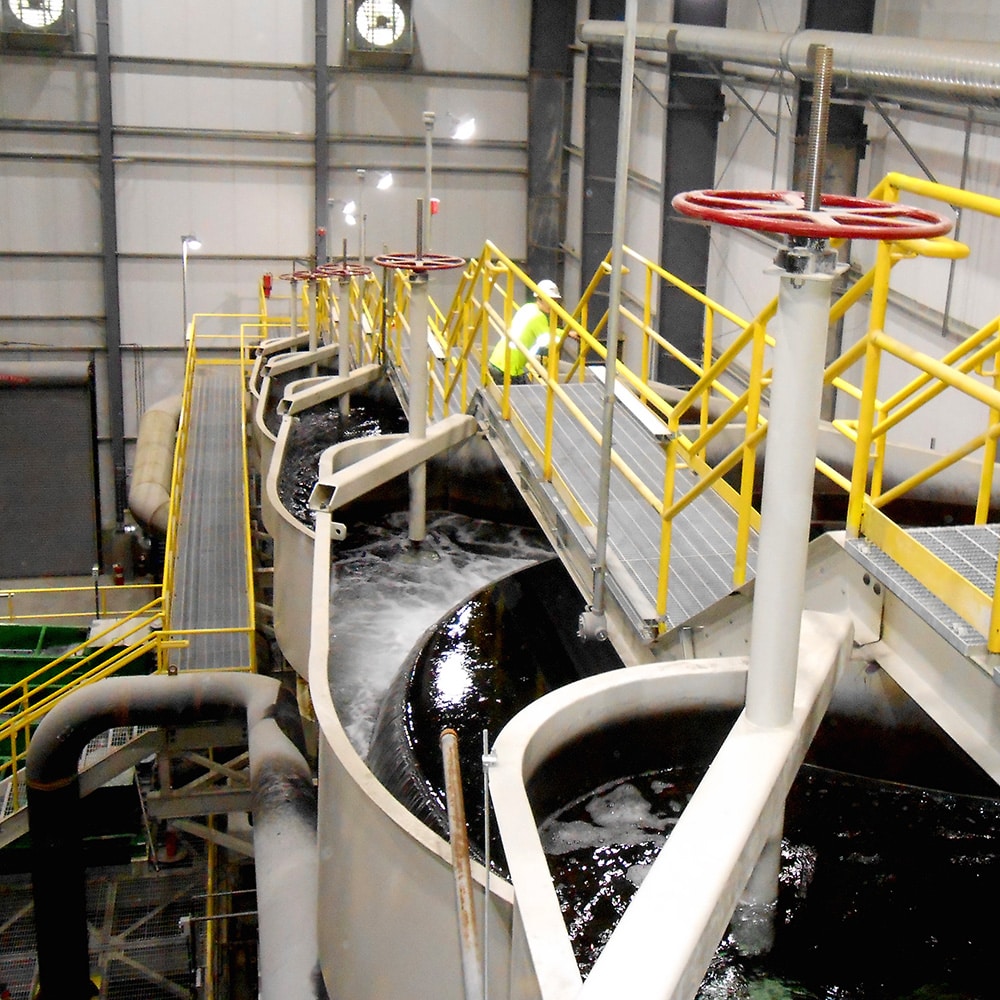
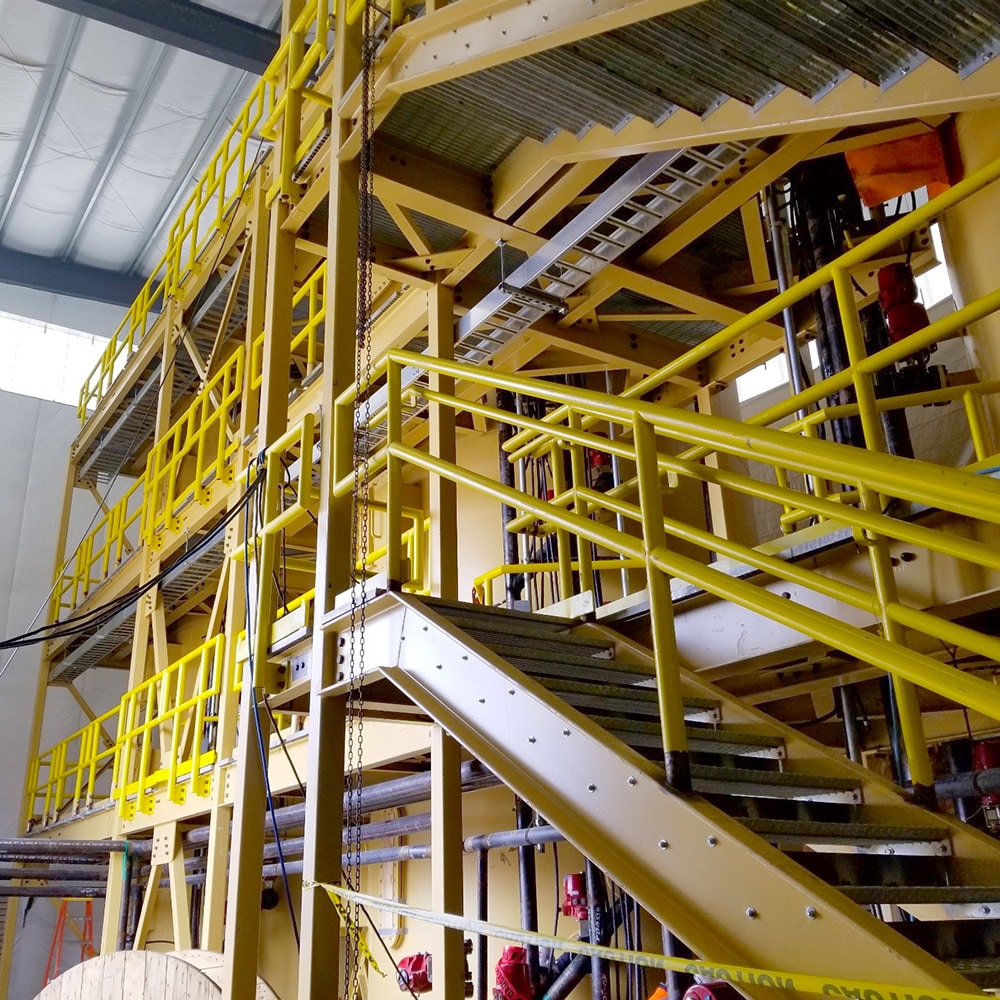
Are You Space Constrained?
When adding an auxiliary or secondary gold recovery application to an existing operation, the space needed to shoehorn an unplanned processing facility into your footprint may be a real concern. For the same nominal flow through a conventional gravity CIC plant, a vertical plant can use up to 55% less floor space and 65% less volume space than a conventional gravity CIC plant. The space saved using a vertical design can fit into floorplans where space is an issue.
Another space-saving measure involves valving. While carbon advance and carbon transfer valving are similar between conventional and vertical CIC Plants, valves are reduced in the vertical configuration because the dart valves or knife gate valves that are used to control flow between stages are eliminated. The reduced valving also saves space in the overall arrangement.
Are You Capital Constrained?
When you think about it, aren’t we all capital-constrained? “Going vertical” can reduce costs because the volume of concrete construction required for containment and the construction of slabs, footings, and stem walls, are greatly reduced by both area and volume. Additionally, cast-in-place concrete can be especially costly at remote sites. The overall smaller footprint required on a VCIC approach also presents cost savings if the plant is located within a structure. The cost to fabricate the vertically stacked columns is less than conventional counterparts, further reducing capital outlay before the commissioning of the plant.
Further cost-saving with VCIC designs is seen in operational costs because the amount of pumping associated with solution recirculation without recovery is significantly reduced. Scavenger circuits have the added benefit of accelerating gold production by removing ounces from recycling back up to the heap leach pad.
Be Aware
While there are many benefits to “going vertical,” there can be downsides to operating a VCIC plant. These may include:
- Operators cannot view the carbon bed fluidization across the entire stage. Site glasses can be incorporated into the design and fabrication, but the view is narrow. A visual check across the entire carbon bed is preferred and is critical when optimizing your operation against preferential flow paths and disproportionate bed expansion. Unfortunately, this is not possible in the vertical configuration.
- Operators cannot dead-bed the stages in the column to physically determine the carbon inventory. Site glasses can again be used, but the measurement will be approximate.
- There is no ability to bypass individual stages in a vertical tank. Maintenance on a single stage in the column is impossible without shutting down the entire column.
- Distribution plates between stages can plug or be damaged. This requires taking the entire column offline to repair. Distribution plates plugging between stages is the most common maintenance issue in VCIC plants.
- These disadvantages should be addressed with your design team before developing your expansion plans.
Summary
The use of VCIC may be particularly attractive if you consider adding carbon adsorption capacity at your site because the capital cost can be significantly lower than conventional CIC plant construction. VCIC systems can function effectively in the right application with the right attention to detail during the design phase and into commissioning and operation. Performing a scoping study and comparing the alternatives may be worth your time determining if this solution fits your budget.
Learn More About VCIC