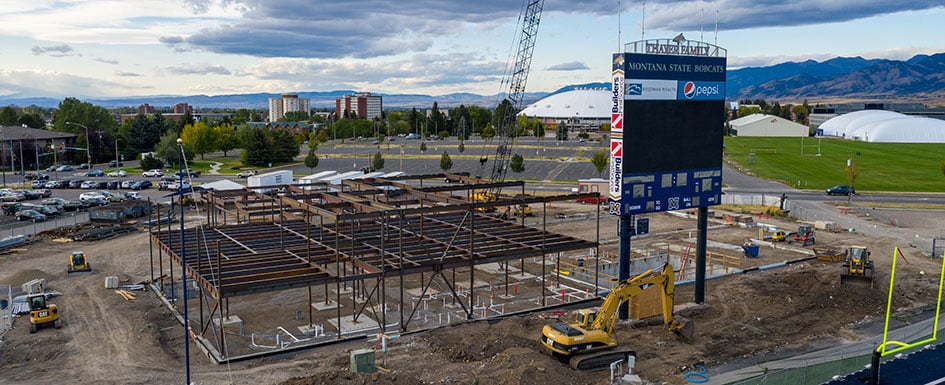
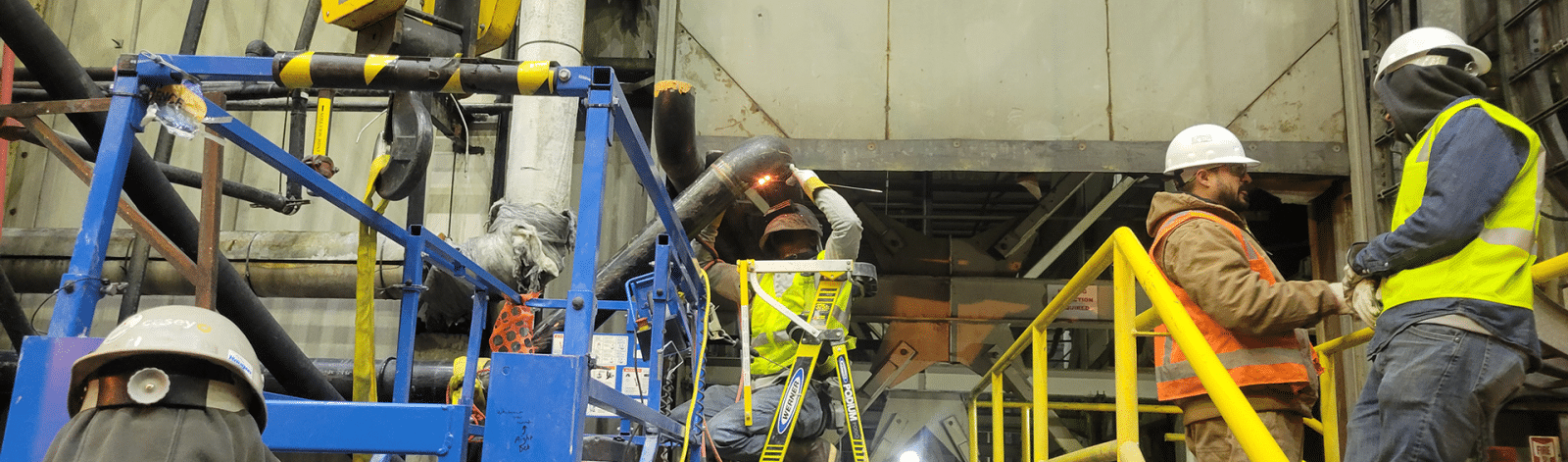
How to Develop a WPS
While developing a WPS can be time consuming and detailed, taking steps to get it right will pay off in the end
A properly developed Welding Procedure Specification (WPS) will not only help welders create a reliable and acceptable weld, but it will also streamline the process, reduce costs by increasing efficiency, and minimize the need for repairs. While developing a WPS can be time-consuming and detailed, several critical elements are required to create a comprehensive, clear, and consistent document.
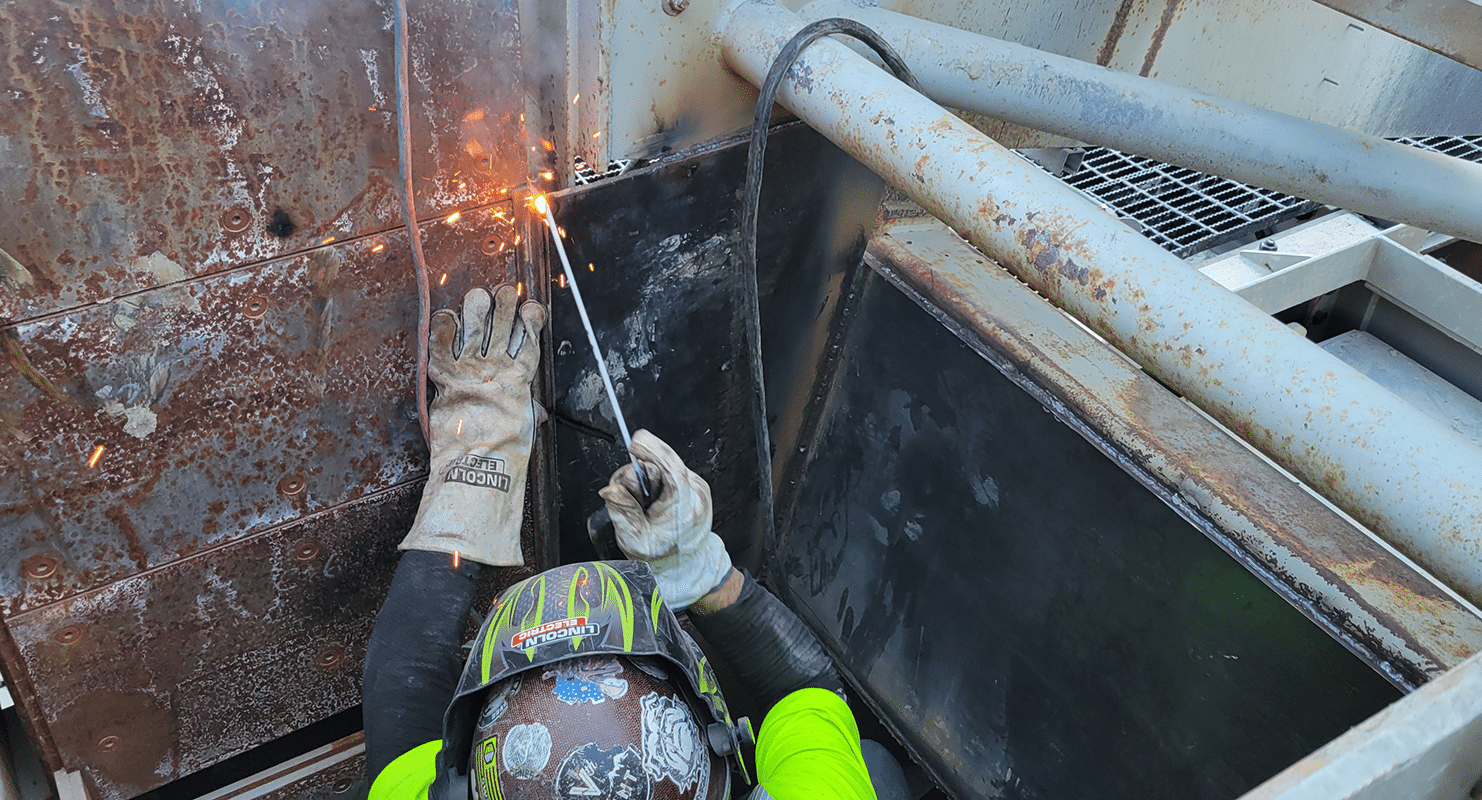
Know the WPS Code
When developing a WPS, developers—or those creating the WPS—need to know which code it must follow. After determining the correct code, look at the welder’s capabilities and the efficiencies of each welding process to choose the correct approach.
After you’ve determined the correct code and decided which weld process(es) to use, developers should consult any historical data they have. For example, a developer may have several Weld Procedure Qualification Records (PQR) on file, providing them with the testing and backup information required to write a new WPS. Or, they may have an existing WPS that meets the criteria for the project. At the same time, review the code you are working with to see if a Prequalified WPS meets the code requirements for your project.
If the code used on your project allows for a Prequalified WPS—and the process meets all the essential and non-essential variables specified in the code book’s Prequalified WPS section—follow the code and list all essential and non-essential variables on the WPS form. The advantage of a Prequalified WPS is that if you have a working WPS, you won’t have to spend time and money on the testing required to develop a new one.
What's the difference between WPS and PQR? Learn more here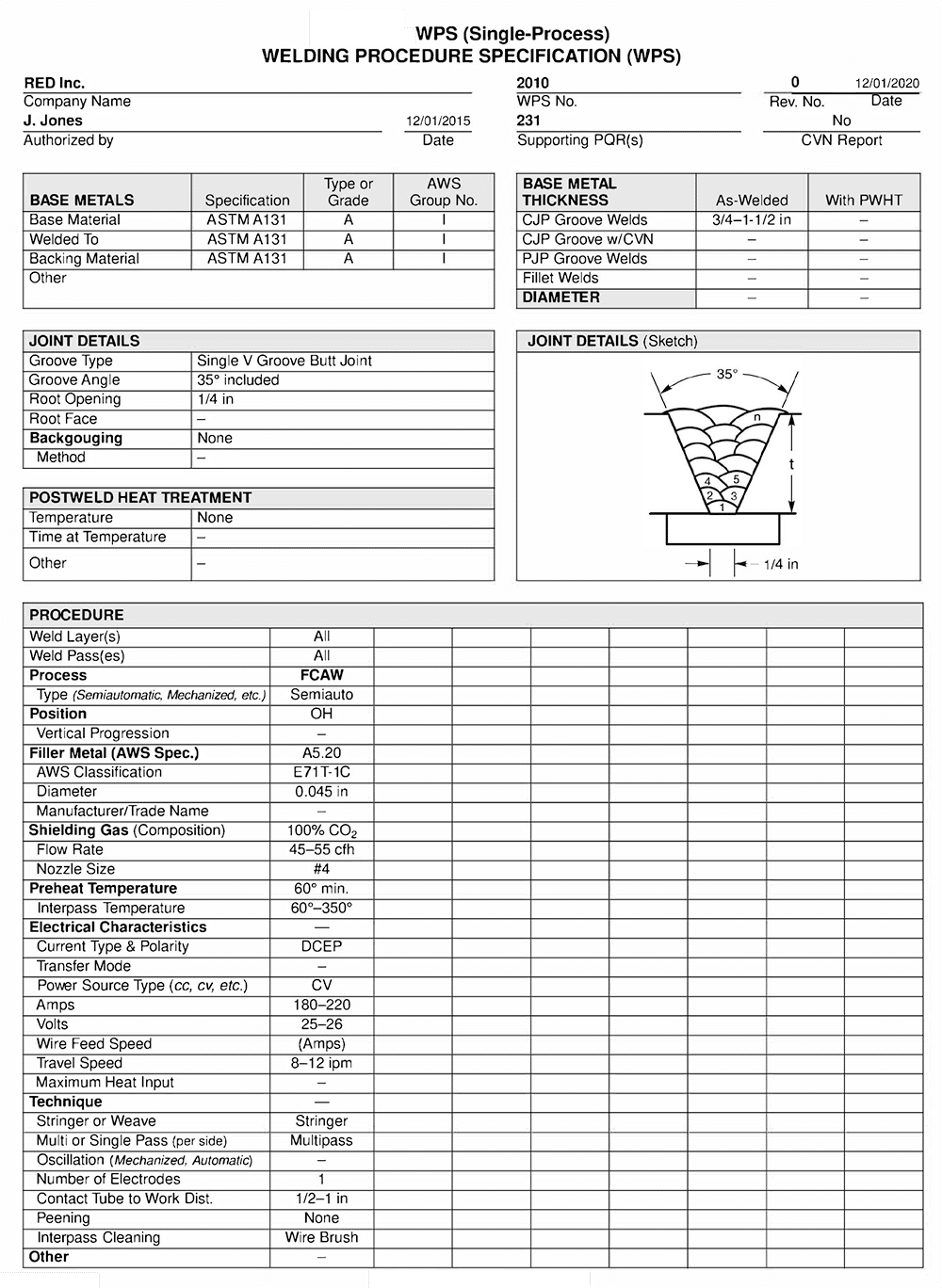
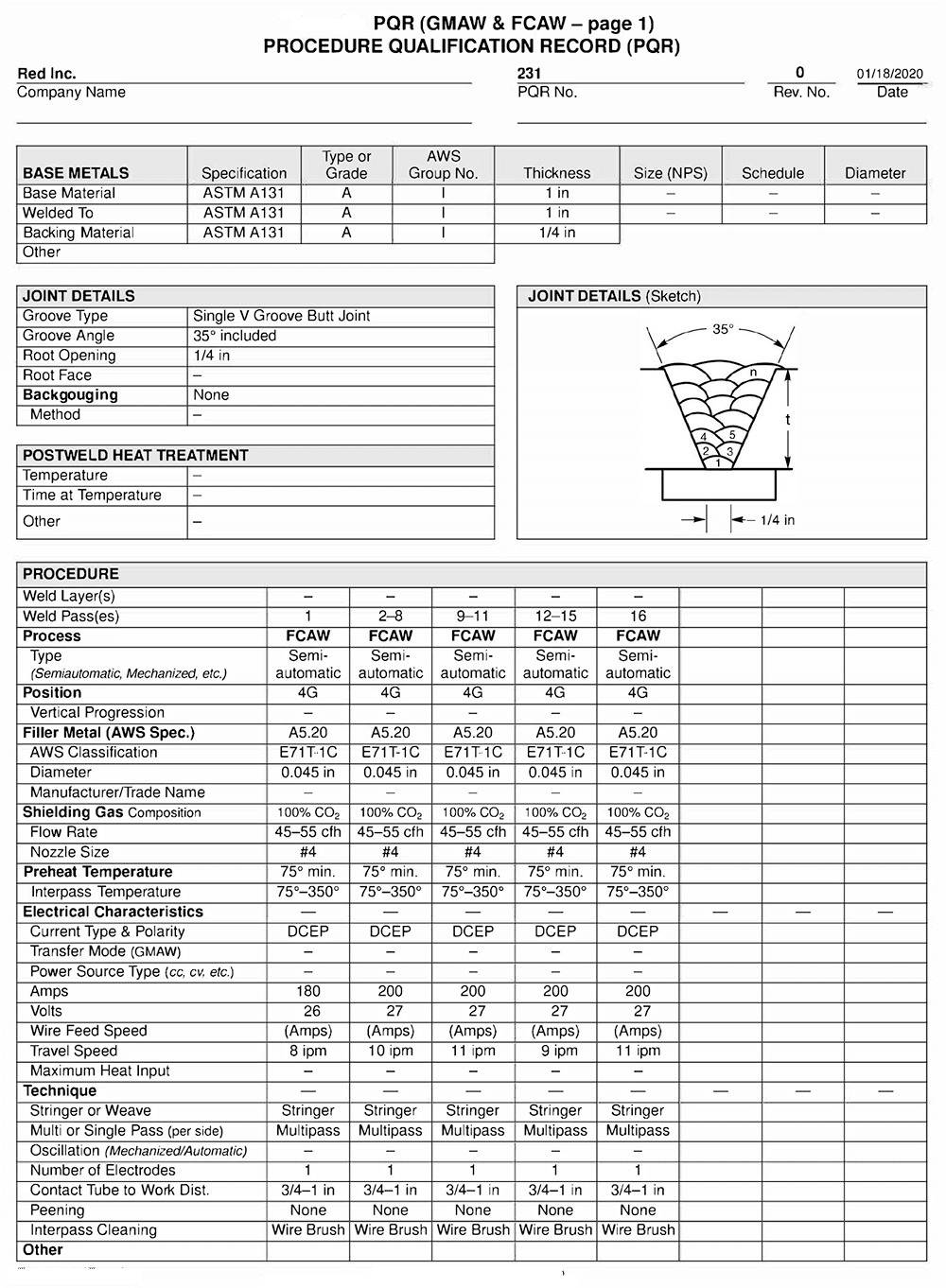
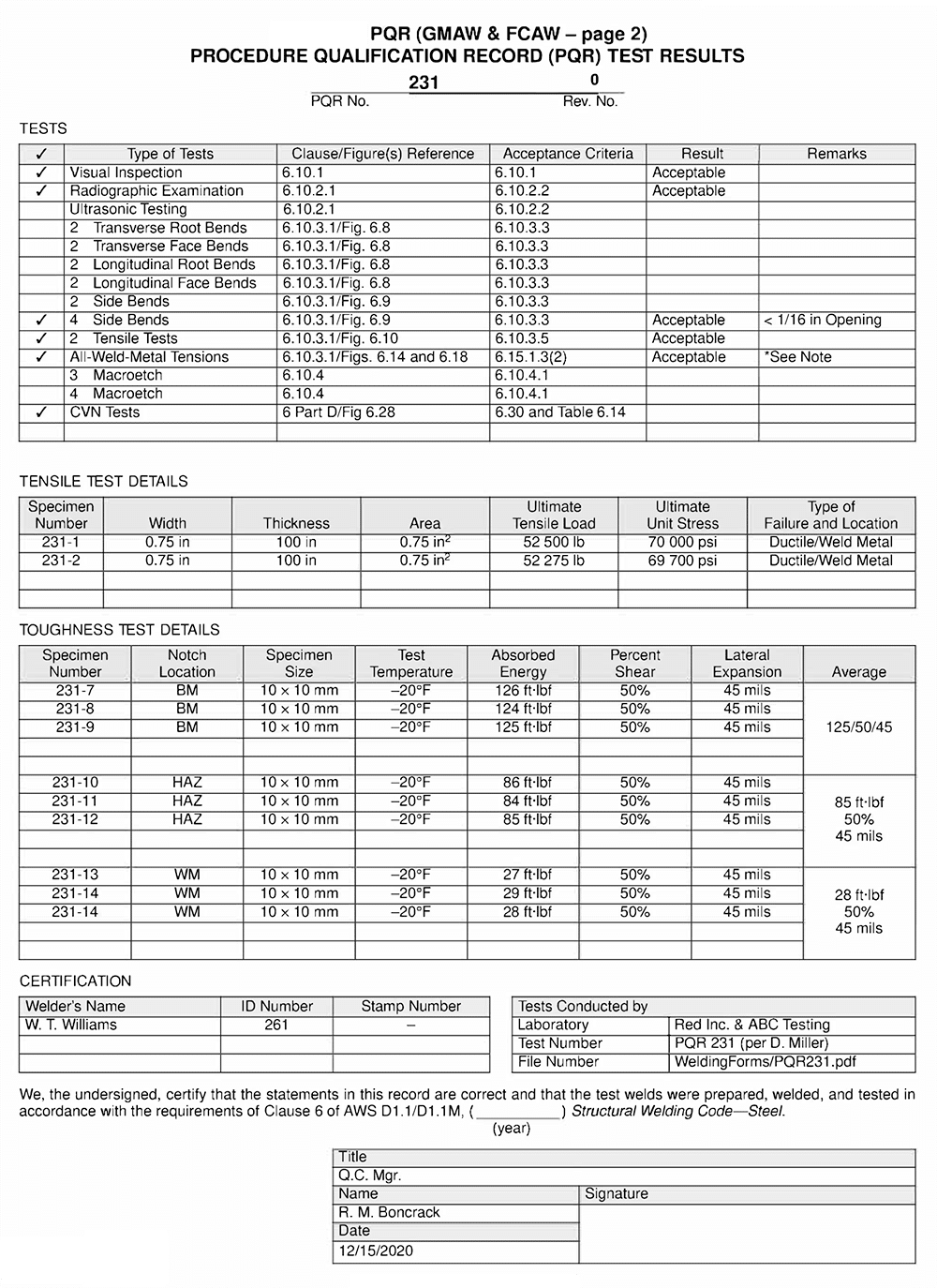
No Data? No Problem
Let’s say a developer has no historical data and a Prequalified WPS and Standard WPS do not meet the project specifications. What now?
The best approach is to determine the essential, nonessential, and supplementary variables required by the code you’re using, develop a pre-WPS to help with welding the test coupons, and write a Procedure Qualification Record (PQR).
For example, let’s say you are using the D1.1 2015 code book. The qualification requirements in this code are in Clause 4 Part B. Part B has a section for each part of the WPS qualification and directs you to tables corresponding to each part of developing and testing a WPS (The tables used in this clause start at Table 4.1 and go through Table 4.9). This clause also has all the figures for welding positions, test plate dimensions, test specimen dimensions, and dimensions for testing apparatuses.
After reviewing the code requirements, you will enter all the essential and non-essential variables and supplementary variables if CVN testing is required. At this time, the pre-WPS should include the following:
- Base metal
- Backing metal if required
- Joint details and geometry
- Single-sided or double-sided weld
- Filler metal specification and classification
- Amps
- Volts and travel speed
- Shielding gas and composition
- Flow rate
- Cup size
- Type of flux
- Pre-heat and post-heat requirements
- Weld position
- Electrical characteristics including transfer mode and type of current
- Weld technique
- CTWD
- Peening
- Interpass cleaning
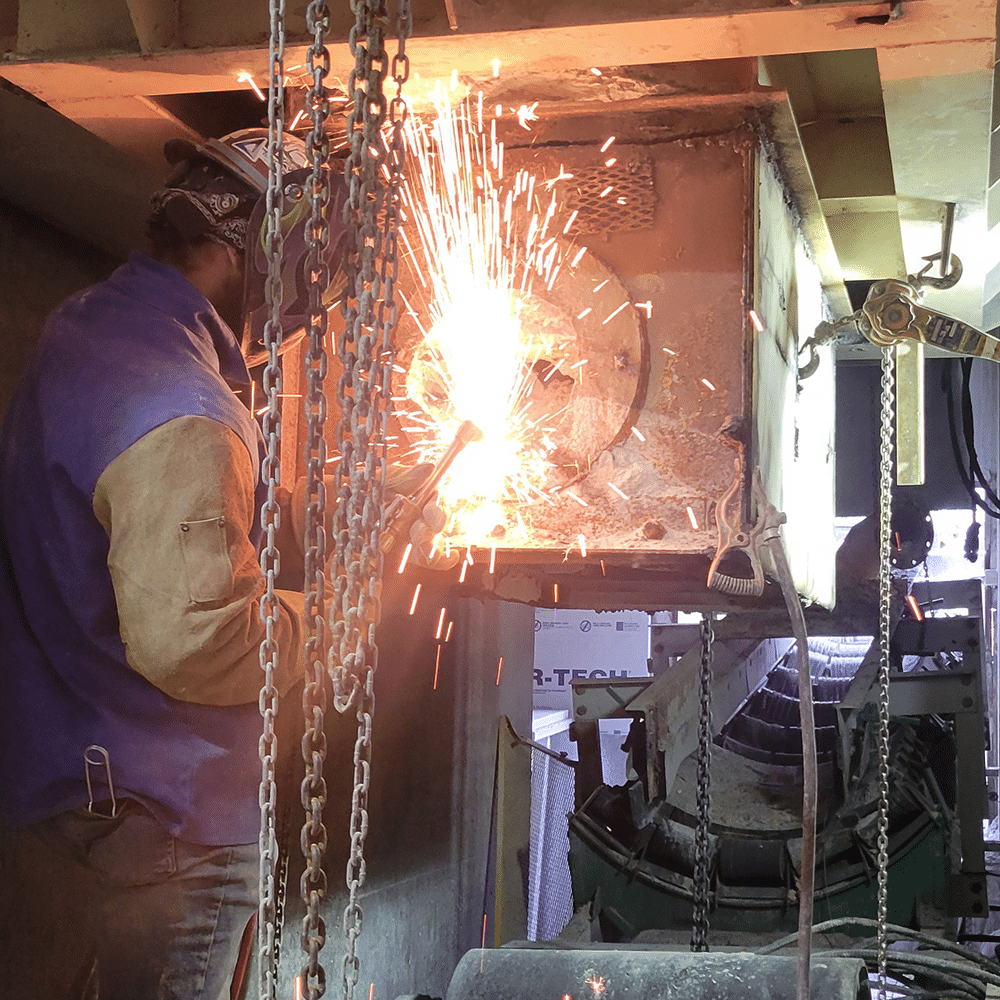
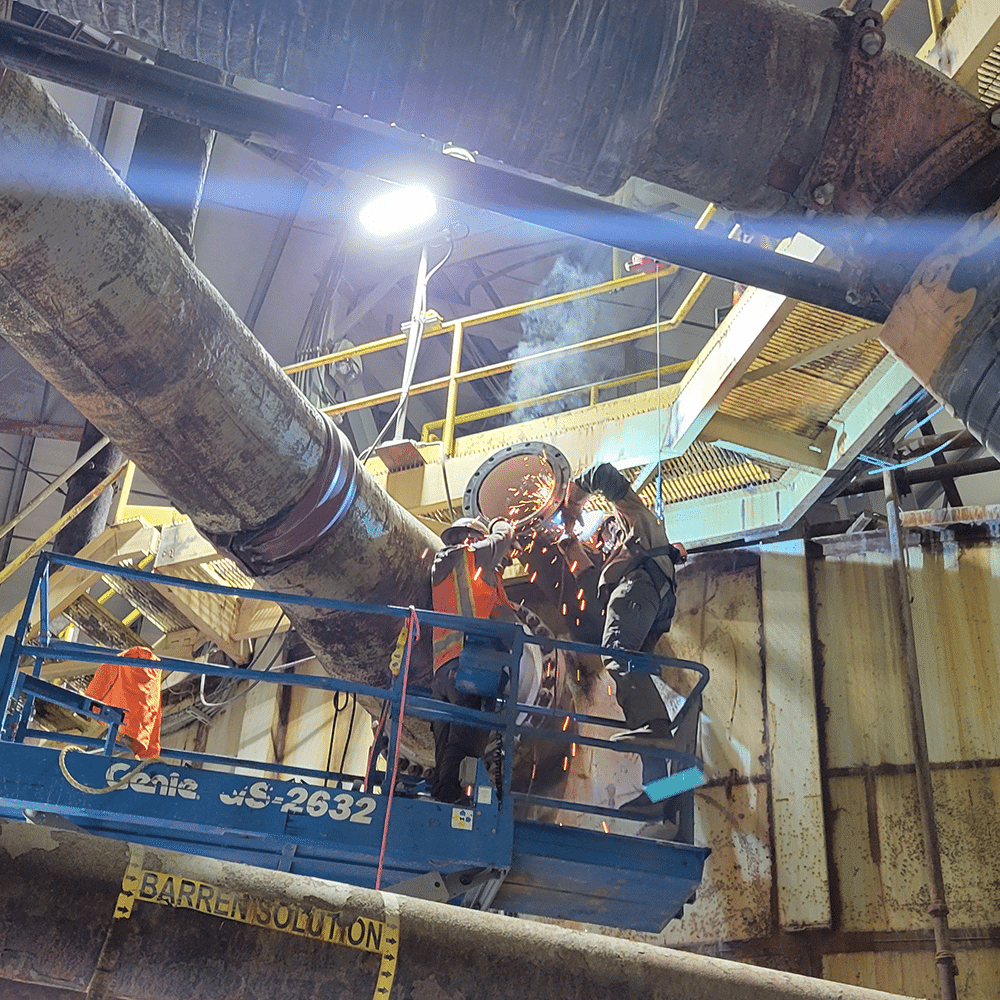
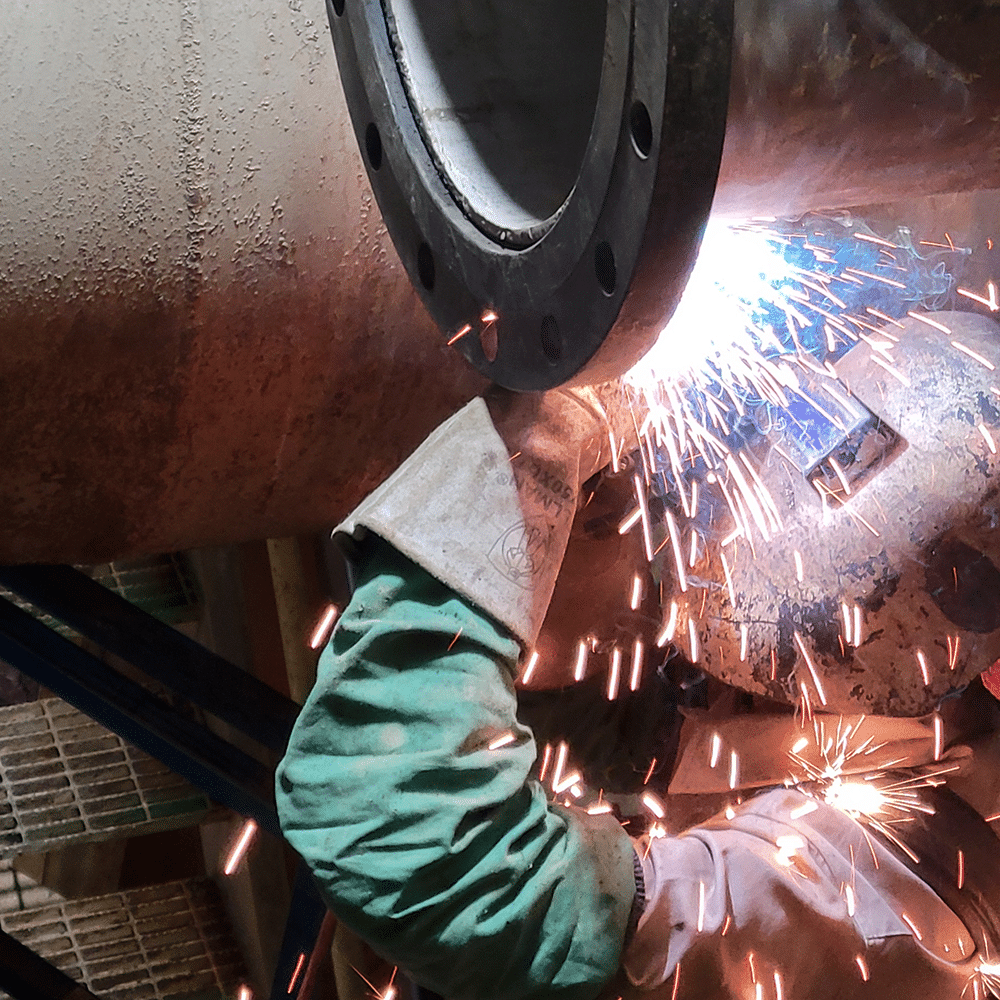
Once the welder begins welding the test plate using the pre-WPS, all the real-time data observed during the test coupon welding must be recorded. This data should include:
- Weld position.
- Power source.
- Polarity.
- Voltage.
- Amperage and travel speed for each pass (each pass should be numbered for ease of tracking).
- Weld material thickness for each process.
- Preheat and interpass temperatures.
- Electrode or wire used.
- Gas composition with flow rate and cup size (along with contact tube to work distance when gas is used).
- Weld technique (stringer or weave).
- Interpass cleaning and peening (if used with any post-weld treatment, they may have been used while welding the test coupon).
At this point, the welder has welded the test coupon following pre-WPS, and the welded coupon has passed the visual inspections. The test coupons can now be sent to the lab for testing. The lab will perform radiographic or ultrasonic testing, root bends, face bends, side bends, tensile tests, macrotech testing, and CVN testing if required. When the lab returns the test coupon and all the destructive test results—and they have met the code requirements—developers must record all the real-time data from the nondestructive and destructive testing data in a PQR.
Developers should review all the real-time data collected during the welding of the test coupon and from lab testing, determine the voltage, amperage, and travel speed ranges, and prepare the final WPS based on the data collected. Once the final WPS has been written, the owner will present it for review and approval before sending it into production.
Our Certified Welding Inspectors Can Help
Our team of certified welding inspectors (CWI) and engineers at Morrison-Maierle is more than willing to assist you during the WPS development and review process. Please call or email us to see how we may assist you in your welding endeavors.
Contact us to learn more